MidProp MT Filter Bag Improves Baghouse Performance
August 10, 2012
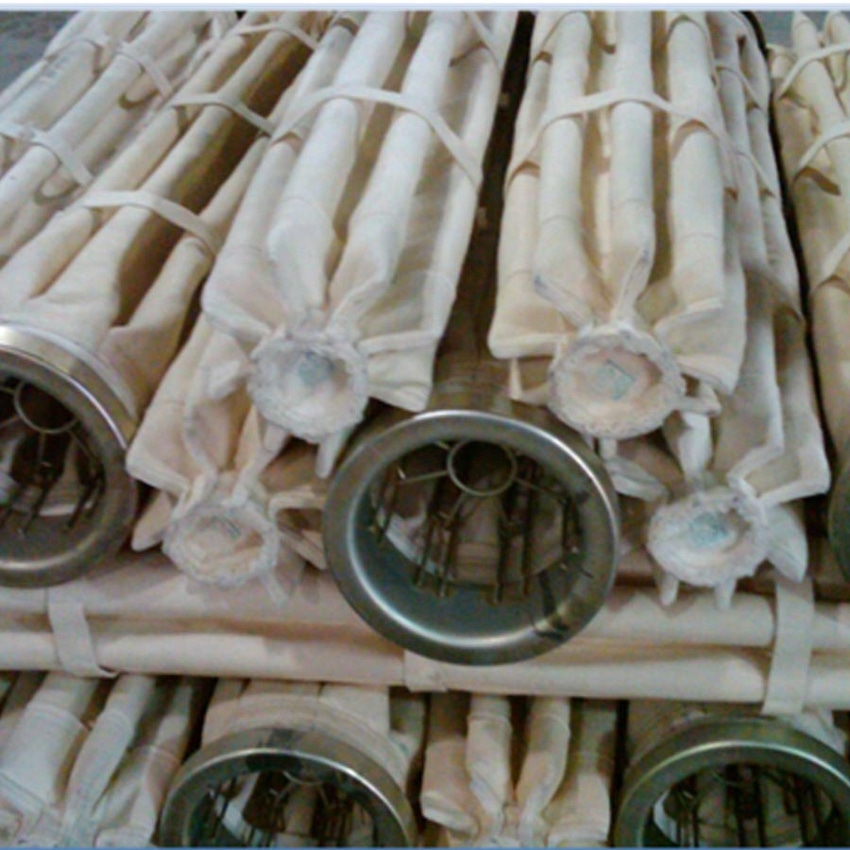
A major North American cement manufacturer was experiencing multiple baghouse issues that included premature bag failures, high operating differential pressures, and high-impact abrasion, and was faced with increased particulate capture requirements. The suggestion was to use Midwesco’s patented MidProp MT bags and cages for the customer’s clinker cooler, raw mill, and several other auxiliary dust collectors at one of its locations in the Midwest to address these challenges.
The MidProp MT bag is a patented filter bag design that was developed to fill the gap between filter bags and pleated cartridges. MidProp MT bags are made with the same materials as used in traditional style filter bags – including polyester, aramid, PPS, and felted fiberglass; while increasing the filter area up to 100% with eight very open pleats. The pleats are formed with the use of an eight finned cage. With the shape of the uniform positioning, the propeller bag significantly increases the filtration surface area while using the same number of filter elements. In addition, the structure of the propeller bag reduces the air-to-cloth ratio and differential pressures, which leads to significant efficiency gains and reduced energy consumption with the use of a VFD on the fan.
Application: Clinker cooler
Number of bags: 2176
Eight compartments, each with 272 filter bags
Original length: 14 ft
Material: aramid
The root cause of the problem was that the customer’s cooling system was undersized and they were experiencing difficulty with very brief bag life for many years - from 8 to 12 months with several bag replacements during that period. In the past the customer was replacing at least 50% of the filter bags every six months during their maintenance shutdown/outages.
Their central inlet had four compartments on each side. Most of the damage to the bags occurred in the bottom section of the bags and the two end compartments due to inlet abrasion.
Despite their clinker cooler being undersized, the customer wished to increase their capacity by 25% to 245,000 cfm but did not have the space, time, or budget necessary to increase the size of the unit.
With hopes of a quick fix, the customer made modifications to their inlet and replaced valves to evacuate the hopper quicker, but this action did not achieve the customers anticipated results.
The baghouse operated alone at a differential pressure of 6 in. with new bags. However this increased quickly to 10–12 in. before having to shut down due to broken/failed bags.
After assessing the dust collector conditions, Midwesco’s MidProp MT bags and cages were installed as a trial in the worst compartment. After a trial of several weeks, the customer decided to replace an additional two compartments.
After a three-month evaluation with no issues of failed bags, Midwesco’s MidProp MT Propeller bags were installed with a shorter 118-in. overall length MidProp MT.
The current life of the MidProp MT is 18 to 24 months, and the differential pressure ranges between 4 and 6 in. In order to help with the wear, Midwesco worked with the customer and added a 6-in. reinforcement at the top to reduce wear damage due to the higher velocities and help increase life to a minimum of at least 24 months.
After installation, the customer has noted increased performance results including improved bag life, lower operating differential pressures, reduced emissions, and higher production capacity, and, because of lower usage of compressed air and energy, the operation costs decreased significantly.
For more information on Midwesco Filter Resources (Winchester, VA), call 540-667-8500 or visit www.midwescofilter.com.
You May Also Like