Q&A: Debottlenecking Existing Pneumatic Conveying Systems
This Q&A stems from the 2023 DryPro Webinar with the same title.
March 5, 2024
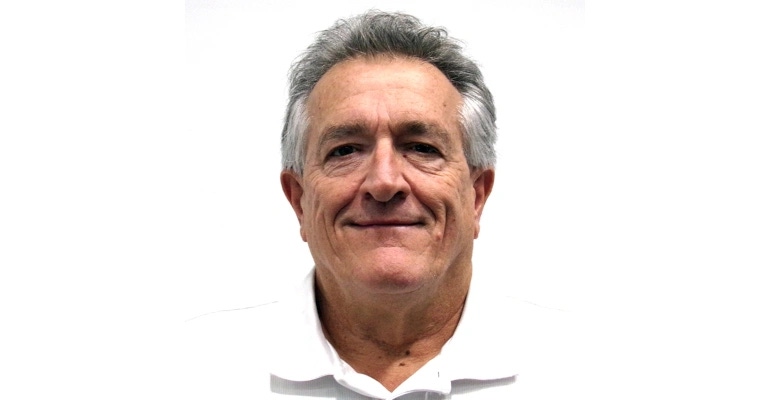
Recently, Powder & Bulk Solids’ presented “Debottlenecking Existing Pneumatic Conveying Systems” as part of its DryPro webinar series. The webinar discussed problems with bottlenecking on pneumatic conveying systems and solutions on debottlenecking.
Jack D. Hilbert, principal consultant, Pneumatic Conveying Consultants LLC, discussed various scenarios on how to keep your pneumatic conveying system running properly without bottlenecking, which comprises flow. But it does happen, and when it does, here are some solutions. After the presentation portion of the webinar, a live Q&A took place. Below are the questions and answers.
As well, you can see this Debottlenecking webinar On Demand here.
Q. When starting from scratch, how do you estimate the required conveying line diameter?
Starting from scratch, the conveying line diameter is going to be a function of two things. First of all how much pressure do you have available to utilize. Meaning, are you going to limit yourself to a PD blower? If you do that, you’re going to be trying to find a diameter that’s big enough to handle your material over the length you want to run of that including the number of changes in direction and the rate and be less than 15 psi.
If you use a compressor, a single-stage compressor might be able to go up to 40 or 45 psig. Typically, the higher the pressure limit you set for yourself the smaller the line diameter can be. If you want to limit yourself to a pipe size first, that’s going to drive you to a higher or lower pressure. In terms of the actual calculation, in previous webinars and presentations I’ve given two or three different ways to calculate the pressure drop in the system. You have to assume a diameter and an estimated pressure drop, based on the type of air supply you made earlier.
You then go through the calculation procedure based on those assumptions and see what your pressure drop is. Then you look at it and say, gee this pressure is higher than I have available, so I have to go back and do the same calculation over again with a larger pipe diameter to bring that pressure drop down. Conversely if you go through your calculation based on the diameter you assumed and you have a much lower pressure than you anticipated; for example, if you have a 3-inch pipe with 2 psi, you can go to a smaller diameter size pipe.
Q. If you increase the RV speed and/or pressure at the RV do you expect additional air leakage? As that has an effect on the blower capacity, how do you estimate that?
Yes, I expect more air leakage as I speed the airlock up. Air leakage through the rotary airlock comes in two forms: When we spoke about this before, I called one the static leakage and one the dynamic leakage. The static leakage happens because of the clearances between the tip of the rotor OD and the ID of the rotary airlock body. So, for a standard airlock, that clearance and whatever your operational pressure differential is across the airlock — whether it’s 2 psi in the convey line or 10 psi, the higher the differential pressure, the more leakage through those clearances. So even if the feeder wasn’t turning, but you were able to artificially create that pressure in the line, you’re going to have that element of static leakage as a function of differential pressure.
Now more importantly, every time that rotor comes around (a rotor has so many cubic feet per revolution displacement), when it’s conveying material and if that pocket is 100% full, you’re getting so many cubic feet per revolution of that material. When that pocket runs empty, at the bottom, the 6 o’clock position, it’s returning a pocket full of air, at whatever pressure the convey line is operating at that point in time So the leakage that you’re losing is that same cubic foot per revolution displacement in addition to losing the static leakage.
The dynamic leakage is a function of RPM and pressure, because when that pocket refills with air after it’s discharged, it’s air at whatever pressure in the pipeline you have. If you’re running at 8 psi that pocket is under 8 psi. When it comes around, and it vents or releases itself, before it can receive more material, that pocked is depressurizing back to atmospheric condition, or negative if it’s going to a dust collector. So that air is expanding from the ACFM to the SCFM condition. That value of SCFM MUST be added to the SCFM you determine is required to convey the material BEFORE you select the pressure blower package.
Q. Where can I find the saltation velocity calculations?
If you can’t locate it in a previous webinar, drop me an email and I’ll send you information on the five different sources. If you just Google “saltation velocity calculations” I think you’ll find those same names such as Risk, Weber, Klinzing; they’re all going to pop up when you Google it.
Q. How would utilizing multiple blowers together affect the system and/or the accuracy of their performance curves?
Let’s say for example we need an additional volume of SCFM, when we change material in an existing pneumatic conveying system. If I went to the curve and it said this blower can do it, maybe with a speed change or motor HP change or both, that would be great. But, what if that wasn’t the case — what if I had a very small blower installed and I could not get the extra volume from that existing blower. I would have two choices: I can put in a new, larger blower or I can put in a second blower and run it parallel to the existing one for the additional volume.
