Milled DSI: An Alternative to Converting/Closing Your Plant
April 30, 2013
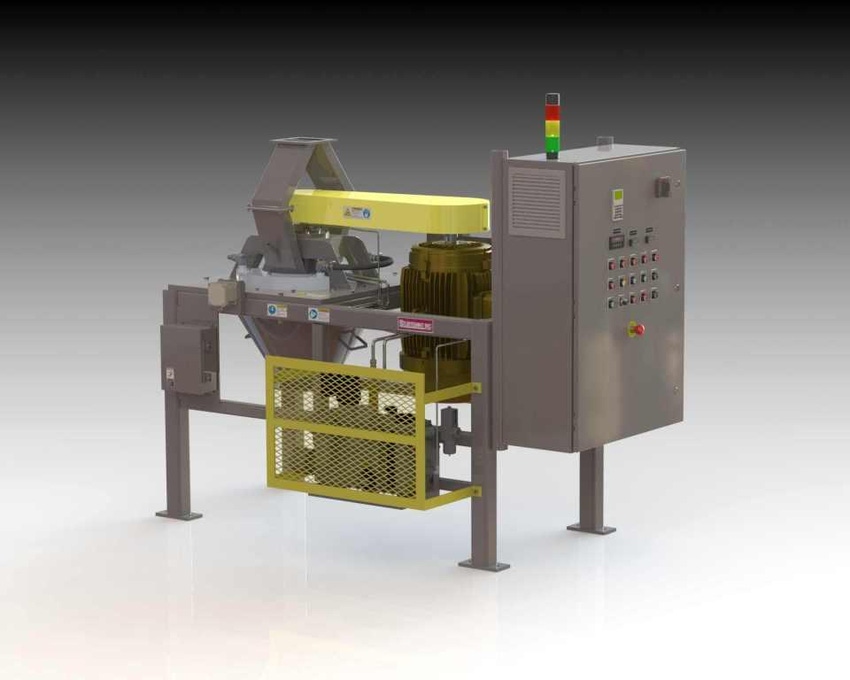
Fueled by constant EPA pressure, unpredictable legislation, and the natural need to lower air pollution levels, coal- and oil-fired power plants and industries alike, are turning more and more to early plant retirement, or conversion to “current” cheap natural gas as a solution to lowering their stack emissions. According to some reports, this, along with adding emission controls to keep some existing coal-fired plants on line has, in fact, lead to pollution level numbers at low levels not seen since the late 1990s.
Early plant retirement is a popular choice of late (for some older coal-fired power plants) for a number of reasons beyond the scope of this article. Conversion to natural gas or early plant retirement can, of course, be an effective way for power companies to comply overall. This is mainly and obviously, because adding wet scrubbers and/or other elaborate emission control equipment as an alternative, can be extremely expensive, and doing so to a plant that is rapidly ageing just does not add up dollar wise.
However, with that said, there is a hidden cost to both the plant’s and the country’s economy in general for both of these choices, in particular job loss when plants are closed and the fact that natural gas prices may rise in the future, and the cost to convert to gas and perhaps back to coal if prices rise too high, too fast, may, in fact, be a more expensive choice for all of us in the long run.
One alternative to avoid some of these issues is to use Dry Sorbent Injection (DSI) to comply to regulations and/or reduce pollution emissions. DSI when used with Trona or the SBC alkaline sorbents reduces So2, So3 and HCLs to conforming numbers with a cost-effective operational cost and low initial capital investment, and allows an older plant to continue its contribute to the power grid, while saving jobs and avoiding the natural gas conversion costs and the future unknown fuel/gas cost impacts. Along with these alkaline sorbents, others like Amended Silicates or Powdered Activated Carbon (PAC) can remove mercury as well. These sorbent when milled on site to a fine particle size distribution (PSD), can reduce So2, So3 to 90%, and HCLs further. Milling Trona, SBC, and Amended Silicates in a blow-through style pin mill has proven to function extremely well to have blue plumes (So3) and acid rain (So2) and HCLs virtually disappear.
Integrating DSI into an existing plant will cost only 10% of what a wet scrubber system would cost and provide conforming So2, So3, and HCL numbers. Applying DSI into a properly selected injection point (correct temperature to be considered), with a pre-tested atomized injection rate, and using reliable on-site milling, will achieve this goal quite easily. With this solution, power plants and industrial sites can retain the maximum amount of flexibility to the constantly changing regulations and compliance dates, and save hundreds of jobs at the same time.
The Sturtevant pin mill has played a key part in the success and industrial development of milled DSI with 58 Simpactor pin mills sold into the DSI industry as of March 2013, for use at coal-fired power plants. This includes eight site-testing rigs with eight different DSI System installation companies throughout the U.S. The first specialized DSI FGT Sturtevant mills date back 12 years, and this specialized mill has constantly evolved ever since.
Effective milled DSI is possible largely because of the many years of successful installations of non-milled lime sorbents and because of the twelve years or so of Sturtevant Trona and SBC mill evolution.
The benefits of using a pin mill offer exceptional milling results. As to milling sorbents, take a look at the mill details that will lead to this cost-effective pollution reduction (this example is based on the Sturtevant model s 6C-30-fgt or 3C-18.5-fgt):
1. Finest sorbent: PSD range from 10 to 15uM d50 provides a sorbent low consumption performance and leading So2, So3, HCL removal for milled DSI.
2. Lowest use of power due to five different model configurations - only 40 hp for 4000 pph (100 pph per hp).
3. Highest milled/DSI throughput available - up to 15 tn/hr of d50 15uM sorbent
4. Cool mill design to keep Trona and SBC well below 120ºF for best process use (popcorn effect/maximizing surface area and pore surface area in the plant process where needed)
5. Least material buildup inside the mill. Trona and SBC are hygroscopic. The design of this mill helps increase the operation time of the milling. 100% automated mill internal cleaning.
6. Lowest wear rate of mill internal parts available. Trona has 0.5 to 1% silica included as injected. This can wear a mill out inside if not properly protected. Properly protecting a mill will lead to low maintenance and long-running durations.
7. Best suited for 24/7 adverse climate operation. All mill functions are monitored. Special design considers extreme cold start-up temperatures and extreme hot operation environments.
In conclusion, consider milled DSI as an alternative to closing your plant or converting your plant prematurely. The job you save may be yours or your fellow countryman’s, and the flexibility gained by staying with coal for the rest of your old power plant's life may be the most cost-effective solution in both the unpredictable short run and in coal’s proven long run.
Steve Coulombe is a product manager at Sturtevant Inc., Hanover, MA. For more information, visit www.sturtevantinc.com.
For related news, articles, and equipment reviews, visit our Size Reduction Equipment Zone
You May Also Like