Precision Grinding is Essential to Meet Specifications with Hammer Mills
Examining the benefits of efficiently maintaining hammer mills with precision grinders.
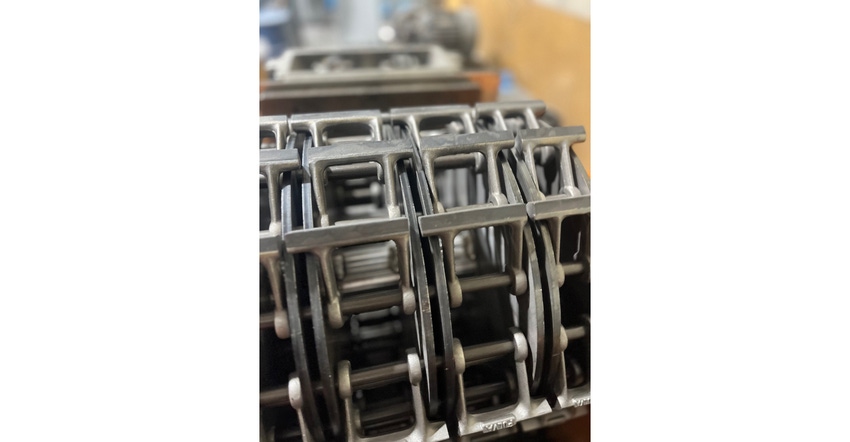
Professionals dealing with bulk solids often rely on industrial pulverizing hammer mills. The mills are designed to crush a comprehensive variety of solid materials ranging from soft to hard, for size reduction needs from 6 mm to 35 microns, for optimal particle size distribution in a variety of milling applications.
Because pulverizers--commonly known as hammer mills--are so varied in their material crushing capabilities, the equipment is widely used across many industries for various particle size reduction needs.
To efficiently pulverize industrial materials, the many internal hammers in industrial pulverizers are forged, hardened, and then ground down to create the optimal impact edge, minimize vibration, and fit within tight clearances.
To examine the benefits of efficiently maintaining hammer mills with precision grinders, we discussed the topic with Mike Anderson, a technical specialist at DCM Tech, a Winona, MN-based designer and builder of industrial rotary surface grinders.
Q: What do Powder & Bulk Solids readers need to know about hammer mills?
A: Hammer mills are essential pieces of industrial equipment used to crush or pulverize a wide range of materials such as spices, cosmetics, pharmaceutical powders, rocks, minerals, and recycling waste. Although the design can vary, hammer mills are a steel drum containing a vertical or horizontal rotating shaft or drum on which hammers are mounted. Within the chamber, the hammers swing freely on a rotor that spins at high speeds while material is fed into the hammer mill from a feed hopper. The material is impacted by the hammers and is thereby pulverized and expelled through a screen in the bottom of the mill.
Because the many internal hammers spin at extremely high velocity to pulverize materials, the point of contact of each hammer must be precisely ground to the correct shape and weight with virtually no variation; any excess can not only cause severe abrasion but also throw the carefully calibrated machine dangerously out of balance.
The tip of the hammer travels approximately 21,000 ft/min. That velocity leaves little room for imprecision in the hammers, which must be precisely ground to certain specifications of size, thickness, and weight. There can be dozens or up to a hundred or more hammers in the largest pulverizers.
To minimize vibration, each of the rotors that the hammers are assembled to are dynamically balanced to tight tolerance. The hammers must also be manufactured to an extremely consistent weight and size. This is critical not only to maintain the balance of all the rapidly swinging hammers but also to provide sufficient clearance within the tight confines of the chamber.
Q: What role does precision grinding play in efficiently maintaining hammer mills?
A: Precision grinding is extremely important in maintaining the impact edge of hammer mills. Since the hammers are high wear parts, the tips are hardened to withstand continual impact. However, this requires grinding the “impact” edge to the ideal dimensions for optimal pulverization of the material.
