What Really Matters to OEMs When Process Weighing is Spec’d in
May 20, 2016
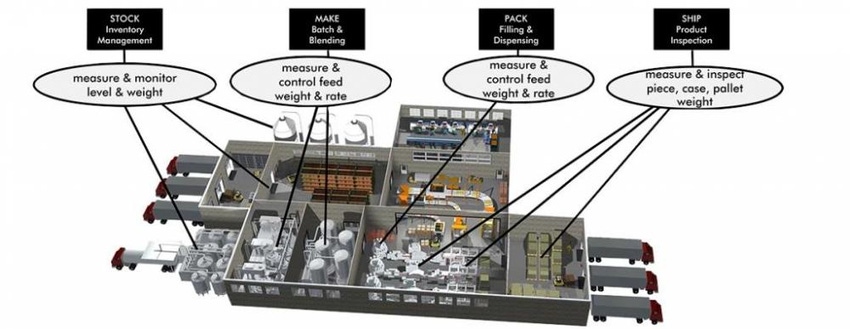
Many OEMs face the constant challenge of trying to differentiate themselves in their markets. There also seems to be an ever-increasing level of competition from a broader base of OEM machine and equipment (skid) builders.
These days many customers seem to have ever fewer projects and smaller capital budgets. On top of that, customers are usually focused on cost first, but never seem to back away from a demand for more functionality. As a result, many OEMs struggle to balance the cost and design demands of their customers.
Furthermore, OEMs know that changing suppliers can be difficult and costly. But, on the other hand, they appreciate that development and innovation are key to maintaining their competitive advantage and satisfying their customers. Process weighing is often a functional requirement on many OEM machines or skids. In fact process weigh is one of the most frequent used process measurement parameters, used more than flow, pressure etc. The same oz/lb/ton of raw material can be weighed several times as it moves through the manufacturing process. By choosing a process weighing partner who can help them not only differentiate themselves, but also face their customers’ cost and design demands, OEMs can help meet these challenges while maintaining profitability.
Perhaps you are one of them? If you design and manufacture industrial automation machines or skids, then you probably know that one weighing solution does not fit all. Building machines with different levels of automation requires solution flexibility. You have to seek out innovative ways to reduce your TCD3 (Total Cost to Design, Develop, and Deliver), while simultaneously shortening the time to market and apply sustainable production practices.
In short, you are trying to help your customers and yourselves:
• Meet your customers’ specification
• Reduce their cost
• Reduce risk for you and your customers
• Differentiate your system
• Maximize your revenue
• Maximize your profitability
Get It Right Early in the Process
Developing, testing, and refining your equipment or skids can be time consuming, and a costly and fast burner of resources. You realize you can’t be an expert at everything. So how do you avoid the trap of spending hours and hours trying to meet tough customer specifications, when you don’t really have deep experience in the area of process weighing? A good answer might be to partner with a process weighing expert and leverage their expertise, experience, innovation, and solutions. Take a shortcut to the best, easiest solution, and reduce both your development cost and time to market. Getting it wrong has always been easy. Getting it right first time using a good partner is a far better option.
A specialized process weighing partner can help you establish which weight measurement and/or control products best suit your application. They can also guide you through their best practices for installation and integration. The resulting solution is simplified, easier to use, and customized to meet the business needs of your customer. And it will deliver the least total cost.
Apply the Right Techniques for the Best Result
There are generally four areas in the manufacturing process where process weighing is integral and process weighing specialist excel. Best summarized as where manufacturers stock, make, pack, and ship their raw materials and finished products.
1. Inventory Management (Stock)
Accurate inventory management of raw materials in storage silos, vessels, tanks, bags, or on pallets is a challenge faced by many manufacturers. Using weight measurement techniques over level sensing techniques to manage the inventory of materials improves accuracy and helps deliver just in time and bottom line results. OEM equipment builders for this area will likely encounter and deploy the following inventory management applications and techniques.
