Inconsistent Inventories: Guesstimating Material Levels in Your Silos
Knowing which circumstances lead to inconsistent level measurements can help you take appropriate corrective actions
March 9, 2021
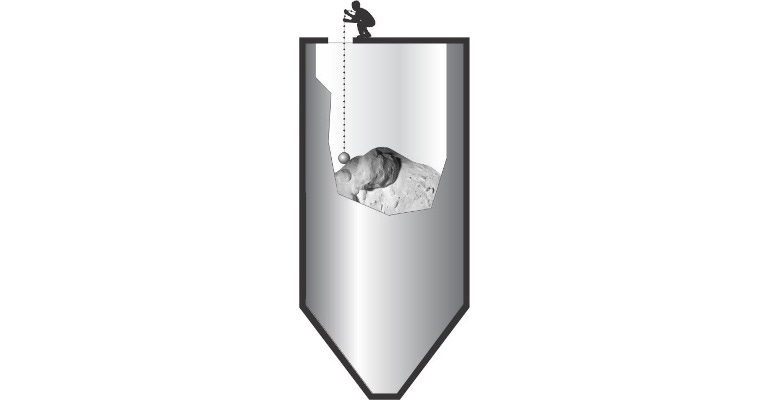
Herman Coello, level marketing manager, Siemens Industry Inc.
Is someone at your facility an expert at guesstimating the material levels in silos? I ask this question assuming that you have level instruments in place to continuously monitor material levels in your silos. But perhaps someone on your team, after experiencing inconsistent instrument performance, lost hope and now prefers to rely on old-fashioned methods of inventory management rather than on any level technology.
Does Your Production Suffer Because Inconsistent Inventory Levels Hamper Your Process Efficiency?
Production management stands to save lots of money by consistently producing goods, delivering material on time, eliminating production shutdowns, and reducing material losses. Maintaining the right inventory level of raw materials is key. Anyone seeking consistency and reliability should not only add level instrumentation to monitor their inventory levels, but also integrate digital solutions to bridge the connectivity gap and receive information 24/7. However, if erroneous inventory levels are not mitigated, your data will be good for nothing more than estimations.
This article is not about the latest breakthrough in solids level measurement. Measuring bulk solids used to be challenging for many level technologies, especially in dusty conditions common with flours, powders, cement, etc. When 26GHz radar transmitters were introduced two decades ago for solids level measurement, they were considered revolutionary. Continuous level measurement became possible during filling and emptying of silos, even under extreme dusty conditions. However, some spherically shape materials still needed special attention. Then, a decade ago, when the first 78 GHz radar transmitter was released to the market, a new level of installation flexibility and performance was achieved. Granular and spherically shaped materials (e.g. sugar, silica sand, or grains) stopped being a challenge and could be monitored easily following a simple setup of the instrument. Yet, even with the latest and greatest technology, inconsistencies in level measurement did not completely disappear. Plant managers realized that adding a new technology did not necessarily turn out to be the cure to their inventory discrepancies. Let us take a closer look why this might be.
Instead of immediately blaming your instrumentation for any inventory issue that arises, it is best to take a holistic approach to find the root cause of the problem. This requires considering the material properties, their behavior inside a vessel, and the vessel type itself. This approach may turn out to be revealing. Knowing how material behaves inside a silo can help you take corrective action where it is needed, or at least help you set the right expectations. You might also discover some serious material handling deficiencies that in the long term can prove costly.
Bulk solids and specifically bulk powder materials tend to behave somewhat mysteriously in a silo. The truth is that bulk solids materials are complex in the way they behave in and outside a storage vessel. For those who deal with facilities across the nation or the world know this. These materials can present handling challenges at some sites, while none at other sites.
Often, when inventory levels in silos are questionable, production managers turn to proven technologies for bulk solids materials to resolve discrepancies. In some cases, a certain level technology is put in place and works for some time, but then operators stop trusting the instrument’s reliability. When discrepancies are observed, an operator may verify manually that the level instrument is not reporting the correct level. After so many trips to the top of the silos, the technology in question is disregarded.
What to Do in This Case?
The general approach is to troubleshoot using one’s own knowledge or with support from the instrument provider. But what if the root cause approach is misguided? What if the inclination is to think that the level instrument is the culprit? This is often the case, and yet the problem can stem from other factors in play. When everything fails, the normal course of action is to acquire a new and possibly more powerful level instrument to replace the “underperforming” one. At first, the problem may appear to be resolved for a few days or even longer. This could be because the silo activity or production levels are not the same – but then inconsistencies reappear. What happened?
