The Latest in Coatings for Tanks and Silos
September 14, 2006
If you’re considering the purchase of a new tank or silo for your process dry bulk material, the type of coating found on the inside of your tank will be one of the most important factors you consider. Whether dry foods, plastics, chemicals, wood products or minerals, each material has its own requirements.
Coatings are essential for tanks. They provide corrosion and abrasion resistance, which extends the life of the tank, and promote material flow.
Coatings are essential. They provide corrosion and abrasion resistance, protecting the inside of your tank from the materials that pass through and extend the life of your tank. The slickness of the coatings promotes flow to ensure all product passes out of the tank/silo, leaving minimal residue. Finally, the protection offered by coatings often means less maintenance during the life of the tank.Construction materials used for tanks and silos in the dry bulk industry today are basically defined: carbon steel, stainless steel, aluminum and—for exceptionally large volume—concrete. What most differentiates brands and manufacturers (and the quality and total life-cycle of the tank you buy) is the coating.
Today’s coatings are commonly applied as a powder or liquid epoxy. The cutting edge in technology for dry bulk storage coatings is Trico-Bond EP. Once applied and cured, this epoxy will bend without breaking or tearing. Trico-Bond EP is a highly engineered thermosetting modified epoxy powder that underwent more than five years of testing before introduction to the market. In testing, it performed better than 2B-finish stainless steel. It also has met FDA requirements for food contact and is utilized both as an interior liner and exterior primer. On the exterior, it is combined with urethane topcoats to provide the greatest protection against the elements.
Testing Abrasion Resistance
Abrasion resistance is commonly tested by the “falling sand” test. This test measures the stream of falling sand required to wear through a coating. At a normal 3 mils dry film thickness, many older coatings require 20 to 200 liters of sand before wearing through. In contrast, today’s high-quality coatings may require up to 600+ liters of sand before wear-through.
Comparing Flow Promotion
If you’re considering a new tank, you should first determine your product’s abrasiveness and bulk density, and importantly, consider its flow requirement. Is your product free flowing or non-free flowing? If you are not familiar with your product’s flow requirement, you should have it flow tested before buying a tank. Flow testing will determine the proper degree for the hopper and hopper outlet and will provide requirements for flow or blending equipment needed to ensure proper flow. The slickness of the tank coating you choose also will be a key element in maximizing your flow system.
Application: The Key Difference
While most coatings applied today consist of either powder or liquid epoxy, the difference lies in their application. High-quality coatings are applied at the factory under environmentally controlled circumstances, ensuring the most consistent application. Taken one step further, the best coatings are then thermally cured at the factory. Some manufacturers may apply the coatings at the factory but then allow them to air-dry and cure with ambient heat, which exposes the cure to environmental factors such as dust and humidity. Other manufacturers manufacture the tank or silo but outsource the coating process. The optimal coating solution is one that is both applied and thermally cured in controlled factory conditions before the tank is shipped and erected in the field. Typically this can be accomplished with factory welded and bolted tanks.
Tanks that must receive their coatings onsite in the field once the tank has been erected include field welded and concrete types. These tanks may need to undergo a chemical process to protect the coating while the tank is being erected (i.e., heat from welding may damage the coating). If you are reviewing this type of tank, make sure there are adequate quality control measures listed in the specification and consider third-party inspections. Be aware that once a tank has been erected in the field, there are often areas of the tank that are extremely difficult to sand blast and/or fully prepare for field coating. Even “missing the smallest spots” leaves exposed areas open to corrosion or residue. Also, the thickness of coatings applied in the field cannot be controlled, which may result in uneven application. Finally, keep in mind that the curing process in the field will be affected by weather and the environment—dust, humidity and wind.
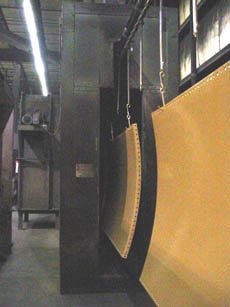
After the abrasion-resistant coating is applied to bolted tank sections, the pieces are thermally cured at 350° at a Columbian TecTank facility.
Comparing Apples with ApplesIf a tank manufacturer promises a low cost for tank and coating, make sure you are comparing apples with apples. The quality of the coating will significantly affect the maintenance cost and recoating requirements and therefore the whole life cost of the tank or silo. Compare the specifications of each tank being offered, especially the coating application sections, and ensure that the costs you review are comparable.
Why is a High-Quality Coating so Important?
Tanks without high-quality features may quote lower on initial cost. But in the long run, their total life-cycle cost is often comparable to or higher than a high-quality tank with a good coating. A quality abrasion resistant coating ensures against corrosion, a common problem that shortens the life of the tank. A good-quality coating often means lower maintenance, offering fewer headaches during the tank’s life cycle. A quality coating also means less residue on the inside of the tank.
Other Considerations
Are coatings for tanks absolutely necessary? “Black tanks,” or tanks without coatings, are sold for storage of products that are protectants in themselves. For example, tanks for storage of soybean oil or an abrasive product like sand would not need a coating.
Would you ever consider moving your tank or silo? Coatings applied in the field reduce the ability to move the tank, as the coating will tear or break when the pieces are moved. Also, if your tank requires a special coating, some coatings are available today that resist high heat, are suited for cold weather or withstand acidity.
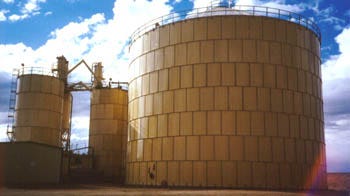
The highest-quality coatings promote abrasion and corrosion resistance for nearly all materials, including dry foods, plastics, chemicals, wood products, minerals, etc.
Locating an Experienced VendorIt may seem like common knowledge to mention experience as a factor for choosing a tank and coating, but it is key consideration. Consider the experience of the tank manufacturer: how long the company has been fabricating tanks; whether it uses state-of-the-art coatings; whether its coatings are factory applied and thermally cured; what its quality control measures are; what its volume sold is; in what countries it sells; which markets it supplies. Also consider tank manufacturers with third-party accreditation, such as the ISO 9001 Quality Certification.
Peter Vodak is corporate coating engineer with CST Industries Inc. He is a NACE certified coating inspector. Columbian TecTank, a division of CST, specializes in the design, fabrication, factory coating/thermal curing and erection of tanks and silos for the dry bulk industry. For more information about choosing tanks and coatings, visit www.tanks.com.
About the Author(s)
You May Also Like