What I would do for example, if I didn’t need to double that blower’s volume; I just needed about 30% more I would put in the same size blower I have now for uniformity of two blowers the same size and minimizing my spare parts, and I would set both blowers at the speed to give me half the volume I need from each one and let them run in parallel condition. Under that situation, they are both always seeing the same back pressure and you can look at the curve for that blower at the speed you’re at against the back pressure. Each is running at half the volume you need but both are delivering that air against the same back pressure.
Q. I believe it is typically recommended to have ~6 pipe diameters between each change of direction or line step. Does that apply as you move further down the line, or is that primarily at the first part of the line? Can you step the diameter of a line directly after a change of direction?
Typically my preference has always been to try to step a pipe diameter in a vertical segment of pipe where I know that my material and air are fully suspended. (IE on the order of 10 to 20 feet after the bend) But in this case, with the example I gave you [in this webinar], I had to go into that last horizontal section — which is OK, you can still step it. But the calculations showed I needed to go the additional 25 feet in order to get enough pressure reduction and have enough volume increase. Even if that wasn’t the case analytically, I still would never step a pipe diameter immediately after a change of direction.
Typically, 10 pipe diameters should be OK in the dilute phase conveying. Sometimes if I’m coming in two-phase flow or dense phase and I want to step that pipe, I have to be worried more about material not being equally distributed in the pipe’s cross-sectional area. But typically, 6-10 diameters would be OK for stepping. Just do not step immediately after a change of direction.
And again, preferably look for a vertical section of pipe to step it in. But I’ve stepped a lot of pipes in a horizontal. When we talked about stepping in a vertical pipeline I would step with a concentric increaser and in a horizontal pipeline I would step with an eccentric increaser so that the bottom of the pipe is at the same elevation, so you preserve your pipe supports.
Q. Will the wear and tear of the pipeline increase due to higher air volume?
Not necessarily. The wear and tear of the pipe is a function of velocity. And not just velocity as a linear function, but the velocity to the exponential of the 3rd or 4th power. That’s why we step the pipe. For an example with a 6-inch pipe at a certain velocity, this material was not abrasive today, but let’s say it was. I’d have abrasive wear taking place. I would step to the bigger pipe my volume has increased because of the expansion by having increased the original volume of air — the original SCFM or ICFM into the blower. I’m only increasing that ACFM in the pipeline.
So, in that case, if I were to have stayed in that same smaller pipe, with the higher velocity, then yes, I would get more wear in the back of the pipe than the front of the pipe. But because we stepped the pipe diameter, I was back to a lower velocity profile so I would expect a lower level of wear in that back section of pipe because of the larger diameter and a lower velocity profile in that section of the pipe.
Q. How do you select dense phase and lean phase?
Dense phase and dilute phase refer to the mode of conveying taking place inside the convey line. The primary difference between the two is the velocity profile achieved with reference to the product’s Saltation Velocity.
Simply stated, when the gas velocity is greater than the product’s Saltation Velocity, the mode of conveying is lean phase (aka dilute phase). When the gas velocity is below the product’s Saltation Velocity, the mode of conveying is dense phase.
Electing lean phase is relatively easier as basically ALL products CAN be conveyed in lean phase, BUT the question is SHOULD they. Lean phase is typically the mode of conveying with lower solids to gas ratio and highest velocity profiles making them very susceptible to experiencing abrasive wear if the product is abrasive and also creating a lot of product damage to the material’s physical nature if the product is degradable.
What complicates the dense phase selection process is that not all materials are capable of being conveyed in dense phase the same way as other materials and sometimes not at all.
If you are just considering the use of dense phase, or interested in what type of equipment might be required, that can be handled in discussions with some analytical calculations and maybe some bench top testing of the product.
Once you have decided to pursue a commercial installation, it is strongly recommended you speak with several vendors of dense phase conveying systems to learn about their specific hardware, technical approach and capabilities in conducting lab scale conveying trials on your material to determine if your product needs any special design considerations.
Q. How much velocity should be maintained in the pipe?
The velocity requirements of the convey line are first determined by the physical properties of the product to be conveyed and the procedure you choose to use to determine the Saltation Velocity.
Once the Saltation Velocity has been established either by calculation, testing in your own facility, prior experience or in conjunction with equipment vendors, the pickup velocity for the product is determined.
That is the beginning of the velocity profile and the pressure drop you have determined for the convey line will then establish the terminal velocity of the system if you stay in a constant diameter pipe.
If the velocity profile becomes excessive, that is when you can consider incorporating a stepped diameter pipe to lower the overall velocity profile.
Q. Is the use of inclined piping not an option, instead of the horizontal/vertical combination?
In general, the recommendation is to try to maintain horizontal and vertically upward convey lines wherever possible. If there is a situation where an inclined line is necessary, it can be addressed by more experienced system designers.
As a general guide, if the angle of the incline is less than 15 degrees from the horizontal or from the vertical, the line is treated as being horizontal or vertical. As the angle of incline approaches 45 degrees, additional pressure drops are included and the velocity profile in the inclined section is more scrutinized. The preference would be to have sloping upward lines be included towards the end of the system rather than early in the system to have the benefit of the higher velocity at that location.
About the Author(s)
You May Also Like