Using the right type of level technology to measure bulk solids material is important. For example, radar technology is well suited for dusty environments and long-range applications. Proper installation of any instrument is a must. This does not mean that the level device must be precisely installed with no wiggle room for those situations where ideal process connections are lacking. However, following the manufacturer’s installation guidelines is sound advice to avoid introducing failures that can be easily avoided.
When setup and installation recommendations are adhered to and nothing seems to help, the tendency is to blame the technology and assume the best option is to go back to the “good old days” of using precisely calibrated ropes. But how do you continually get that information to the control room or the cloud? One knot at a time!
Taking a Holistic Approach to Solving Your Problem
Instead of focusing attention solely on the instruments, it is also important to question the silo design, feeder mechanism, aeration system (or lack thereof), and the properties of the material itself. Understanding how material properties affect their behavior inside a vessel or silo can provide a better idea as to why some materials are easily monitored and others are quite problematic. Thus, to find the root cause it is best to approach the issue from a broad point view and then narrow it down to the most likely causes. Unless it is obvious that the level instrument is defective or you know that the wrong technology has been installed, not considering other factors can leave you wondering whether there is anything on the market that can really be trusted to provide reliable inventory levels.
What to Look for
If material flowability issues are evident when material is drawn out of a silo or transported from point A to point B, it is safe to say that material level measurements are also being affected negatively. In general, the material characteristics are analyzed for cohesive strength, compressibility, flowability, etc. Factors that affect material behavior inside a silo go beyond the material properties analysis. These include silo design, wall friction, fluidization, and variation of moisture content due to chemical composition or seasonal environmental conditions. If material is not moving or otherwise behaving as expected, production will be drastically reduced or spoiled, which can result in the loss of thousands if not millions of dollars a year. To avoid spending countless hours trying to resolve fluctuating or inconsistent level measurement, accounting for some of the factors mentioned above can help you to achieve significant inventory management improvements.
Material characteristics influence how bulk materials flow inside a silo and how they are conveyed from point A to point B. Casual observation of PVC powder, for instance, shows it to be very fluid. But after being stored in a silo for a couple days, it has the tendency to clump. This impedes easy flow out of a silo or how it transitions from hopper to bin. Clumping creates conditions that drastically change the landscape of the material in the silo. What most people don’t consider is how the material surface behaves. This is understandable since what is needed for production is what comes out the silo, and how the material looks on the surface is not immediately relevant. However, if the material bridges, ratholes, or channel flows (conditions that are not always observable since they happen below the surface), then inconsistent material levels will result. This a behavior that is common with cohesive and powdery materials.
A through-space (non-contacting) level instrument provides a measurement from what it sees – that is, from the top of the surface. The instrument requires that enough signal bounces back from the material. For instance, a flat and highly reflective surface would yield an excellent signal return, which can easily be interpreted by a radar level transmitter. But solids tend to have an angle of repose or an angular or spherical shape that is not necessarily evenly distributed across the surface. Solids radar level transmitters are designed with Process Intelligence to perform well with many types of bulk solid materials. But if the surface develops too many peaks and valleys, or the material rat holes or channel flows, the signal quality will degrade. A channel flow condition is of the greatest consequence, with large swings in material levels attributable to this type of condition. Significant level variances occur when the channel can no longer sustain its walls and the material collapses, thereby causing the level instrument to detect a new and sudden level change. The solution to this problem is not simply replacing the existing instrument with a more powerful version. This can help in the case of a material with poor reflective properties, but if the material is funnel or channel flowing, a high-powered instrument won’t save the day.
An Example
Consider a 50-ft-tall silo with a 12-ft-diameter. General guidelines suggest installing the level instrument about 1/3 the radius of the silo diameter. Now, assume that the material is drawn from the middle of the silo via the canonical section. The material in this case is a cohesive material like flour or PVC powder. When the silo is 80% full or higher, the level measurement tends to be in agreement with expectations. But hours or days later when more material is taken out, the level device no longer reports the expected level. In fact, you know that you have taken out 30% or more material to run your production and thus, the level instrument is off. If you are unaware of what is happening with your material flow pattern inside the silo, the natural tendency is to question the level technology or the instrument. Most people will troubleshoot the instrument as well, and instrumentation experts also lean this way. The approach may include re-aiming the level device for better signal reflection or even relocating it to a more suitable location in the hopes of obtaining a reliable level reading. Sometimes this helps, but usually not for long and soon you are back at it again, fighting with the instrument. Finally, you decide to replace the non-contacting technology with guided wave radar, a contacting level technology – only to learn later that you now have a new set of problems (e.g. a broken cable jammed in the feeder, a damaged roof due to pull forces, or even buildup that demands periodic maintenance) and that the original issue is not really resolved. Other times, regardless of which technology you use, material levels do seem to be on target. What is happening?
