CSB Releases Final Report on Fatal Vapor Explosion
A flammable vapor explosion and fire occurred at the Yenkin-Majestic paint facility in Columbus, OH, in 2021.
December 5, 2023
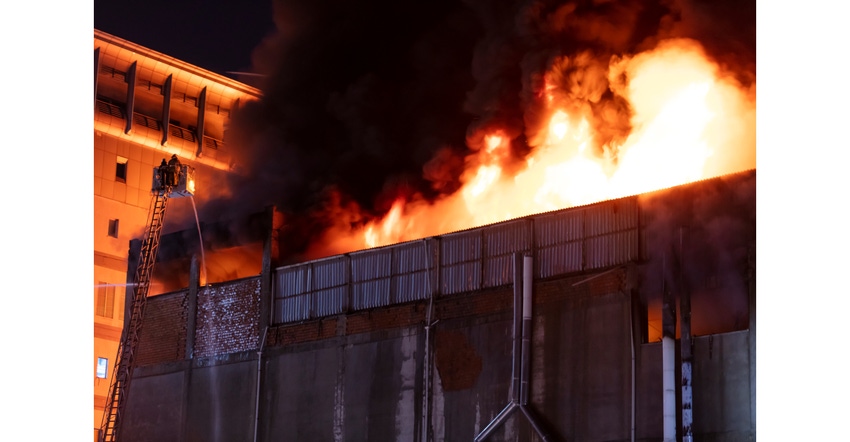
The US Chemical Safety and Hazard Investigation Board (CSB) recently released its final report on a flammable vapor explosion and fire at the Yenkin-Majestic facility in Columbus, OH, on April 8, 2021. One employee died during the incident, and eight workers were injured. The CSB’s final report makes several safety recommendations to Yenkin-Majestic, as well as to professional and trade associations.
The explosion and fire occurred around midnight on April 8, 2021, at the paint and coating plant when a mixture of flammable naphtha solvent vapors and resin liquid escaped through the seal of a closed manway of an operating kettle, creating a flammable vapor cloud that quickly spread throughout the facility. Minutes later the flammable vapor cloud found an ignition source, causing a huge explosion and a large fire that burned for roughly 11 hours.
More than 100 firefighters responded to the scene, including hazmat teams. Nearby buildings were damaged, and a fire broke out at an adjacent property. Yenkin-Majestic estimated that the incident caused over $90 million in property damage to the site.
The CSB determined that the release occurred through the closed manway after the kettle became pressurized by the rapid vaporization of solvent in the kettle when the kettle’s agitator was switched on after it was discovered that the agitator had not been operating while the solvent was being added to the kettle, as it should have been. In its investigation, the CSB found that the manway was not designed, constructed, or pressure tested to a design pressure appropriate for the process.
“The CSB’s investigation determined that Yenkin-Majestic failed to adhere to basic pressure vessel integrity quality assurance practices and did not have any engineering controls that would have prevented solvent from being added to the kettle when the agitator was turned off," explained CSB Chairperson Steve Owens. "The impacts of this incident also were much worse than they should have been due to Yenkin-Majestic’s failure to install effective warning alarms, failure to adequately train its employees, failure to require employees to wear flame-resistant clothing, and failure to have adequate emergency response preparations in place. Additionally, the CSB determined that there is a general lack of clear industry guidance for low-pressure vessels used in hazardous chemicals service.”
The final report highlights three key safety issues:
Mechanical Integrity of Low-Pressure Vessels. Yenkin-Majestic did not adequately ensure the mechanical integrity of a new 20-inch manway that was installed on a process vessel (Kettle 3) approximately three months before the incident. The CSB determined that Yenkin-Majestic did not follow basic quality assurance practices, such as adequately pressure testing equipment after alterations, which led to this release. The CSB also determined that although pressure vessels that can operate over 15 pounds per square inch gauge (psig) are subject to pressure vessel safety codes, there is little industry guidance specifically for the design, construction, and alteration of pressure vessels that do not exceed 15 psig.
Safeguard Selection and the Hierarchy of Controls. The hierarchy of controls is a risk management principle based on ranking hazard controls from most effective to least effective. On the day of the incident, Yenkin-Majestic did not have engineering controls to prevent the incident sequence. Yenkin-Majestic also relied on the operator to recognize and respond to the agitator turning off, without the assistance of alarms. Administrative controls (such as alarms, operating procedures, and operator training) should not be relied on alone, without additional robust design and engineering controls in highly hazardous chemical processes.
Emergency Preparedness. Yenkin-Majestic did not have adequate mitigative safeguards to minimize the consequences of the incident. For example, Yenkin-Majestic did not effectively utilize flammable gas detection systems and associated alarms to audibly notify onsite personnel of a hazardous gas release and the need to evacuate. During the incident, some of the gas monitors installed within the Yenkin-Majestic facility detected the flammable solvent release approximately one minute after the release began and sent an email to offsite personnel, but the gas monitors did not sound audible alarms to warn employees of the hazard. Additionally, Yenkin-Majestic did not specifically train its employees to recognize and respond to the presence of a flammable solvent vapor cloud and its associated hazards. During the incident, this overall lack of hazard recognition led to some personnel approaching the hazardous gas to investigate the release instead of initiating a plant-wide evacuation.
“The CSB calls on operating facilities to examine the three safety issues identified in the report and apply the report’s key lessons to their own facilities. Safe pressure vessel operation, implementation of the hierarchy of controls, and proper emergency response training for personnel are imperative for thousands of facilities across the country," said Investigator-in-Charge Melike Yersiz.
As a result of the investigation, the agency issued recommendations to Yenkin-Majestic, as well as two trade and professional associations.
The recommendations to Yenkin-Majestic include a call to update mechanical integrity procedures and implement applicable engineering standards for all pressure vessels in highly hazardous chemicals service, including pressure vessels that do not exceed 15 psig. Further, the company should install flammable gas detectors that alert plant personnel of a flammable hazard and demonstrate the use of the hierarchy of controls in its future resin plant designs. Also, the company should require personnel to wear flame-resistant uniforms in all operating areas that process flammable chemicals and update employee training material to include the requirement for and purpose of PPE use.
The CSB recommends to the American Petroleum Institute (API) to develop specific design, construction, and alteration guidance for low-pressure process vessels in flammable and other highly hazardous chemicals service that do not exceed an internal pressure of 15 psig, which could be incorporated into its existing standards. The CSB further recommended that the American Society of Mechanical Engineers (ASME) to work with API with the development of this guidance.
“The CSB has made recommendations both to Yenkin-Majestic and to the API and ASME to improve operation not only at the Yenkin-Majestic facility, but at any facility that deals with flammable and other hazardous chemicals at low operating pressures," said Owens.
The mission of the CSB is to drive chemical safety excellence through independent investigations to protect communities, workers, and the environment.
About the Author(s)
You May Also Like