Laser Level Gauge Aids Ore Crusher Jaws at Nickel Mine
December 10, 2014
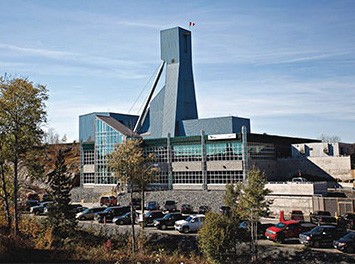
Vale, a global mining company headquartered in Brazil and present in more than 30 countries, recently opened a new nickel mine in Canada's Sudbury Basin in Worthington, Ontario. Called the Totten Mine, it's the company's first in this basin in more than 40 years.
Developed over seven years, the Totten Mine uses the industry's most modern technology, automation, and environmental practices. Environmental facilities include three water treatment plants, enclosed material handling facilities, and progressive closure planning.
When the mine achieves full capacity in 2016, it will produce 2200 tons of copper, nickel, and precious metals per day for 20 years.
In this nickel mining operation, the ore rides on a conveyor to crusher jaws. The jaws must receive an optimal amount of ore at any one time to avoid overloading, jamming, and degraded performance. In choosing an ore level measuring technology to achieve optimum crusher performance, Vale engineers looked for quick response and high accuracy.
According to Jack MacIssac, automation & production leader at the mine, ore levels in the crusher jaws can vary from 8 to 15 ft. "We control the speed of the conveyor belt based on crusher ore levels to prevent jams and overload conditions," says MacIssac. "The ore level gauge* must exist in a rugged underground area, characterized by high vibration and a damp ambient atmosphere."
Solution
Vale engineers selected the ABB LM80 laser gauge to measure ore levels in the crusher jaws. This laser level gauge is a non-contact measuring instrument designed for granular solid materials like ores. Based on pulsed laser technology, it embodies speed and accuracy in a single, easy-to-use-and-install product.
The characteristically narrow (0.2%) beam divergence of the laser permits accurate aiming towards the target surface without interference from surrounding structures.
The gauge's on-board microprocessor calculates distance by multiplying the speed of light by the time it takes for an invisible infrared laser pulse to travel to the targeted ore and back. A second, visible aiming laser helps operators align the measuring laser.
To install the gauge, Vale engineers mounted it on an arm that could be swung out over the jaw opening. This allows any maintenance of the gauge necessary to be accomplished by simply retracting the swing arm back to the operator platform.
Early in its operation, the LM80 gauge measured the base level for the empty crusher jaws. A comparison of the measurement of ore in the jaws with the base level provides the necessary data to control conveyor speeds.
The LM80 gauge requires no software setup. It sends a 4 to 20 mA signal to a controller that continuously adjusts conveyor speed. It also provides relay outputs for ore level alarms.
Results
The crusher jaws at the Totten mine now operates at optimal efficiency, eliminating jamming and overloading.
MacIssac notes that the successful automation of the system avoids manual operator intervention at the crusher. The operator no longer needs be present at the controls.
Vale has since purchased two additional LM80 laser gauges for similar uses, and is considering a trial for a LM200 model gauge capable of measuring ore level at a 600-ft distance for a different application.
For more information on ABB Inc. Level Measurement Products, call 800-858-3847 or visit www.abb.com/level
For related articles, news, and equipment reviews, visit our Instrumentation & Control Equipment Zone
You May Also Like