This is where taking the holistic approach comes into play. Start evaluating the situation from the very bottom to the very top of the silo. Is there evidence of poor flowability? If there are hammers or blunt objects (such as a two-by-four) near the cone area of the silo, ask why that is or why the cone looks all beat up. Maybe these state-of-the-art accessories have been there as long as you remember, and they are just part of the process. This can be compared to a child who needs eyeglasses, but doesn’t know it until he or she gets them – and then the world looks clearer. Until that moment, the abnormality was considered normal. Fortunately, somebody questioned it and clearer vision was the result. In the same vein, if someone has been beating on the silo cone to stimulate good behavior, there is clearly poor material flow. You may not have previously linked this to inconsistent level measurement, but the connection is there.
Channel flow, ratholing, or bridging unintentionally affect level measurement. Materials that behave this way need to be handled in silos designed for cohesive powders. Silos designed for mass flow are the answer for cohesive materials. The material in such silos behaves uniformly. The geometry of the silo and wall friction is such that when the material slides down, it appears to be displaced down in one piece like a piston. The material surface also tends to remain quite stable. This scenario not only alleviates poor flowability, but it also helps level measurements become more consistent. A silo designed for a mass flow pattern also includes the right feeder and interface mechanism. There are experts in this field that based on the material properties analysis, know what the right flow pattern for the material in question is and which type silo should be used.
It is not essential to have a uniform surface on top of the material for a radar level transmitter to provide consistent level measurements. The idea here is to illustrate that when material clings to the silo walls, or only flows out via the channel that was created due to poor flow, the material may start developing a ramp and material displacement will take place mainly via this ramp. As the channel becomes prominent and well formed, weakened channel walls and plant vibrations may be the catalyst for material to avalanche off the ramp. The material slides off the ramp and suddenly fills the channel, thereby creating a new target for the level transmitter and a new, unexpected level reading. Granular, spherical, or angular materials that are not cohesive, such as grains, sand, frac sand, or plastic pellets, tend to develop a steep angle of repose during the filling process. Then, when the material is taken out, an inverted cone develops. In either case, these materials are typically stored in funnel flow-type silos. A funnel flow pattern is suitable for coarse, non-degrading, free-flowing materials, and when segregation is inconsequential. The material surface is more dynamic in a funnel flow silo than in a mass flow silo. Radar transmitters designed for solids level applications are reliable when used to monitor the level in either silo type. However, material in the wrong silo can keep you awake at night.
Solids radar level transmitters can be set up quickly and provide years of reliable performance. They can be used to monitor the level of many solid bulk materials, including sugar, grains, frac sand, kiln dust, rocks, cement, flours, synthetic powders, and more. It is important to know that materials behave differently in in metal and concrete silos. Non-contacting radar transmitters are suitable for materials that display a steep angle of repose and perform well when reading material levels as material is drawn out and forms a conical shape. Most granular materials flow well and continuously roll down as they are being depleted. But cohesive powders tend to adhere to the silo wall and form a channel. This is an undesired condition. Even if no signal loss occurs during this adverse situation, the instrument may not receive a signal from an area that is representative of the actual material level in the silo.
Further Examples
Non-contacting radar transmitters have been used with success in flour silos that are 100 ft tall. In this case, the silos were designed for a mass flow pattern and regardless of the level in the silo, there was never any flour attached to the silo walls. This is an example of a first-in/first-out scenario (a desired condition for materials that can spoil or degrade). In another application, the silo did not seem to have the characteristics needed for cohesive materials. Nevertheless, the material behaved in a mass flow fashion while fluidization was active, and issues arose when the aeration was stopped, and the material had a chance to compress over time. Material was later taken out, but it no longer behaved as when air fluidization was turned on.
Conclusion
It is valuable to understand the characteristics of a material because they influence the behavior of that material while in the silo and also when coming out of it. Improper bulk solids flow patterns can potentially be the leading cause of inconsistent level measurements. When inventory inconsistencies are present, focusing on the level technology alone may not reveal the root cause of the problem. If you can determine that the material flow pattern is affecting your process and mechanical modifications of your storage system are not feasible, you will at least be aware of the culprit and can reevaluate expectations. Knowing which circumstances lead to inconsistent level measurements can help you take the appropriate corrective actions, which will certainly improve your production process. You’ll come to trust that, with the right process level technology and when used appropriately, guesstimating inventory levels will become a thing of the past – and inventory management can truly become part of your digitalization endeavors.
Herman Coello is the level marketing manager for Siemens Industry Inc. With more than 29 years experience with level instrumentation, Coello is responsible for business development and marketing of radar, guided wave radar, and ultrasonic level instruments. For more information, call 817-412-9667, email [email protected], or visit www.siemens.com.
You May Also Like