FIBCs: Prevention of Dust Explosions in Storage & Handling
April 15, 2014
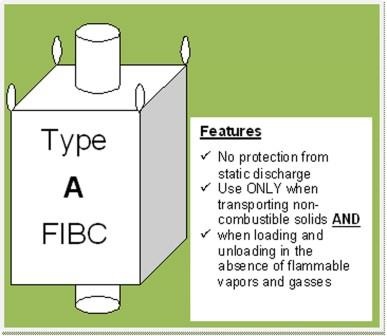
FIBCs are extensively used for packing, storing, and transporting a variety of materials (chemicals, minerals, food products, agricultural products, fertilizers, plastics, cement, etc.) in fine dust, powder, granular, or flake form. The use of FIBCs in industrial applications is ever-growing as they are a cost-effective packaging and transportation means. However, there are associated electrostatic ignition hazards that one should be aware of when using FIBCs for packaging and transporting combustible/explosible materials and/or when flammable gases and vapor atmospheres are present.
Electrostatic Discharges
Electrostatic charge generation normally occurs due to the process of contact and separation which takes place between individual powder particles and the conveying equipment upstream of the FIBC during filling and between the powder particles and the internal surfaces of the FIBC during emptying.
The types of discharges that may occur due to the buildup of electrostatic charge on the FIBC include:
* Brush discharges from the surfaces of standard insulating FIBCs and liners. Brush discharges can ignite flammable atmospheres requiring up to approximately 4mJ for ignition.
* Propagating brush discharges from the surfaces of insulating FIBCs and liners, which have electrical breakdown voltage greater than 6000 volts. Propagating brush discharges can ignite flammable vapor, gas and dust cloud atmospheres.
* Spark discharges from conductive parts of groundable bags if left ungrounded
What Should I Know Before Selecting an FIBC?
FIBCs should be selected according to the electrostatic and flammability characteristics of contained powders and the presence of flammable gas/vapor atmospheres in the location where they are used. You should know the following:
* Is the powder material being packaged/transported a combustible/explosible material?
* The dust (fine particulates) of most materials used in industrial application is explosible. More than 70% of the powder materials being used in general industries are explosible dust. However, if you are unsure whether your material is explosible or not, a Go/No Go explosion screening test in accordance with American Society for Testing and Materials (ASTM) E1226-12a: “Standard Test Method for Explosibility of Dust Clouds” can be conducted to determine if the material is explosible or not.
* What is the Minimum Ignition Energy (MIE) of the dust material?
* The minimum ignition energy (MIE) is the lowest electrostatic spark energy capable of igniting a dust cloud. The test (conducted in accordance with ASTM E2019) is used primarily to assess the potential vulnerability of powders and dusts to ignition by electrostatic discharges.
* Are flammable gases/vapors present in the area?
* The operation involving the FIBCs should be evaluated to determine if flammable gases/vapors could be present in the area. In some cases, the powder material being packaged might release off-gases over time which could be flammable or powder may be directly transferred from the FIBC to a vessel containing a flammable liquid. Hence each case should be thoroughly evaluated to determine the presence of flammable gases and associated MIE.
* What are the electrostatic characteristics of powder materials?
* For materials with MIE <25mJ, it is also important to know the ability of the powder particles to generate (Electrostatic Chargeability test conducted in general accordance with ASTM D257) and retain (Volume Resistivity and Charge Relaxation Time tests also in general accordance with ASTM D257) electrostatic charges during processing, filling and emptying conditions. This information can be utilized to determine the possibility of generating electrostatic discharges (an ignition source) from the material itself during filling and emptying of FIBCs.
Types of FIBCs and Selection Criterion
There are currently four types of FIBCs: Type A, B, C, and D.
(seeimages)
Important Notes
* If left electrically ungrounded, type C FIBCs (groundable bags) can give rise to a higher explosion risk than type A and B (insulating) FIBCs.
* It is not possible to make general recommendations for the safe use of type D FIBCs under all operating conditions. In particular:
o The existing type D FIBCs that incorporate antistatic yarns and an antistatic coating can still create a localized electrostatic field around the FIBC. Ungrounded conductive objects that may be present in the close proximity of such charged FIBC could become polarized and become charged by the process of induction. Such charged objects could give rise to subsequent spark discharges which could be a potential ignition source. Hence it is recommended that conductive objects in close proximity of type D FIBC need to be electrically grounded.
o Incendive sparks may occur during filling and emptying of type D FIBCs if the surface of the FIBC is partially covered by an electrically conductive substance (e.g. a wet patch).