For hammer mills to reliably function requires extraordinary coordination of all the hammers swinging at extremely high velocity within narrow confines. With great precision similar to a Swiss watch but on an industrial scale, the end result is exceptionally precise pulverization machinery designed to last for many years.
Q: Can you give an example of how precision grinding was successfully used to maintain industrial hammer mills? Please explain the importance of the grinding and how it was effectively accomplished.
A: Yes, a Saxonburg, PA-based OEM provides a wide variety of pulverizers and auxiliary equipment. This includes hammer mills of different sizes and capabilities. The OEM offers various hammer mills from a small lab size with only a few hammers, to its largest, which uses more than 100 hammers. They produce tens of thousands of hammers a year, all of which must be extremely precise.
The specialized hammers are manufactured by beginning with either forged carbon steel or stainless steel. However, forged parts can have variances in dimensions, surface finish, and material properties. These variations are inherent to the forging process and can result in slight differences between each manufactured piece.
There is some weight variation in the forged hammers since there are differences in the material used, the heat, and the forging process itself.
To increase the durability and longevity of the high wear part, the hammer mill OEM welds a layer of hardened material on the tip, or impact edge. The thickness of the hardened material welded onto each hammer varies depending on several factors but can generally range from 0.25 to 0.5 in.
Without a hardened surface, the impact would wear the base material, which is not hard enough to withstand what the hammers are put through. So, the hammer mill OEM welds on an overlay of hardened material at the tip where the impact occurs. However, there is variability in the overlay as well.
To ensure absolute consistency of size and weight of the hammers installed on new equipment, the OEM has relied on advanced rotary surface grinders.
The rotary surface grinders surface the tip of the OEM’s hammers down to a specific size, shape, and dimension, which provides a good impact edge. The surface grinders take the hardened welded material down to exactly what is needed for the hammers.
The OEM ensures that each hammer possesses uniform weight while adhering to essential internal clearances by grinding the hammers’ base edges.
There is a very specific dimension from the tip of that hammer to the inside of the OEM’s hammer mill. Adequate clearance is required to avoid impact damage to the mill itself, but it also needs to be close enough to provide the fine pulverization needed.
The OEM has owned several rotary surface grinders for more than 20 years that work really well and hold close tolerances.
Q: When it’s time to replace a rotary surface grinder, what kinds of upgrades are available today, and what are the benefits?
A: After 20 years of use, the hammer mill OEM decided it was time to replace one of them and recently purchased its third rotary surface grinder, a more automated, robot ready model with a 24-in. variable speed table and 20-hp variable speed grinding spindle motor.
The surface grinders are designed with advanced sensors and controls that automatically maintain tight tolerances, removing material down to within one ten-thousandth of an inch of the final thickness. Digital technology also allows for an interface with easy-to-use touchscreen controls.
The new model also includes advanced features that automate the initial contact between the abrasive wheel and the part, which typically had to be finessed by the operator. With this updated option, advanced sensor technology detects vibration and can automatically fine-tune not only the pressure of the spindle motor but how quickly it moves the wheel down onto the part. When the machine senses the abrasive wheel has contacted the part, it automatically begins the grind cycle.
Automatic part detection eliminates the need for the operator to do time consuming, error prone “manual touch offs” where they would manually feed the grinding machine until it just touches the surface of the part before backing off and restarting it.
The rotary surface grinding process consistently achieves high throughput and eliminates variability, which enables the OEM to achieve high-quality finished hammers with great consistency.
The advanced rotary surface grinder arrived “robot ready,” allowing the OEM to incorporate robotic elements when needed in the future.
By adding robotics for the loading and unloading of workpieces, OEMs with higher production demands can substantially decrease cycle times while improving precision on unattended machines.
For more information, contact DCM Tech at 800-533-5339 or [email protected], or visit www.dcm-tech.com.
About the Author(s)
You May Also Like