Turbo Blower Integration into Pneumatic Conveying: An Approach to Energy Savings
August 9, 2012
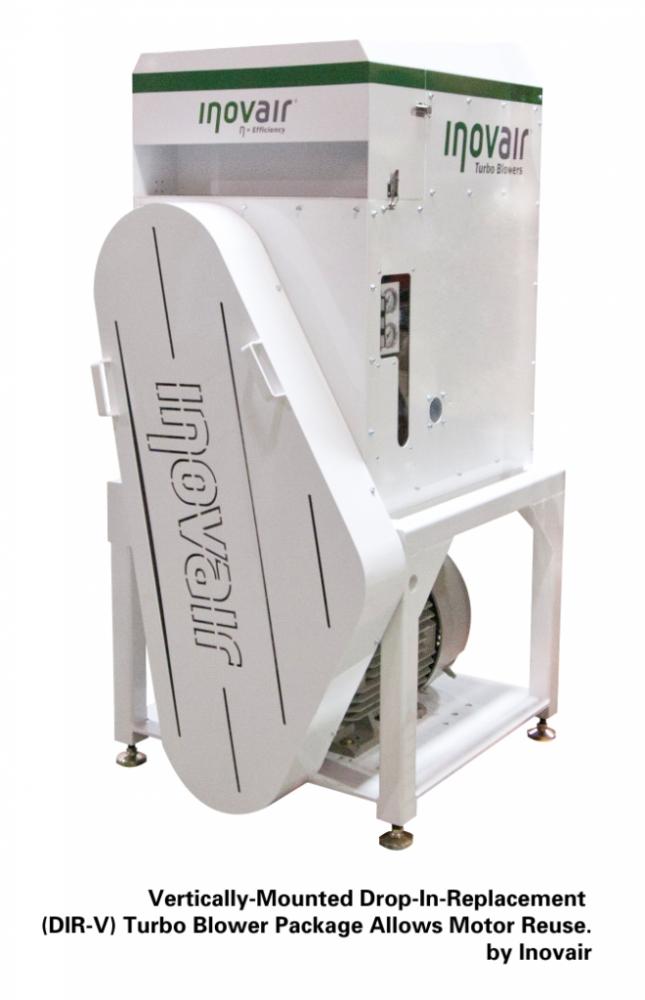
Recent introduction of turbo blowers into the pneumatic conveying industry has now given processors options other than traditional rotary positive displacement blowers to consider. This article’s intent is to provide an understanding of centrifugal blower technology, by discussing history, operating principals, application advantages, and selection of the right blower to maximize your energy savings.
Turbo Blower History
Turbo blowers, also known as centrifugal blowers, are part of the turbomachinery family of compressors. Turbomachinery was first implemented as a gas turbine in the late 1700s, with the first patent issued in 17911. By the late 1800s, the idea of using turbomachinery in many practical applications had taken hold. French Professor Auguste Rateau invented the first centrifugal compressor in the late 19th century, and had his first industrial unit operating in a steel works in 1903.(2) Turbo blowers evolved with their use in aircraft applications during the time of World War ll. From the 1950s to 1990s, turbo blowers became widely used in more demanding 24/7 operations such as wastewater aeration, coal gasification, gas recovery, natural gas pipeline compressors, and other industrial applications. Recent technological advancements in turbo blower packages have leveraged this technology for other applications, including pneumatic conveying.
Operating Principals
Turbo blowers are comprised of three key components: an impeller, diffuser, and collector (Figure 1). The impeller rotation draws in air that is then directed into the volute. As the air travels through the impeller, it gains a high amount of kinetic (or moving) energy. This energy is converted into static pressure as the flow is transferred through the diffuser into the collector. The product of impeller RPM and diameter determines the maximum amount of achievable pressure. This aerodynamic compression process typically achieves efficiencies of 75% - 85% (Figure 2), regardless of the pressure rise.
Due to the rigorous operating requirements of pneumatic conveying, rugged integrally geared single-stage turbo blowers are successful in this application. The integrated gear box allows the turbo blower to operate at an optimum speed driven by a standard 1800- or 3600-RPM drive motor. This feature allows re-use of existing motors and ancillary equipment reducing capital investment costs. Intelligent airflow controls and PLC-based communication provide for seamless integration.
Application Advantages
The advantages that processors are seeing with integrally geared turbo blower technology typically include: reduced energy costs, decreased noise levels, no pressure or flow pulsations, higher pressure capabilities, and the proven reliability associated with turbo machinery for decades. Other benefits of centrifugal blower technology are lower discharge temperatures (lower dT), preserving product integrity, and the ability to withstand high intake air temperatures.
Plant expansions can add new destinations, extend convey distances, and increase system capacity requirements. A recent example where turbo blower efficiency and pressure gains were utilized to increase the convey capacity of a previously existing PD blower system saw a 21% increase from 56,000 to 68,000 lb/hr successfully accomplished. This was accomplished without changing the motor size, electrical power to the motor, line size, or the filter receiver capacity. In these cases, significant saving extend to hardware costs, installation labor, and reduced downtime, in addition to the ongoing electrical savings afforded by the high efficiency turbo blower.
Selecting a Turbo Blower
When selecting any process improvements there are many items to consider, and this holds true when considering a turbo blower for improving your pneumatic system performance. A comprehensive evaluation of your current system performance including airflow, normal operating pressure, maximum operating pressures, ambient conditions, and duty cycle are all important in selecting the most efficient turbo blower for your specific needs. Other items to consider are possible capacity increase demands, noise reduction desires, and lower convey air temperature requirements. Additionally, an overall life cycle cost assessment is a recommended approach over consideration of initial capital expense only. If any of these factors are part of your process improvement strategies, then a turbo blower should be included in your analysis.
D.G. Kuiper, M.S.M.E Eng. Director, and M. A. Carlson, P.E., M.S.M.E., can be reached at Inovair (Lenexa, KS) at 913-469-7244 or www.inovairblowers.com.
1 Cook, Alan F. (July 2003). "John Barber – The Inventor of the Gas Turbine: A Potted History". Nuneaton & North Warwickshire Family History Society–Journal: 10. June 19, 2012
2 Klaus H. Ludtke, Process centrifugal processors: basics, function, operation, design, application (Berlin [etc.]: Springer, 2004).
CAPTIONS
Figure 1: Basic components of a turbo blower
Figure 2: Centrifugal blower operating map example with efficiency islands
Figure 3: Efficiency comparison of various blower technologies
Dir-V: Inovair DIR-V blower package
You May Also Like