News
Apr 25, 2024
Apr 25, 2024
Worker Dies in Cotton Processing Plant Accident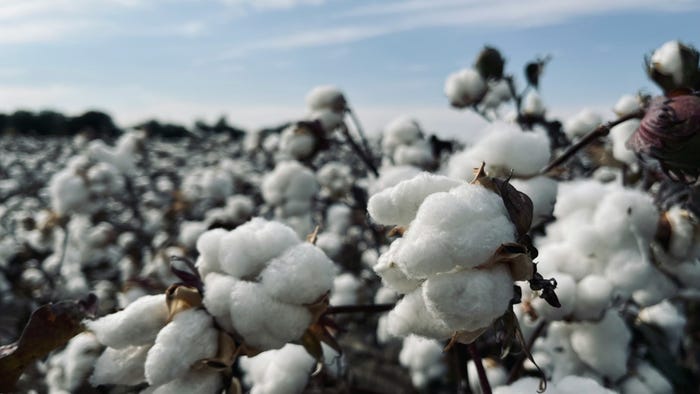
Industrial Fires & Explosions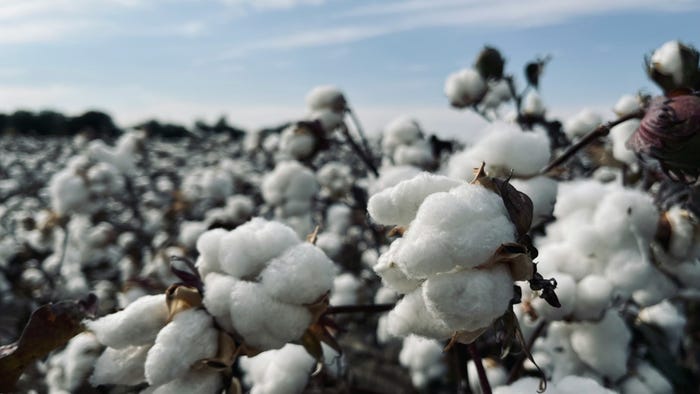
Worker Dies in Cotton Processing Plant Accident
Worker Dies at Cotton Processing Plant
He was working between two 1,500-lb stacks of cotton.
Sign up for the Powder & Bulk Solids Weekly newsletter.
Equipment
See allSponsored Content
Apr 1, 2024
Technical Articles & Case Studies
The Superiority of Abrasion-Resistant Elbows and Fittings in Industrial Applications
Abrasion-resistant elbows and fittings offer a clear advantage over their traditional counterparts.
Apr 23, 2024
|
5 Min Read
Size ReductionPrecision Grinding is Essential to Meet Specifications with Hammer Mills
Apr 23, 2024
|
6 Min Read
Material Handling & Transport4 Ways to Cut Costs with Bulk Material Container Shipments
Apr 18, 2024
|
2 Min Read
Mechanical ConveyingMaximize Conveyor Uptime with Total Preventative Maintenance
Apr 9, 2024
|
5 Min Read
Safety & Compliance
See allView upcoming and archived events from our DryPro educational webinar series, and check out webinars from our partners.
Sponsored Content
DryPro: Feeding and Filtration in Pneumatic Conveying ApplicationsPowder & Bulk Solids South
PBS South: A Closer Look at 3 Sessions
Combustible Dust Safety, Life After the Dust Hazard Assessment, & Advancements in Logistics of Bulk Solid Recyclables
Recent
Industry Insights
Scott Miller
Consultant, Solids Handling Technologies Inc.
Casey Bickhardt
president, CEO, owner
Scott Miller
Consultant, Solids Handling Technologies Inc.
Discover top-quality suppliers in the Industry Master directory
Featured Suppliers
See our featured suppliers
Manufacturers
Search manufacturers A–Z
Representatives
Search representatives A–Z
PBS South is where technology and innovation meet to set the course for the future of bulk processing. Join us in Charlotte, NC on June 4-6 to connect with product experts who can help you sharpen your competitive edge. PBS South is part of IME South, a six-in-one expo offering the latest insights & solutions spanning medtech, packaging, automation, plastics, design, & processing.
Register Now