* Irrespective of the type of FIBC used, and depending on the electrostatic properties of the powder and the powder handling equipment (for example, whether the plant is conductive or insulating, grounded or ungrounded) other electrostatic ignition sources may still exist.
* Conductive powders (having volume resistivity < 106Ohm.m) could accumulate electrostatic charges in type A, B, or even D FIBCs (in the absence of direct ground connection), it is recommended to use only type C FIBC with conductive powders to avoid spark discharges from the powder material itself.
Use of Inside Liners in FIBCs
The use of liners in any type of FIBC can increase the risk of an electrostatically initiated flash fire or explosion. There are three types of liners that are permitted to be used in a particular type of FIBC depending on the electrostatic properties of the liner material. Depending on the liner type, the following physical and electrostatic properties may need to be determined ensure the suitable type of liners:
* Surface Resistivity
* Breakdown Voltage
* Liner Thickness
* Resistance to Groundable Point
These tests results provide valuable information that will be utilized to determine the safe use of a particular type of liner with a specific type of FIBC.
Qualification Criterion for Liners inside the FIBCs
Type L1 Liner
A type L1 Liner should meet the following criterion:
* Made from materials with Surface Resistivity on at least one surface ? 1.0x107 Ohm per Square,
* If the material is multi-layered, or if the material has outer surface with Surface Resistivity >1.0x1012 Ohm per Square, Breakdown Voltage through the material shall be < 4KV
* If the material is multi-layered, or if the material has inner surface with Surface Resistivity >1.0x1012 Ohm per Square, Breakdown Voltage through the material shall be < 4KV and Thickness shall be <700 micrometer
Type L2 Liner
A type L2 Liner should meet the following criterion:
* Made from materials with Surface Resistivity on at least one surface between 1.0x109 and 1.0x1012 Ohm per Square.
* If the material is multi-layered, or if the material has outer surface with Surface Resistivity >1.0x1012 Ohm per Square, Breakdown Voltage through the material shall be < 4KV
* If the material is multi-layered, or if the material has inner surface with Surface Resistivity >1.0x1012 Ohm per Square, Breakdown Voltage through the material shall be < 4KV and Thickness shall be <700 micrometer
Type L3 Liner
A type L3 Liner should meet the following criterion:
* Made from materials with Surface Resistivity greater than 1.0x1012 Ohm per Square,
* Breakdown Voltage through the material shall be less than 4KV
Selection Criterion for FIBC and Liner Combination
Once the type of a particular liner and the FIBC has been determined (using the tests discussed above), the following table can be utilized to determine the permissible combination of a liner with a specific type of FIBC. (insert chart)
There are additional requirements for labeling and testing a particular type of FIBC. It is advised that a thorough risk assessment should always be conducted before using FIBC in potentially hazardous situations. Selecting and using a suitable type of FIBC and liner combination is one of the important steps to prevent the risk of fire and explosion hazards.
Muhammad Qureshi, Ph.D., is a process safety specialist at Chilworth Global. He provides consulting services in dust explosion and electrostatic hazard assessment and is also responsible for standard and customized electrostatic testing. He is a member of the American Society of Mechanical Engineering. He received his Ph.D. degree in mechanical engineering from the New Jersey Institute of Technology (NJIT) in 2006. Chilworth can help you understand the electrostatic hazards associated with the use of FIBCs by determining the electrostatic characteristics of FIBC, liners, and powder materials by conducting the above mentioned tests in its state-of-the-art ISO-accredited laboratory. Chilworth’s senior process safety specialists can help interpret results and provide specific guidance in regards to the safe use of FIBCs, especially with liners. For more information, visit www.chilworth.com.
For related equipment reviews, articles, and news, visit our Explosion Protection & Safety Equipment Zone
Click here for information about the International Powder & Bulk Solids Conference & ExhibitionReferences
[1] NFPA 654: Standard for the Prevention of Fire and Dust Explosions from the Manufacturing, Processing, and Handling of Combustible Particulate Solids2013.
[2] IEC 61340 Edition 2.0 2012-01: Electrostatics – Part 4-4: Standard test methods for specific applications – Electrostatic classification of flexible intermediate bulk containers (FIBC).
[3] Safety Watch: “FIBC Selection and Safe Use” A focus article by Muhammad M. Rafique Qureshi, published online by Chilworth Technology Inc., Jan 2013.
You May Also Like