Contract Manufacturer of Powdered Cleaning Products Boosts Capacity with Ribbon Blenders
December 2, 2013
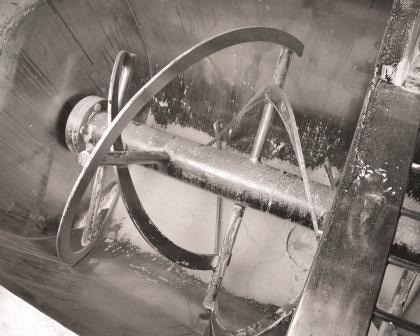
Webco Chemical Corp. is a fully integrated, custom contract manufacturer and packager of powder and liquid chemical products. Founded by Charles Puliafico in 1956, and now in its third generation of private ownership, the company has 75 employees in its modern, 200,000-sq-ft facility.
Webco offers both powder and liquid blending and filling services. Powder products are blended in quantities from small batches to multi-batch production runs, and packed in containers ranging from 4-oz bottles to 55-gal fiberboard drums.
“We blend primarily industrial, agricultural, and household cleaning products,” says Mark Puliafico, president of Webco. “Some examples include metal cleaning and finishing products, household and commercial laundry powders, and cleaning products for dairy farms, including egg-washing cleaners and even a powdered teat dip for cows.”
To meet increased demand, Webco recently replaced its aging blenders with two Munson Model HD-36 stainless steel heavy-duty ribbon blenders, each with a blending capacity of 40 cu ft. “This gives us a total blending capacity of about 90,000 to 100,000 lb per shift,” says Puliafico. “One blender discharges into the fiberboard drums while the other feeds a semi-automatic filling machine. Both blenders run pretty much constantly, and we expect them to remain at the heart of our business for at least the next 50 years.”
Versatility Required for Product Mix
“Our batch sizes generally run from 1000 to 3000 lb, although we occasionally process smaller quantities of specialty cleaners,” Puliafico explains. “The bulk densities of the powders we blend range from 30 to 75 lb/cu ft. The proportions of the materials we need to blend can vary widely, down to as little as 0.05 percent of the final blend in the case of dyes required for coloration.”
Thorough mixing over a range of material proportions is assured by the 2:1-length-to-diameter-ratio design of the double helical ribbon agitator, which subjects every particle of material to agitation during loading, blending and discharge.
The duration of a production run can also vary greatly from product to product. “Some runs can be as short as a single batch, but we often run the same blend for as long as a week before changing to a different blend,” notes Puliafico. “When changing blends, we sweep out any powder from the previous blend, scrape the interior surfaces with the plastic blade, and then power wash the interior of the blender. This takes about 30 minutes. We don’t need to add a separate cleaner because we’re blending cleaning products to begin with. We try to schedule cleaning for the end of the day to give the blender a chance to thoroughly dry before beginning the next run.”
Residual material is minimal due to tight tolerances of 1/16 to 1/32 in. between the ribbon blades and the blender wall, reducing cleaning time between changeovers.
Location Facilitates Workflow
“The blenders are located on the second floor of our two-story building and discharge to the floor below,” Puliafico explains. Bulk materials are stored in silos, from which they are conveyed to a weighing system and then added to the blenders. Materials supplied in smaller bags are added manually according to bag weight.
Although the ribbon blenders are available with internal spray lines for introducing liquid additives, Webco bypassed this option. “Because of the diversity of products that we blend, we have to add different liquids to each one,” Puliafico notes. “We usually add the liquid manually when the powders are partially blended. It takes less time and effort to add manually than it would to clean the spray line when we change liquids.”
The blender maintains a constant speed of rotation regardless of the blend being processed. “A typical batch takes about 10-15 minutes,” says Puliafico. “Materials discharged from the blender are always thoroughly and uniformly mixed and ready to be packaged for shipment.”
One blender feeds blended material to the semi-automatic filling line. The other discharges into fiberboard drums, or into bulk packs that are sent to another department where an automatic filling line can fill as many as 10,000 bottles in an eight-hour shift.
Both blenders are equipped with knife gates. “When the drum reaches its target weight, the knife gate stops the flow of material, the filled drum is manually removed and replaced with an empty one, and the knife gate is reopened,” says Puliafico.
Since the drums are filled directly from the blender, the number filled per shift depends on the time it takes to blend a batch. “This can vary from 20 to 40 minutes, including the time it takes to load the recipe and empty the blender,” says Puliafico. “If the process were continuous, we could fill about 25 to 30 drums per hour, or 200 to 240 per eight-hour shift,”
Webco worked with Munson representative, Tom Murray of Armac Inc., Lynnfield, MA, and the Munson engineering department, which tested Webco's products in its laboratory blenders.
For more information on Munson Machinery Company, Inc., call 315-797-0090 or visit www.munsonmachinery.com.
For related equipment reviews, articles, and news, visit our Mixers & Blenders Equipment Zone
Click here for information about International Powder & Bulk Solids Conference & Exhibition
You May Also Like