The Cost and Risks of People Entering Bridged Silos
The safe and only true option is to never put a person in a silo that can lead to engulfment.
September 21, 2023
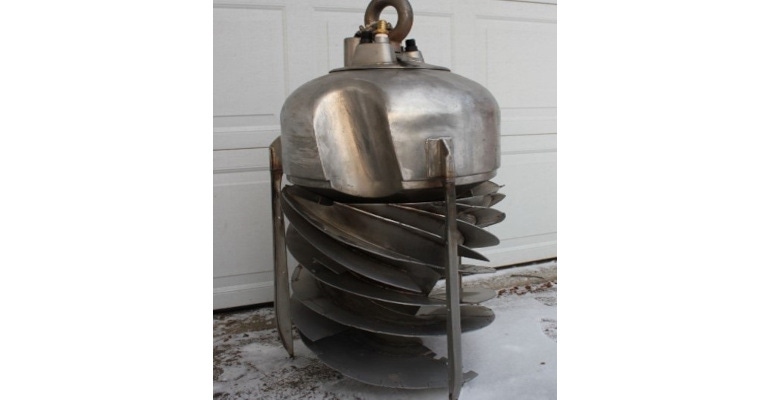
Michael L Anderson, PE, owner, Anderson Engineering
CBS Sunday Morning Postcards from Nebraska by Roger Welsch described America’s Silos as our castles. They provide security, food, medicines, so many things. They store so much of what we need.
For those of you with silos, how much of your company’s wealth is stored there? What is the value of the silo itself? It is an asset not a monument. Is the material it stores a key part of a process, maybe sugar for a drink? Have you lost your castle?
Ship cargo holds, railcars, and semi-trailers are also sites for bridging. The material cannot be transferred. Again, the solution should not be putting someone in the vessel. A device should be used to break up the bridge. This can create another problem. Using outside vibrators can damage the train car or truck trailer.
A material like dried distillers grain (DDG) doesn’t store well. It is so hydrophilic that even a little bit of moisture can create a significant bridge. Corn and similar products are fine as long as they are processed and shipped quickly. While quick shipping can prevent bridging, there is an exception to the rule.
We ran into a bean problem where a silo was filled with overly wet product. The result was a partially filled silo with an ammonia environment and no safe way to clear it. They used one of the big cleaning services and got less than 10 bushels of black beans. We got about 100 bushels ground up and the confirmation that we needed more torque from our device.
Some definitions are in order. A bridge is a packed portion of the product that prevents the flow of material above and the easy removal of product below. Bridges on the top are easy to break up. Too often the bridge is far below the top of the product. To get to the bridge, a significant amount of loose product is protecting the bridge from above. Either the bridge is not accessible from the bottom or not safely accessible. The material stored is now of less or no value.
Ratholes are a narrowing of the flowable material to a very thin channel. This is a little easier to free up but again there is a time delay and the loss of quality of the product. Castling is a structure in a silo that does not necessarily block flow but does make less space to be available and may cause secondary product issues as the structure of material in the silo will not leave the silo until it is broken up. Again, has the product been degraded?
You have lost the ability to use your product on the timely basis you planned. The quality of the product is diminished and may have to be discarded. What is your cost for this lost material? Have you lost the opportunity to make product? Has this created another significant cost? One customer lost $45,000 per silo bridge in sugar that was contaminated by the clearing efforts.
This same customer had to pay more than $30,000 per week for a crew to come in and attempt to clear the bridge. They eventually put one of the contractors with a long piece of conduit under the silo’s cone in a confined space of one small door and the closed ring of support. They would remove the rotary valve and have this person poke at the bottom until the bridge broke free. Being in the little room with a hopefully locked out auger when the sugar started to flow is not for the faint of heart.
Those are the operational costs. The big cost is when someone enters the silo. The air may be bad. The bridge collapses. Safety lines can part. A worker is seriously injured or more often killed. The Great Plains Center for Agricultural Health states, “An adult can be completely buried (engulfed) in 20 seconds.”
I was the person to be rescued at a demonstration put on by Dr. Carol Jones of Oklahoma State University. Rather than trying to pull the victim out, they build a small caisson around him and use a small auger to remove the material in this smaller container where the victim is located. Once the material is out of the caisson, they pull the victim out with a pulley, or he climbs a ladder. All fine and good, but engulfment occurs quickly.
There is one particularly dangerous scenario. This is called “walking down the grain” in farm and ag operations. Voids are created as the silo is filled. While the silo looks full, it is significantly under capacity. Somebody walks over the top of the material hoping to collapse the material and eliminate the voids. Then they need to get out.
Without rescue, death occurs quickly to the person in the silo. The Peoria OSHA fined one grain operation for serious violations without a fatality. Reviewing the fines for killing an employee can exceed $600,000. Those are the costs if you don’t care. The penalty if you do care is a lifetime of guilt.
Usually, the way to get the body out is to make a hole in the silo side wall and clear out the material. A big hole is needed. That is not cheap and may require significant repair costs.
Don’t fool yourself: a written policy proclaiming immediate termination does not keep the hero out of a silo. I have spoken to a number of managers who vigorously defend their policy regarding the prevention of someone entering a silo. This is after one or sometimes two of their employees have died in an engulfment. Their indignation rings hollow.
The safe and only true option is to never put a person in a silo that can lead to engulfment. No complex rope system, no bosuns chair. Find a safe alternative.
Small-diameter augers can drill lots of holes and hoping for the Swiss cheese affect, the bridges structural integrity is eliminated and the bridge collapses. Little devices crawl across the crusty top of a silo. Some people shoot guns, and the CO2 “grenades” may break up a surface crust. Different pressure hoses may sometimes work.
Regardless of what is being used, we are still seeing injuries and deaths due to workers entering silos. There are devices that are safe and can prevent disasters.
Michael L Anderson, PE, is owner, Anderson Engineering (Newark, OH). For more information, call 740-403-9576 or visit andeng.co.
You May Also Like