Measurement or Level by Weight: Measuring level or inventory by weight is widely accepted to be the most accurate technology. The weight is not affected by ingredients that foam or settle unevenly, by changes in density, internal mechanical bracing or shape of the tank. Weight is weight, regardless of percent solids, bridging, ratholing, or whether your ingredient is conductive or sound absorbing. Because weighing is a non-contact method of measuring level, there is no chance of contamination.
Stock Control by Weight: Weight instrumentation can also maintain a level or level range in a vessel. For example, a “low” setpoint can initiate a refill of the vessel so as not to run short of the material, while a deadband or second “high” setpoint insures a high level or illuminates an overfill condition, even while its contents are in motion.
Throughput or Totalizing Weighing: An automatic throughput bulk weighing system utilizing a PLC and a weight controller is designed to control incoming or outgoing material in a manufacturer’s shipping and receiving operations. The system measures and stores draft requirements, totals, tolerances, and individual weight compensation offsets for multiple separate materials. The system analyzes weight data generated by load cells to accurately measure and totalize the flow of the bulk material
These techniques are usually found in one or more the following applications:
Vessel & Silo Weighing: Weighing vessels and silos with legs in compression or suspended in tension is generally accepted as the most accurate and repeatable method to measure their contents, especially for inventory purposes. There are many factors to consider in vessel weighing, such as size, type of vessel, support structure, piping, movement, and environmental (temp, wind, etc.) to name a few.
Bulk Bag Weighing (IBC): If a manufacturing process uses intermediate bulk containers (IBC), ensuring the total weight of raw materials that goes in or comes out of them is critical. High resolution and fast update rates are needed to ensure precise cut-offs in the filling or dispensing processes to insure accurate weighments. IBCs are typically used for loss-of-weight application. IBCs are suspended by load cells to weigh the material dispensed into receiving containers. Specialized filler/dispenser weight controllers can open and close the discharge gates while weighing the loss of ingredients. Empty IBCs are often exchanged before the desired weight is met. A dispenser/filler that retains the amount dispensed from the first IBC in memory knows how much material is required from the second IBC to complete the desired weight. Without this feature, material is wasted by not completely emptying the IBC or by over filling when switching.
Floor, Pallet, Bench Scales: Used to collect inventory weight data from raw materials that are stored and transported in containers of various sizes and weight.
2. Batching and Blending (Make)
Batching
OEM’s that manufacture process equipment/skids for batching systems in this second manufacturing area will know that a batch process can involve sequentially feeding one material at a time (using gain-in-weight) or simultaneously feeding multiple ingredients at a time (using loss-in-weight) into a mixing vessel. Thereafter, the batch is dumped into a finished product holding tank or into a downstream process. The vessel can be a simple hopper, tank, or reactor. It could have a built-in mixer, an agitator, or heating and cooling jacket. Ingredients are conveyed, extruded, vibrated, pumped, hand delivered, or gravity-fed to gates or valves above the vessel. Applying good process weighing practice ensures the accuracy of each feed completed, the quality of every batch made, making lives easier for the folks in manufacturing and quality control.
Batching by Weight: Whether deploying process weighing techniques of gain-in-weight (GIW where the vessel receiving the material is the scale) or loss-in-weight (LIW where the vessel feeding the material is the scale), a precise measurement of each ingredient, as called out in the recipe, is critical for each batch manufactured. Just a fraction of a percentage off target and a batch could be ruined, wasting precious money and resources. Introducing batch weighing into the process involves sequentially or simultaneously adding ingredients into a vessel by weight and then discharging the batch (sum of all the ingredients) to downstream processors.
Batching by Weight & Rate: This method is often used to control process reactions in reactors. It is a combination of “loss-in-weight” (LIW - which controls the amount fed) and "loss-of-weight" (LOW - which controls the rate of the feed). LIW and LOW applications allow multiple ingredients to be added to a single vessel at the same time. Closed-loop rate controllers are for use in a variety of applications, including auger, belt, and vibratory-based feeders, converting them from volumetric to gravimetric.
Blending
OEMs that manufacture process equipment/skids for blending processes generally use the LOW technique to continuously and simultaneously stream raw material into a process. In some cases, the LIW technique is added to blend a very long batch.
