Running the Plant on Dried Potato By-Products
January 31, 2012
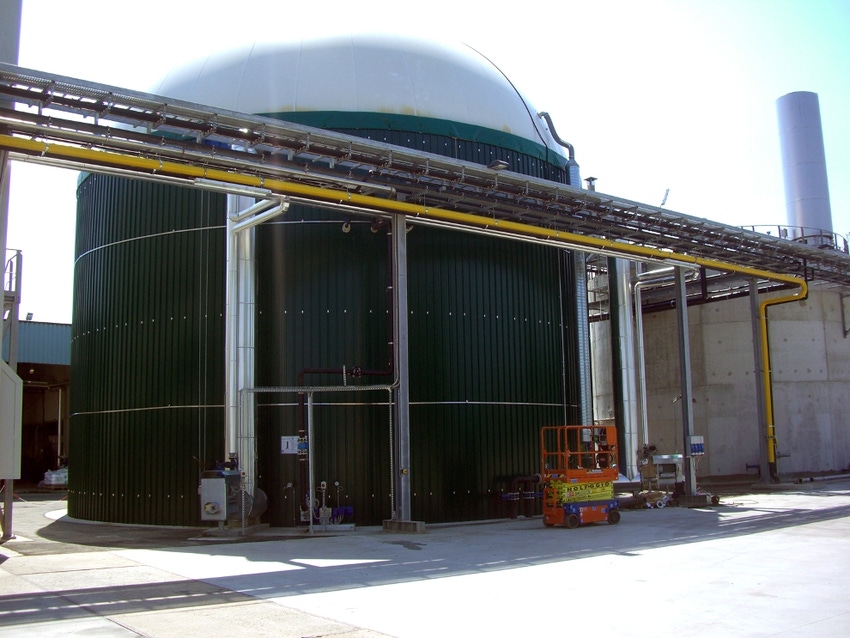
A °Celsius screw heat exchanger is used for a sustainable co-fermentation process in which wastewater, together with potato skins and starch, is converted into biogas. As a result Pizzoli S.p.A, Bologna, Italy, the biggest potato processor in Italy that has been supplying a wide range of fresh and deep-frozen potato products since 1926, has become almost self-sufficient in its energy supply (heat and electricity).
The Process
When processing potatoes, wastewater is produced that contains a large amount of organic material. When treating this wastewater the organic material can be converted by bacteria into biogas, this biogas is a mixture of methane and carbonic acid. The plant processes not only the wastewater released but also all the residual streams, in which the residual products are converted into biogas in the fermentation plant.
The biogas produced is used as fuel for a biogas motor that drives a power generator. The heat from the motor cooling and the exhaust gases is recycled to produce steam, hot water and to heat the thermal oil for the screw heat exchanger that dries the digestate. The remaining biogas is used to fire the steam boiler. Because of this co-fermentation Pizzoli S.p.A. has become almost self-sufficient in its energy supply.
The digestate from the fermentation plant together with the wastewater is processed in the water treatment plant. The wastewater from the water treatment plant is then treated to give a water quality that is suitable for recycling in the production process. Pizzoli S.p.A. is hence drastically reducing its water consumption. The remainder of the wastewater is thoroughly treated to give a quality suitable for discharge.
Screw Heat Exchanger for Drying Digestate
The screw heat exchanger was specially designed for the biofermentation plants to dry digestate, using the energy available in the exhaust gases. Via a heat exchanger thermal oil is heated by the flue gases to around 280ºC. The trough and the two screws of the screw heat exchanger are heated with this oil, in this way the digestate is dried by indirect heat transfer. A moisture evaporation rate of 500 to 600 l/hr is feasible; less moisture in the digestate does of course mean lower disposal costs. The plant is paying for itself in full by all the savings and recycling.
The Celsius screw heat exchanger is custom-built in addition to which the process is guaranteed by Celsius on the basis of tests, calculations, engineering, and experience. For example, the screw heat exchanger is a double screw (2 x Ø800) with a capacity of 850 kg/hr and reduces the moisture percentage of the digestate from 80% to 58%. The thermal oil (280ºC) is circulated with a flow of 15 cu m/hr at a maximum operating pressure of 5 bar. The thermal capacity is 350kW. The total width of the machine is 2.2 m and it is 2.4 m high and 11 m long. It weighs about 20,000 kg.
Design and Engineering
The design and engineering of the fermentation plant and a water treatment plant for Pizzoli S.p.A. in Italy was carried out by Colsen International b.v., environmental technology consultants in Hulst. The design, engineering and production of the screw heat exchanger for drying digestate was carried out by Celsius, the specialist division as regards Screw Heat Exchangers of Van Beek BV from Drunen. Celsius screw heat exchangers are available from Kemutec in the North and South American markets. For more information, call Keumtec at 215-788-8013, or visit www.KemutecUSA.com.
You May Also Like