Product Packaging Accessory Drives Sales
June 8, 2012
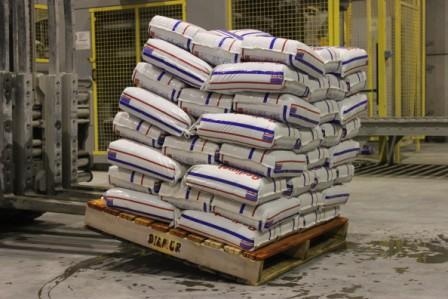
Established in 1999 and located in the port of Antwerp, Belgium, Diamur is a producer of cement mortars. With a capacity of about 700,000 metric tons a year, the plant produces product in bulk silos and 25-kg bags. The company has become a leading producer by developing a reputation for quality and user-friendly products. Quality is not only recognized in the product itself, but also in the manner in which it is packaged, palletized, and shipped. Quality is also noted by the company’s commitment to ecology and the use of recyclable materials.
Customers benefit from Diamur’s innovations by receiving perfectly stacked, decorated bags with a minimum of plastic wrap. More importantly, the pallets of products stay stable even after the plastic has been removed and anyone who has had to restack a pallet or clean up the cement spilled from a broken bag appreciates this benefit.
Diamur started producing its primary bag size, 25 kg, in 2008 and currently supplies about 80,000 tons per year for shipment throughout Belgium, France, and the Netherlands. These markets include both the professional trade, sold through building material outlets, and the retail trade, sold through do-it-yourself stores.
In the introduction of the 25-kg product, the company wanted the quality of the packaging to represent the quality of its contents and decided to use plastic bags rather than the traditional poly-lined paper bags. “The advantage of plastic packaging is that the mortar keeps longer and can withstand rain (many outlets store the product outside),” says Benedikt Van den Braembussche, Diamur’s president. “It is also easier to recycle, because regular paper bags always contain plastic liners. Moreover, plastic packaging does not release dust which is especially nice for customers.”
Unfortunately plastic bags have some unintended consequences; they are more slippery than paper bags, as the slight coating caused by the dust that is prevalent in the manufacturing environment acts as a lubricant. Pallets frequently fell apart within the palletizers causing major tie-ups in production operations as lines must be shut down to clear the jams. Furthermore, pallets often fell apart while being transported to the stretch hood equipment, a process where a plastic cover is starched around the pallet to stabilize it in transit.
Hot Melt Experience
Diamur initially tried to stabilize pallets with hot melt adhesive, but this also had unintended issues. The hot melt was too aggressive and bags often ripped when they were separated. Even if they didn't rip on separation, the heat of the glue, bag distortion on separation and its adhesive residue made it hard to read the printed copy. In addition, Van den Braembussche says that “since the hot melt contaminated the palletizers, they had to be shut down and cleaned several times a day. This costly process along with the separation issues caused us to discontinue the use of hot melt”.
The problems with palletizer and line downtime, ripping bags, and unreadable text disappeared, but the cement bags were so unstable that each pallet needed two hoods to hold everything in place. And with that the cost per pallet soared, due to the extra hood and the bottleneck that developed in the hooding equipment. Moreover, the pallet load became unstable whenever customers slit the hoods and partial pallets were moved at a construction site. It was also quite awkward in DIY stores whenever a customer pulled on a bag and the whole pallet fell apart.
The Solution
Luckily, according to Van den Braembussche, Diamur’s personnel were introduced to a product called Lock n’Pop, a water-soluble adhesive much like that used in sticky notes, but a product that both loses its tack once it is separated and like sticky notes, leaves no residue on the packaging. Lock n’Pop is available in a number of formulas including corrugated, paper, shrink wrap, and one of which especially designed for plastic bags.
The Process
The two new packaging lines use bag form, fill and palletizing equipment from either Arodo, Arendonk, Belgium or from Haver & Boecker OHG, Oelde, Germany, and pack and palletize up to 80 bags/min. Product travels by conveyor to the palletizers, passing under the air operated adhesive applicators positioned at the entrance to the palletizer. The application system is far safer and simpler to operate than hot melt systems, is fully automatic, and requires little maintenance. The palletizers now run flawlessly without jams or shutdowns due to adhesive buildup. Principally bags are stacked on either EURO pallets or CPI pallets and, depending upon the type of product and the wishes of the customer, are stacked 7 or 8 bags per layer, and between 5 and 9 layers per pallet. Pallets weighing between 2200 3500 lb are moved from the palletizer to the hooding equipment, the final process in the production operation. The perfectly aligned pallets are then moved to the warehouse where they are stored in eye-catching, beautifully stacked, orderly rows.
Improved Stability and Reduced Costs
Initially Diamur opted for a trial installation of the Lock n’Pop equipment to confirm the product claims and evaluate the stability of the final product. “What we immediately noticed was that the stability improved so much, it was no longer dependent on the stretch hood,” said Van den Braembussche. “This is not only easier for the end user but also for our own handling. The pallet load no longer falls apart during palletizing or during transport to the stretch hood machine.”
The company now only uses a single stretch hood with a lower gauge just for extra protection and mainly for dust.
While Diamur is pleased with the improved operations and the benefits it has received with its product’s packaging and handling, it is apparent that its customers are more than pleased. Van den Braembussche concludes, “Seeing the results of improvements we made in our product offering, we have decided to add two new production lines this year, whereby we will at least double our capacity.”
For more information about Lock n'Pop (Everett, WA), call 800-225-5539 or visit www.locknpop.com.
You May Also Like