Dust Collection Basics for Powders & Bulk Solids
Understanding the basic principles of dust collection system design can help plant managers make better dust control decisions.
March 13, 2024
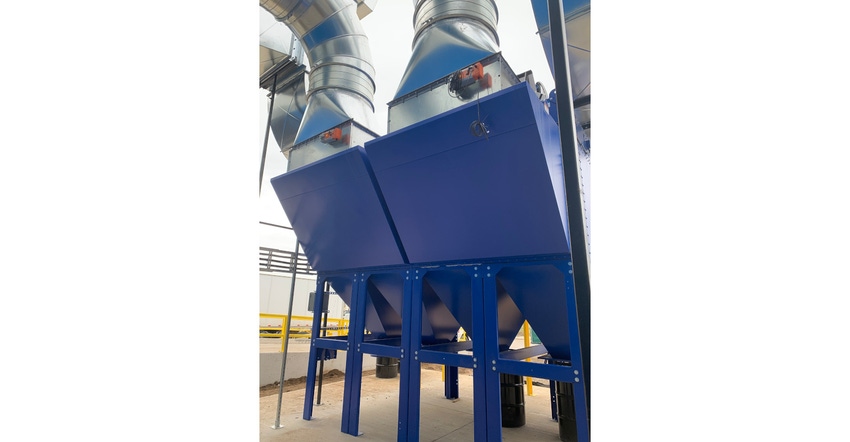
Effective dust collection is crucial in dry processing and bulk solids handling applications, not just for maintaining a clean work environment but also for protecting machinery and ensuring worker health. Understanding the basic principles of dust collection system design—including source capture options, filter media selection, and safety considerations—can help plant managers make better dust control decisions.
Factors in Dust Collection System Design
Dust collection systems are never “one size fits all”—especially in the diverse universe of powder & bulk solids applications. Designing the system requires understanding the unique characteristics of the dust, the facility, the environment, and other important variables. There are a number of questions to ask before starting solution design.
Dust Characteristics
The first issue to consider is the dust itself. Understanding the dust may require dust testing and analysis to determine physical and chemical characteristics. Important variables include:
What is the particle size distribution? What is the smallest size particle that must be captured?
Is the dust toxic or hazardous? What is the capture rate that must be maintained to meet any applicable Permissible Exposure Limits (PELs)?
Is the dust combustible? If yes, what are the explosion indices (KST, PMAX, Minimum Ignition Energy (MIE), and Minimum Explosible Concentration (MEC)) for the dust?
Is the dust abrasive?
Is the dust wet, hygroscopic (moisture attracting), sticky or oily? What is the moisture content of the dust?
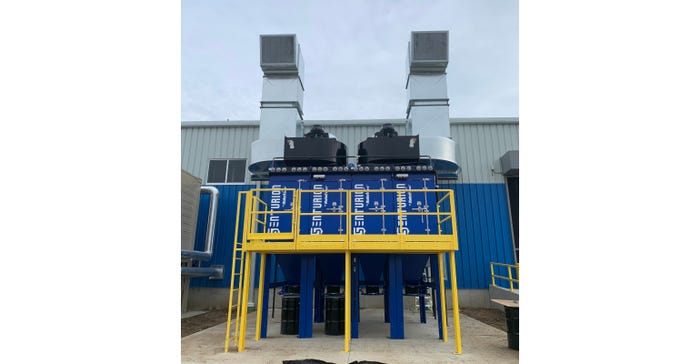
A large cartridge dust collection system installed outside a facility. The large exhaust ducts vent clean, filtered air to the outside (image courtesy of RoboVent)
Process Characteristics
Process characteristics must be considered when designing the solutions. For example:
What is the rate of dust generation in the process? Are there varying dust concentrations or types produced at different stages?
Can the process be fully or partially enclosed? What is the volume of air that must be moved for efficient capture?
Does the dust or powder need to be reclaimed/reused?
How clean does the production environment need to be? Is cross-contamination a concern?
How does the process temperature or moisture content impact dust characteristics?
Are there potential points of ignition or other safety factors that must be considered?
Environmental Characteristics
The environment also plays a big role in dust collection system design. Some of the biggest factors include:
What is the temperature range of the ambient environment in which the system will operate?
What is the humidity range?
Are there large seasonal variations?
Facility Constraints
The physical layout and limitations of the facility are key considerations in system design:
What are the spatial constraints for installing the dust collection system?
How can the system be integrated with existing processes and equipment? Are individual dust collectors needed for each line or process, or is the facility and production line setup suitable for a centralized dust collection system?
Are there any structural limitations, like ceiling height or floor load capacity, to consider?
Is it possible to place the dust collector outside?
Safety and Regulatory Considerations
The dust collection solution must be designed to comply with all regulatory requirements and industry standards. Questions to ask include:
Does the dust have a PEL set by the Occupational Safety & Health Administration (OSHA) or other regulatory body?
For combustible dust, which National Fire Prevention Association (NFPA) standards apply? Is a Dust Hazard Analysis (DHA) required as part of the solution design?
Other Considerations
Other factors may also influence the design and implementation of a dust collection system. For example:
What is the budget for the dust collection system?
