4 Ways to Cut Costs with Bulk Material Container Shipments
Here are 4 ways you can cut costs in your day-to-day bulk material supply chain operations.
April 18, 2024
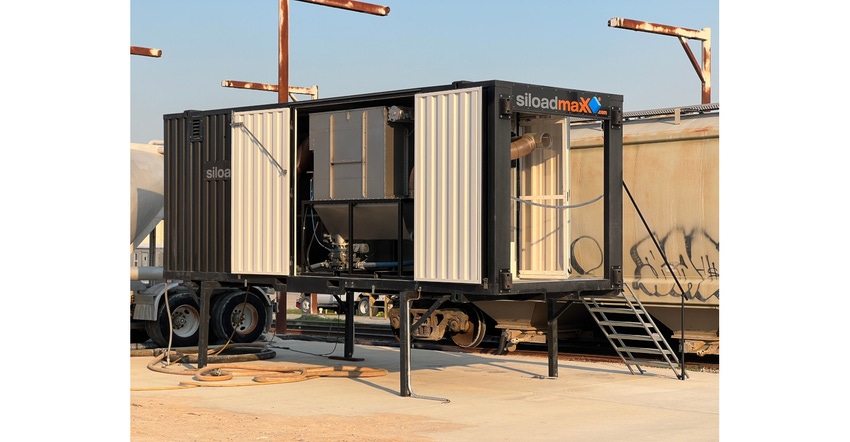
CapEx investments are difficult to justify in current market conditions for chemical companies and other raw material manufacturers or importers. You might have a great idea that will improve the processes in your company, but you already know that your boss will not grant you the funds necessary. What would your boss say if you presented him/her with a solution to save costs in already existing supply chain processes instead of generating new investment expenses?
Here are four ideas for how you can cut costs in your day-to-day bulk material supply chain operations.
1. Making the Most of a Container’s Payload
Optimize the space occupied by material inside a shipping container. Usually containers loaded with FIBCs (or big bags) are only 90% full at most.
Bulk materials with a light density (below 0.7) will not reach the weight limit per container when loaded with FIBCs.
Modern loading methods with a liner bag let you use 100% of the available space inside a shipping container.
Getting more material into each container means that you need to ship less containers in the end, saving you handling and shipping costs.
2. Reduce Costs for Material Packaging
One 20-ft container is loaded with 20-28 FIBCs depending on the bulk material and FIBC measurements. Each FIBC weighs 1.5 kg on average, leading to 36 kg of packaging material for 24 FIBCs in one container.
One liner bag for a 20-ft container weighs about 16 kg, saving more than 50% packaging material.
Savings can be generated when only one liner bag is needed per container instead of 24 big bags.
3. Reduce Necessary Handling Per Container
Not only will you be able to save money on the packaging itself, but handling all this packaging and the packaged material will become less costly as well.
Instead of 24 movements with a forklift for each loading and unloading, the liner bag can be installed and dismounted by one person in a matter of minutes.
Also keep in mind the handling required for each FIBC inside the production facilities.
4. Automate Your Container Loading and Unloading Processes with Rental Equipment
The fourth idea is connected to the former one. Automating your processes for container loading and discharging can allow you to reduce the required manpower and handling steps per container.
Bulk material loadings and discharges are continuous processes that should not require constant handling steps or even observation by your workforce.
Many companies offer their equipment on a rental basis that allows you to automate existing processes without an initial large CapEx investment.
Lars Hanses is CEO of WWTec GmbH & Co. KG. For more information, call +49 (0) 2624 94 370 44 or visit www.wwtec-solutions.de.
About the Author(s)
You May Also Like