Blending by Rate: Many manufacturing plants depend on continuous conveyance systems and feeders to transform raw materials into finished goods. OEMs typically offer continuous belt or hopper feeders to satisfy their customers’ needs when “in motion” raw materials need to be weighed to ensure the ingredient mix is correct and that the finished goods meet quality standards. This is a "loss-of-weight" application where multiple ingredients from multiple scales are added to a process at the same time. Weight by rate is the measurement of an amount of a material which enters into or is dispensed from a vessel over a given period of time. Solids, liquids, or gases can be monitored or precisely controlled using screw- or auger-based feeders, vibratory feeders, conveyors, belt feeders, variable valves, and pumps.
3. Filling and Dispensing (PACK)
In this the third manufacturing area, OEMs offer fast and precise filling or dispensing machines to deliver finished product into receiving containers. Weighing one again is one of the best methods to use and provides accurate and repeatable results. For filling, the GIW (gain-in-weight) technique is typically deployed where the scale is under the container. For dispensing supply bins (IBCs, totes, etc.) using a loss-in-weight technique where the scale is above the container.
Gross/Net Weight Filling: Filling consists of putting material on or into the scale as a GIW process. The container receiving the material can range from small cans, bottles, boxes, or bags to tanks. Gain-in-weight systems use load points (load cells and mounting hardware) or platform scales to weigh the material being received into a container. An empty container is placed on the scale and its weight is tared, so that only the net weight of the material going into the container is displayed. Weight controller instrumentation opens and closes vessel discharge gates while weighing the addition of the ingredients. Conveyors are often used to move receiving containers through the process.
Net Weight Dispensing: Dispensing (or dosing) consists of taking material off or out of the scale as a LIW process. Supply bins in LIW applications are suspended (tension) or supported (compression) by load points to weigh the material being dispensed into receiving containers. Weight controllers can open and close the discharge gate or control the rate of flow from a feeder, while precisely weighing the loss of material from the scale (LOW). Relays in a weight controller are set to automatically refill the supply bin when a programmed weight is reached.
Piece/Portion Weighing (bench): High resolution and fast update rates in bench scales or floor scales allow small parts, portions, or pieces to be weighed for retail packaging. For example, metal parts in a package, chicken parts in a grocery package, and produce in a bag are often weighed as they are packed. Industrial weighing instrumentation can also provide simple piece counting.
4. Product Inspection (SHIP)
In the fourth and final production area, OEMs and machine builders often are involved in developing machines for the product inspection and shipping processes. Weight controllers, load cells, and platform scales are used to weigh containers to confirm that they have been filled to the proper level or that they contain the correct number of parts. Check weighing can be used for a wide variety of applications, including verifying package contents, checking product tolerances, identifying parts, classifying product, and checking for overload safety. Other applications in the ship category include the last steps before shipping finished goods, such as weighing pallets of product to calculate shipping charges.
Check Weighing (static/dynamic): You can use an automated check weighing process for a wide variety of applications including verifying package contents, checking product tolerances, identifying parts, classifying product, and checking for overload safety. Usually the check weighing station is an inspection station after the manufacturing or packaging (Pack) process. Important reasons to use a check weighing system are increased accuracy, increased line speed, quality control, and to meet government regulations.
Box and Pallet Weighing: Weighing of boxes and shipping pallets is often the last step in the shipping process where finished goods are assembled and shipping charges are calculated. Industrial weighing systems prevent shipping clerks from under or over loading boxes or pallets and prevent customer shortages or damage to lifts from overweight loads, thus helping achieve plant safety goals.
Rodger Jeffery is director of business development and marketing for Hardy Process Solutions. Hardy Process Solutions provides easy process weighing equipment for a variety of OEMs in industries including food processing, chemical, plastics, rubber, industrial manufacturing, and more. For more information, contact Jeffery at [email protected] or visit hardysolutions.com.
For related articles, news, and equipment reviews, visit our Weighing System & Scales Equipment Zone
Click here for a List of Weighing Systems & Scale Manufacturers
You May Also Like