How much maintenance will the system require? Will maintenance be managed in-house or through a service contract?
How energy efficient is the system?
Are there future expansions or modifications planned that might affect dust collection needs?
Basics of Dust Collection System Design
Designing a safe and effective dust collection system for bulk & powder applications requires a tailored approach and careful engineering. The American Conference of Governmental Industrial Hygienists (ACGIH) and the American Society of Heating, Refrigerating and Air Conditioning Engineers (ASHRAE) both publish standards and guidelines relevant to dust collection and industrial ventilation system design. Below are some of the basic elements to consider for solution design.
Source Capture vs. Ambient Dust Collection
Dust collection systems may be either source capture (collecting dust from the source as it is produced, often using an enclosure or hood) or ambient (filtering air for the facility as a whole).
For almost all bulk & powder solids applications, a source capture solution is recommended. Source capture reduces the cost of dust collection by limiting the volume of air that must be moved. It also prevents potentially hazardous dusts from propagating through the facility or contaminating other processes, protecting workers from dust exposure and preventing cross-contamination of production lines.
Hood design is an important consideration in designing a source capture system. Some processes may be fully enclosed, while others may require a close-capture hood or fume arm. The system should be designed to minimize the volume of air that must be moved.
In some cases, a backup ambient filtration system may be recommended if the source cannot be fully enclosed and fugitive dust is a concern. Positive and negative pressure zones can also be used to prevent dust movement between areas of the facility.
Centralized System vs. Individual Collectors
A dust collection system may either be set up as a centralized system or with individual collectors for different processes or production lines.
A centralized system uses one or more large dust collectors that are ducted to all the dust-producing applications in the plant. Centralized systems tend to be more energy- and cost-efficient for large plants with many processes. They also simplify maintenance, as there is only one system to service. These large dust collectors are often placed outside.
In some applications, it makes sense to have a smaller individual dust collector ducted directly to an enclosure hood for a specific process. These systems eliminate the need for long duct runs and provide more flexibility and localized control.
Dust Collector Types
There are several types of dust collectors used for powder & bulk solids applications.
Baghouse dust collectors are still commonly used for some very large applications with very high airflow (cu ft/min, or CFM) requirements. These collectors use large fabric bags to filter dust.
Cyclone dust collectors use centrifugal force to separate our larger dust particles; they don’t have the ability to control fine dust and powders. However, they are sometimes used for pre-filtration in powder & bulk applications to remove heavier, coarser dust particles before final filtration.
Cartridge dust collectors are increasingly popular for powder and bulk solids applications due to their versatility, energy efficiency and space-saving design. These collectors use cylindrical pleated filter cartridges, which come in a wide range of media types and filter efficiency ratings. This makes them adaptable to many different types of dust, including abrasive, ultrafine or hygroscopic dust.
Dust Collector Sizing
There are three essential elements to dust collector sizing:
1. CFM: The CFM rating for the dust collector is a measure of how much air the dust collector can move within a particular time frame. CFM requirements depend on the volume of air that must be moved and the air velocity that must be maintained for efficient dust capture and to prevent the settling of dust in the system.
2. Static pressure: This is the amount of air pressure or resistance the fan can overcome in the system. This will include resistance from the system design (e.g. distribution pipe runs) as well as resistance in the collection system (e.g. filter loading). Sizing your fan appropriately could be the difference between a successful system and one that is not capable of removing particulate effectively.
3. Air-to-cloth ratio: In a cartridge collector, this is the ratio between the CFM of the dust collector and the area of filter media. The higher the dust load, the more filter media you need for each unit of air you are moving.
Filter Selection
Filter media selection depends on the characteristics of the dust to be collected and the level of capture necessary to meet indoor air quality goals, OSHA PEL requirements, or process cleanliness requirements.
Filtration efficiency: Cartridge filters are commonly rated using the MERV scale, which is a measure of how well the filter is able to capture particulate in different size ranges. The higher the MERV rating, the better the filter is at capturing finer particulate. Cartridge filters may come in MERV ratings between 10 and 16 (though all filter cartridges will approach a MERV 16 level as they accumulate a dust cake).
Media type: Cartridge filters come in various media types, including basic cellulose, spunbond polypropylene, and various coated media options. For fine and ultrafine powders, a nanofiber coating may be desired for higher capture efficiency. PTFE-coated filters provide better dust release and longer filter life, especially when working with hygroscopic or oily dust. Filters with antistatic properties are useful for electroconductive dust types.
After-filters: Some dust collectors can be equipped with after-filters to collect ultra-fine dust, vapors, or gas-phase emissions. A HEPA after-filter is used when very clean conditions must be maintained for production processes or when collecting fine dust with high exposure risks (such as some chemical or pharmaceutical dusts). Activated carbon after-filters use adsorption to collect odors, vapors and gasses.
Abrasion Resistance
Many powders and bulk materials are highly abrasive. The dust collection system may require abrasion-resistant elements to protect filters and extend the life of the ductwork and dust collector.
Choose durable filters, such as PTFE-coated spunbond polypropylene, to extend filter life.
