What is the Maximum Capacity of My Vibratory Round Separator?
But there are a few considerations that can be made when determining capacity.
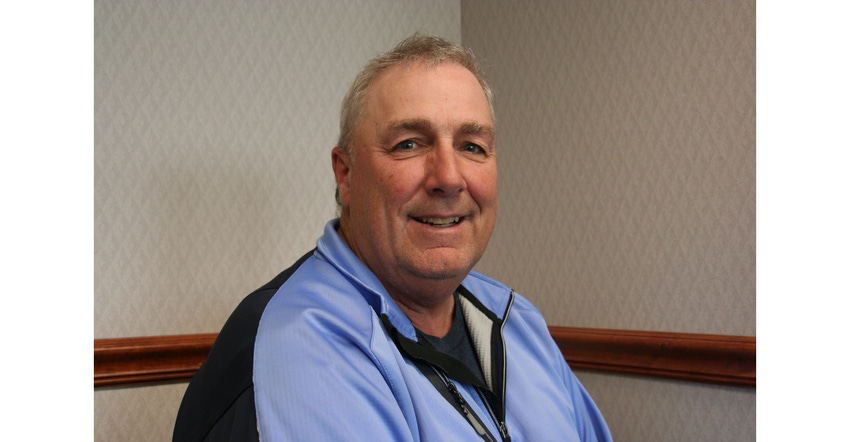
Rob Yake, regional sales manager, SWECO
As a manufacturer of screening equipment, one of the more common questions asked is “What is the maximum capacity of my round separator?” Unfortunately, there is no simple answer to that question. Considering all variables, everyone’s maximum capacity will be different.
Without doing testing, the question really can’t be answered with any accuracy. But there are a few considerations that can be made when determining capacity. The first thing to consider is the separator itself. The configuration of the separator will be a major determining factor of capacity.
For example, consider a 48-in. round separator with the optimum weight settings screening a free-flowing material. The separator with an 8-in.-diam discharge spout can convey and discharge approximately 2 cu ft/min of oversize material off the top screen. The standard table frame on that separator can convey and discharge approximately 4 cu ft/min of undersize material. If you exchange the standard table frame for a scalping frame, the separator can now convey and discharge approximately 9 cu ft/min of undersize material.
All capacities mentioned are the maximum that the separator can handle because of the standard spout size. Even if a high amount of material can be conveyed across the screen quickly, it means nothing if the discharge spout isn’t large enough to handle the capacity. But, of course, capacities can be increased by expanding the spout size to accommodate a larger amount of discharging material.
Another option to consider is changing to a flow-thru design, which allows for material to exit the separator quicker than the traditional separator. However, flow-thru designs typically are not good for sizing applications where high efficiencies are required.
The characteristics of the material being screened are a major determinant of a separator’s capacity.
Let’s consider sugar as an example. There are many types of sugars--granulated, confectioners (powdered), cane, turbinado--to name a few. Each has unique characteristics that will affect how much can be processed in a separator in a given timeframe.
Comparing granulated sugar with powdered sugar, they are the same material with a different particle size. The larger granulated sugar is a free-flowing material and is typically a simple screening process. Powdered sugar screening is more difficult because the material tends to blind the mesh openings and screen at a slower rate due to the higher surface energies of the smaller particles.
Material size is not the only characteristic that can affect capacity. There are many other characteristics (i.e., static attraction, moisture content, bulk density) that need to be considered. For instance, the environment can affect the characteristics of your material. Things like humidity or static can play havoc on many processes. Screening in Florida may be more difficult or easier than screening in Arizona, depending on whether the humidity or static causes problems.
Just be aware that your material characteristics will greatly affect the capacity of any separation process.
The material’s particle size distribution will play a role in the capacity as well. For example, if the granulated sugar has 95% of the particles slightly smaller than a 20-mesh screen, then only one sugar particle can go through a screen opening at a time. This will cause a "traffic jam" at each screen opening. The sugar will spread out on the screen "hunting" for an open mesh hole, greatly slowing capacity. Thus, a very large screen area will be needed to get a higher capacity rate.
These are just a few of the more common factors that can affect the capacity of a vibratory round separator. But when the question “What is the maximum capacity of my round separator?” is asked, the only way to answer the question truthfully and accurately is to recommend extensive testing of the material through the original equipment manufacturer.
Rob Yake is regional sales manager at SWECO. He has more than 35 years of experience with bulk solids processing equipment.
About the Author(s)
You May Also Like