ANSI/ASHRAE Standard 199-2016: An Introduction
August 5, 2016
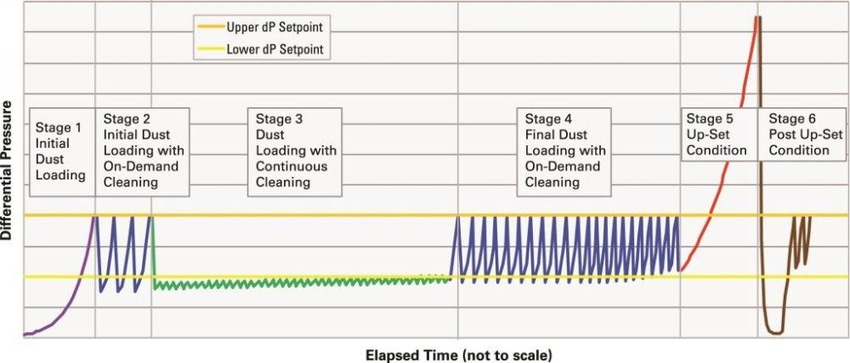
For years, dust collection equipment operators were limited to a filter element’s minimum efficiency reporting value, or MERV rating, to evaluate the possible effectiveness of air filters used in their dust collection equipment. This MERV rating, as outlined in the American Society of Heating, Refrigerating and Air-Conditioning Engineers (ASHRAE) test standard 52.2, focuses exclusively on the filtration efficiency of a filter element under very controlled testing conditions designed to mimic an HVAC system. The rating, while certainly useful, falls short on other important performance characteristics necessary to help operators make sound business decisions regarding dust collection performance. These other performance characteristics include energy consumption and emissions under conditions similar to actual operation of a dust collector.
In response to market and industry interest, ASHRAE recently published a new test standard to address these shortcomings. The new standard provides a means for dust collection equipment operators to compare relevant performance results, based on an expanded range of characteristics. This article outlines the testing methodology and provides information on how the test results relate to operational outcomes.
The ANSI/ASHRAE Standard 199-2016 test procedure includes six stages roughly grouped into three activity phases as outlined in the graphic.
Conditioning Actions
Stage 1: Initial dust loading
This stage provides accelerated ‘seasoning’ of the collector’s filters by running dust-laden air through the collector without pulsing until a high-pressure differential across the filtration media is reached.
Stage 2: Initial dust loading with on-demand cleaning
The conditioning action continues with running dust-laden air through the collector, but this stage activates the dust collector’s ‘on-demand’ pulse cleaning logic for four hours. On-demand cleaning typically operates by monitoring pressure differential across the filtration media and activating pulse cleaning when it is above a manufacturer’s recommended set point. Pulse cleaning then deactivates when the pressure differential reaches a low set point.
Stage 3: Dust loading with continuous cleaning
In the final conditioning action, dust-laden air continues through the collector, but on-demand pulse cleaning is replaced by continuous pulse cleaning for 24 hours. This fully seasons and matures the collector’s filters in preparation for the Performance Test stage.
Performance Test
Stage 4: Final dust loading with on-demand cleaning
The Performance Test stage is conducted with on-demand pulse cleaning logic as dust-laden air continues to run through the collector. The performance testing stage ends after 20 hours, or when the filters cannot recover to a specified pressure differential low set point. Test reporting data is compiled during the last four hours of the Performance Test stage.
Recovery Test
Stage 5: Up-set condition
This recovery stage simulates the dust collector’s response to an up-set condition. In this recovery stage, dust-laden air runs through the collector and all pulse cleaning controls are deactivated. The test typically ends when the pressure differential reaches 10 in. of water gauge.
Stage 6: Post-up-set condition
This final phase simulates the dust collector’s response following an up-set condition. In this stage, dust-laden air (reduced to 25 percent of full flow) runs through the collector, pulse cleaning controls are set to continuous, and the collector cycles through ten cleaning iterations. Next, the airflow is restored to 100 percent and on-demand cleaning is activated. The stage ends after one full on-demand cleaning cycle. The resultant pressure drop provides an indication of the system's ability to restore itself to pre-upset conditions.
Parameters Defined by Test Requestor
Although the testing process and stages are defined by the test standard, many testing parameters are specified by the test requestor and those choices can influence the reported performance results. These parameters include, among others, the following with associated units of measure:
• Specified airflow, acfm (cu m/hr)
• Pulse cleaning system low/high differential pressure set points, inches of water (hPa)
• Pulse interval, s (delay between pulses)
• Pulse duration, ms
• Pulse cleaning system pressure, psi (bar)
• Pulse cleaning system volume, cu ft (L)
• Up-set condition limit (if greater than ten inches of water [24.9 hPa])
Test Results Reporting
The ANSI/ASHRAE Standard 199-2016 test report contains a summary table of parameters, along with graphs of data collected throughout the testing. The summary table parameter results are generated from the last four hours of data collected during Stage 4 (Performance Test phase), which should be the most representative of real-life operating conditions. When multiple dust collector test results are compared, equipment operators can make a more informed decision when purchasing new equipment.
ANSI/ASHRAE Standard 199-2016 report summary table parameters will include:
* Emissions in mg/cu m
Emissions closely relate to what dust collection equipment operators typically need to manage. This is stated not in terms of some theoretical percent of filtration efficiency in a static test, but rather as a measure of how much material passes through the collector during normal operation.
* Differential Pressure Average in inches of water gauge
The energy required to move a given volume flow rate of air through a dust collection system with seasoned filters is a significant driver of operational costs. The lower the average differential pressure, the less energy the system consumes. Additionally, lower stabilized differential pressure values generally indicate filters which will last longer. However, since the system airflows are specified by the test requestor, consideration of the airflow per filter should be taken into account and compared to manufacturer recommendations for specific collectors.
* Air Consumption in cu ft/1000 cu ft
Energy is also required to generate the compressed air used to clean filter elements. High-performance dust collectors should deliver lower compressed air consumption values per volume of filtered airflow.
Evaluating dust collector and filter performance isn’t a simple, one-size-fits-all proposition. As with most complex systems, excellent performance for one parameter often comes with an associated cost to others. With the new ANSI/ASHRAE Standard 199-2016 available, dust collection equipment operators will now have information available in a standard format to align their equipment purchasing decisions with operational objectives.
John Woolever is a market specialist manager at Donaldson Company, Inc. He holds a B.S. in Industrial Engineering from Iowa State University and has over 10 years of experience in the air filtration industry. For more information, visit www.donaldson.com.
For related articles, news, and equipment reviews, visit our Dust Collection Equipment Zone
Click here for a List of Dust Collection Equipment Manufacturers
You May Also Like