How to Avoid Wasting Material in Feeding Applications
Scrap from feeding applications can be fed back into your process or used to make a totally new product.
July 17, 2020
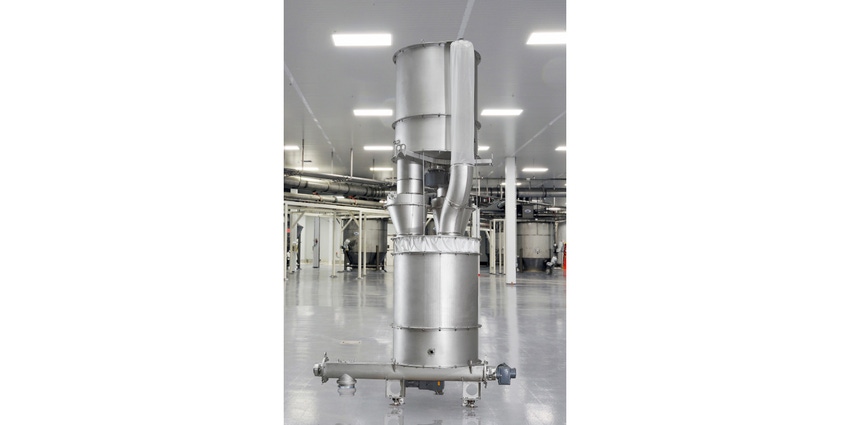
Todd D. Messmer, weighing and feeding product manager, Schenck Process
Several processes that we come across as a feeder supplier involve taking various forms of material scrap and then feeding those materials back into the process. We also come across companies that require us to feed scrapped and recycled materials back into a process that ultimately is used to make a new product. Materials such as plastic flakes from ground up water bottles or milk jugs, cellulose, hemp, stover, glass, carpet, or tiles are just a handful of the many materials we deal with.
Using film sheet extrusion as an example when extruding a sheet of plastic, the edges are often trimmed off so the sheet can be processed with a uniform width. Rather than discard this material, the scrapped edge trim can be ground up into smaller particle sizes, making it easier to store, accumulate, and ultimately feed back into the process.
Here lies the challenge for a feeder supplier. How do you feed a very light, bulk density film scrap back into a process? It requires specialized equipment designed to do so.
First, you need a feeder that can handle extremely large volumes. As an example, take a material that weighs 50 lb/cu ft. In order to hold 1,000 lb of this material you would need an extension hopper that has a working volume of over 20 cu ft. Now what if that same material only weighs 5 lb/cu ft. You would need an extension hopper that has a working volume of over 200 cu ft.
Many of these recycled materials have a very high angle of repose. The material’s angle of repose is simply measured by taking a sample of the material and piling it onto a flat surface. The angle measured between the flat surface and the pile of material is known as the material’s angle of repose. The higher the material’s angle of repose typically equates to a greater challenge for a feeder manufacturer to get the material to flow and feed. So when looking at the extension hopper of the feeder, it is going to need to be either very steep or, even better, straight walled in order to promote mass flow out of the feeder. Mass flow equals first in first out.
To get the material to flow out of the feeder some form of mechanical agitation will be required. There are two types of mechanical agitation systems when utilizing a screw feeder, either external or internal. External agitation systems typically consist of a flexible-walled hopper made out of a plasticized PVC or EPDM material which is internal to the feeder, and a mechanized system of paddles or rollers (agitators) that come in contact with the flexible walled hopper to help break up any bridging of the material to get it to flow into the feed screw. Flexible-walled feeders with paddle or roller agitation are typically not aggressive enough when feeding a low bulk density material with a high angle of repose. An internal agitation system is a much better choice. Internal agitation is in physical contact with the material so it has the ability to break up any nesting or knitting that can occur with these kinds of materials. A word of caution when internally agitating light bulk density, high angle of repose materials: a phenomenon can occur where the entire material content in the extension hopper can turn as a slug of material as the internal agitator rotates. Therefore, there needs to be some kind of a system inside the feeder extension hopper to prevent this from happening. Internally, pins can be welded onto the inside of the hopper extension or a system of adjustable stators can be directed against the turning material by rotating them or moving them into or out of the hopper extension. This will also help prevent the material from turning as a slug of material.
A feeder that is capable of feeding a very large volume of material is also required. Using the previous example of a material that weighs 50 lb/cu ft and feeding at a rate of 1,000 lb/hr a feed screw that could provide a throughput of 20 cu ft/hr would be needed. A typical 2.25-in. open flight feed screw has a water volume capacity of approximately 0.299 cu ft per revolution of the feed screw at 100% fill. Therefore, at approximately 67 rpm a volumetric rate of 20 cu ft/hr (20 cu ft/hr/0.299 cu ft per revolution = 67 revolutions per minute) would be achieved. Now taking the material that weighs 5 lb/cu ft in order to feed 1,000 lb/hr a feed screw that can deliver a throughput of 200 cu ft/hr is required. A typical 5-in. open flight feed screw has a water volume capacity of approximately 3.29 cu ft per revolution of the feed screw at 100% fill. Therefore, at approximately 61 rpm the same volumetric rate of 200 cu ft/hr would be achieved. The feed screw nearly doubled in size using this scenario. The geometry of the feed screw itself will need special consideration. As low bulk, high angle of repose materials enter the flights of the feed screw they will compress. A variable pitched feed screw with a smaller pitch in the feed throat, opening up into a larger pitch at the discharge, will allow the material to expand back to its natural shape before it is fed into the process. The pitch of the feed screw is typically related proportionally to its diameter. A 5-in. diam full pitch feed screw means that the centerline distance between each flight of the feed screw is the same distance of its diameter, which in this case is 5 in. A half-pitch feed screw would have 2.25 in. between centerlines of each flight and a double pitch feed screw would have 10 in. between flights.
Having adjustability in the throat of the feeder to allow more or less material to flow into the flights of the feed screw is also a key design feature to consider.
Also, do not overlook the refill system for these feeders. They will need the same design considerations such as vertical agitation utilized in the feeders placed below them.
In summary, do not throw away scrap, as there are ways that you can feed it back into your process or use it to make a totally new product.
Todd D. Messmer is the weighing and feeding product manager for Schenck Process (Whitewater, WI). Messmer has been with Schenck Process for the past 20 years. For more information, call 262-473-2441 or visit www.schenckprocess.com/us.
You May Also Like