How Rice Mill Reduced Downtime with “Intelligent” Magnets
Kennedy Rice Mill was able to reduce production shutdown times for magnet cleanings by one-third.
August 28, 2023
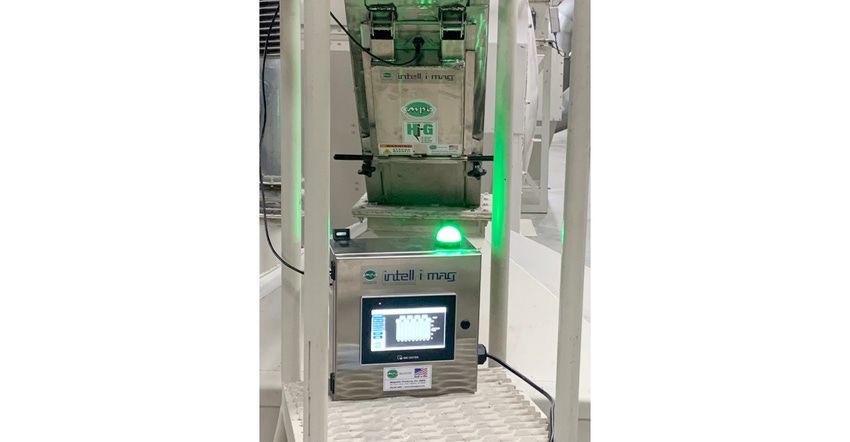
Most food processing plants have magnetic separators that remove ferrous debris from raw materials at various locations throughout the production process. Without a reliable method for knowing when these magnets are saturated with metal, plants must temporarily shut down their production lines at set intervals for regular magnet cleanings, whether needed or not. This inefficient practice has led to a gap in lost production time and unnecessary, increased plant operational costs.
Intelligent magnets bridge that gap. Internal sensors within a magnetic separator digitally monitor metal saturation levels and alert plant personnel via a mobile phone app, or local controller, when a magnet has reached its designated saturation level established by a customer. This notification enables plant personnel to initiate cleaning or activate an automated, self-cleaning system. It is a more informed and efficient way of knowing when to pause production so that magnets can be cleaned and maintained thus keeping them operating at peak performance. Ultimately, this reduces overall production downtime and can save a substantial amount of time and money.
Kennedy Rice Mill and Intell-I-Mag
Kennedy Rice Mill, a second-generation farm family-run mill based in Louisiana, is an industry leader in adopting cutting-edge technology to fit specific product application needs. As one of the original Intell-I-Mag customers of Magnetic Products Inc. (MPI), Kennedy Rice Mill saved more than $1.5 million in one year after installing the system, as referenced in the chart below.
| Before Intell-I-Mag | After Intell-I-Mag |
Lost revenue per day due to shutdown | $6,500 | $6,500 |
Frequency of shutdowns for cleaning | 1x/day | Every 3 days |
Shutdown days per year for cleaning | 365 | 122 |
Lost revenue per year due to shutdown | $2,372,500 | $790,833 |
Kennedy Rice Mill was able to reduce production shutdown times for magnet cleanings by one-third; from once a day to every three days. Magnet cleanings remain thorough yet are more efficient with greater guidance on timing and saturation levels via Intell-I-Mag.
Other benefits for Kennedy Rice Mill have included:
Improved data quality for internal quality assurance programs, auditors, and customers
Elimination of paper cleaning records through automatic data logging
Greater vendor accountability because improved metal contaminant tracking at the direct point of receiving holds suppliers more responsible for material quality
Earlier metal detection, which in turn protects process equipment throughout the entire production line
Optimized labor productivity because employees can perform other duties besides checking magnets
Validation that plant operators have cleaned the magnet through a data validation of Intell-I-Mag sensors
Based upon data collected by Intell-I-Mag, the company predicts it will be able to increase production by 20,000 pounds per day. This is a result of time gained from reducing the frequency of shutdowns for magnet cleanings as well as more insight into ferrous metal collection trend data.
Benefiting from New Technologies
As demonstrated with Kennedy Rice Mill, Intell-I-Mag offers benefits over traditional magnet separation equipment. It gives plant operators real-time insight into metal collection on magnets. This robust system conveniently tells operators and personnel exactly when a magnet needs to be cleaned and, perhaps even more importantly, when they do not need to be cleaned. This knowledge is vital for establishing optimal timelines for necessary magnet cleanings. The system also provides automated quality control data collection for internal QA programs, auditors, and customers, while also keeping food processing on the cutting edge.
Intell-I-Mag is an Industry 4.0 tool offered exclusively on MPI’s magnetic separation equipment to maintain peak magnetic performance. It is the is the industry’s first “intelligent” magnetic separator.
For more information, call 248-887-5600, email [email protected], or visit mpimagnet.com.
About the Author(s)
You May Also Like