Dropout boxes and baffle systems can be used to protect filters from heavier dust.
Use an abrasion-resistant air intake.
For highly abrasive dust, the ductwork and filter cabinet can be lined with abrasion-resistant materials such as Ultra-High Molecular Weight (UHMW) plastic or a spray-on coating such as Rhino Lining. Wear points (such as ductwork elbows) should be inspected frequently for signs of wear.
Chrome-plated rotary valves are recommended between the hopper and collection bin.
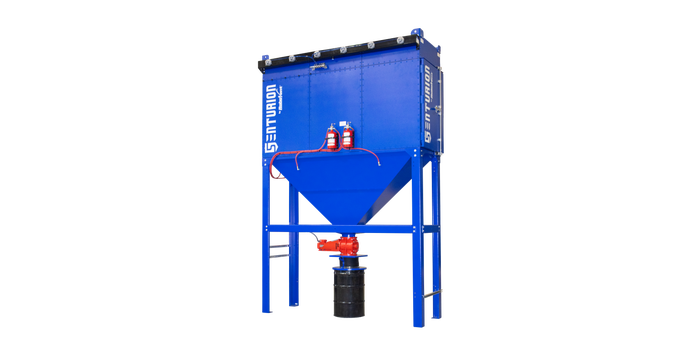
A clean agent gas fire suppression system installed on a cartridge dust collector. Fire suppression is an important element of dust collection system design (image courtesy of RoboVent)
Fire and Explosion Prevention
Dust collection systems for combustible dust must comply with National Fire Prevention Association (NFPA) standards for explosion protection, including NFPA 652, NFPA 654, NFPA 68, and NFPA 69. All dust collectors should also be equipped with fire detection and suppression systems.
Deflagration systems: A deflagration system is used to mitigate the effects of a dust explosion inside the dust collector. This will typically include explosion venting (standard or flameless) to safely vent excess pressure, an isolation valve to prevent pressure waves from propagating back into the facility, and a rotary airlock to prevent dust in the collection bin from fueling an explosion.
Fire protection: The fire safety system should include a smoke/fire detector, an automated emergency stop system, and a fire suppression system. Automated dampers may also be used to shut off the flow of oxygen if a fire is detected. Fire suppression options include water sprinkler systems, CO2 gas, or a clean agent gas system.
Spark protection: Though sparks are not as common in powder & bulk solids applications as in metalworking and similar industries, if sparks are present near the dust collector intake, a spark control device (such as a wire mesh spark trap or centrifugal spark arrestor) may be needed.
Other System Elements
Other system elements include:
Filter pulsing: Cartridge dust collectors, and some types of baghouse collectors, use a compressed air pulsing system to pulse excess dust off the filters and extend filter life.
Filter orientation: Cartridge filters that are oriented vertically, rather than horizontally, shed dust more evenly for increased longevity.
Motor/blower: High-efficiency motors and Variable Frequency Drive (VFD) motors, which adjust the motor speed to compensate for filter loading, can save considerable energy.
Collection bin or tray: For powder & bulk solids applications with heavy dust loads, look for a system that can be equipped with a larger collection bin (such as a 55-gal drum) to minimize maintenance. A bin sensor can be used to provide alerts when the bin is full.
Controls: Advanced control systems automate and optimize the dust collection process, adjusting fan speeds and cleaning cycles for peak efficiency and energy savings. These systems also enable remote monitoring and alerts, ensuring operational continuity and safety.
Ductwork: Careful planning of ductwork layout can minimize air resistance and reduce the energy required to move air through the system. Smooth, well-sealed ducts with gradual bends and minimal length reduce pressure drops and enhance efficiency.
Working With a Dust Collection Engineering Firm
A well-designed dust collection system will save energy, reduce maintenance requirements and downtime, and ensure compliance with regulations. Choosing the right solution partner for designing and implementing a dust collection system is crucial for ensuring the effectiveness, efficiency and safety of your bulk and powder handling operations. Here are some things to look for.
Industry expertise: Does the company have specific expertise in dust collection system design? Do they have qualified engineers and solution experts on staff? Look for a solution provider that is familiar with and will apply all relevant standards, regulations and industry best practices.
Service offerings: It can help to work with a firm that provides turnkey solutions across the entire process, including facility testing and needs analysis, system design and engineering, installation and commissioning, and after-care and preventive maintenance.
Warranty: What kind of warranty do they offer on their equipment and services? Work with a company that will stand behind their work and make things right if there are any issues.
Conclusion
A dust collection system is a long-term investment and is often a considerable capital expense. Understanding the basic principles of dust collection system design can help plant managers understand proposals and bids from providers and make better decisions.
Alysha Paris is director of engineering for RoboVent. She is an experienced manufacturing and design engineer with a proven track record of creating effective, safe, and efficient industrial air filtration and ventilation solutions to help clients meet or exceed OSHA standards for indoor air quality. Alysha oversees a team of engineers and system designers and guides the company in the development of new, innovative air quality solutions. For more information, call 877-959-5714 or visit www.robovent.com.
About the Author(s)
You May Also Like