Liquid to Powder Conversion: Improving Efficiency and Performance
January 31, 2012
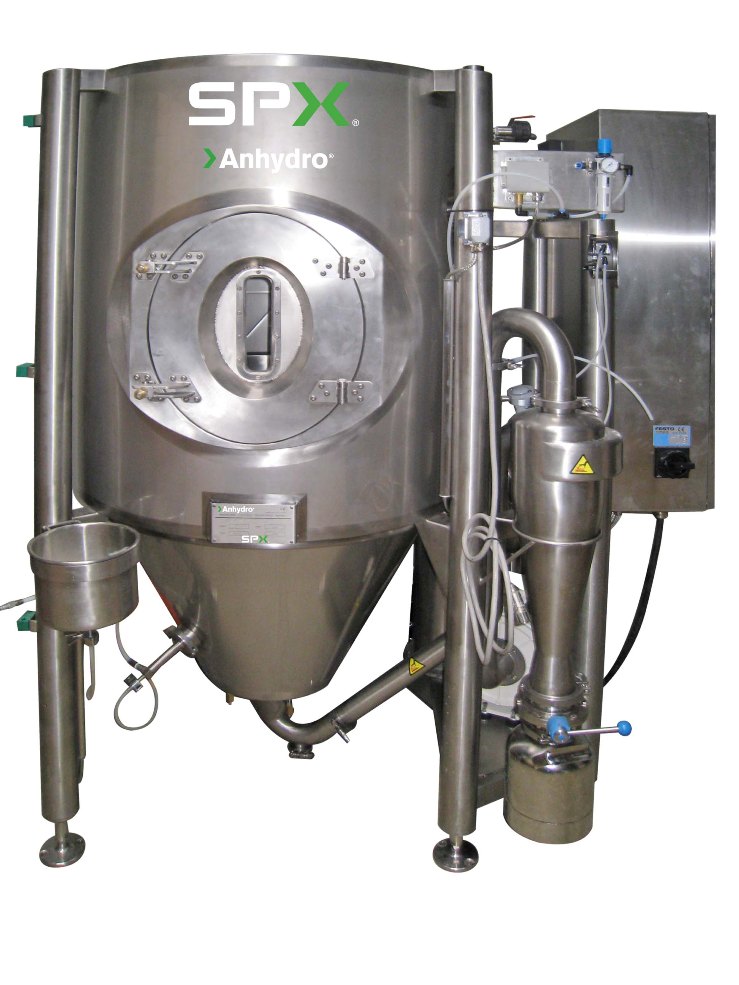
High yield is always an important factor in selecting the right drying process for converting liquids to powders – and the higher the cost of the product the more important it becomes. There are various methods by which to implement this process and the decision on which to use of course includes consideration of the capital and operational costs versus the savings gained by higher efficiencies.
The spray drying process is widely used across many different applications – chemicals, flavors, foods, and pharmaceuticals to name just a few. Spray dryers have many advantages and provide easy operation with continuous and rapid drying of a compound. Their simplicity does not require complicated automation systems and CIP is straightforward. They are known for their reliability, efficiency, and predictable scale-up.
The concept of using a spray dryer to convert fluids into dry powders is a simple one and has been utilized for many decades. The straightforward technique uses a heater with gas flowing through it (usually air) to dry the fluid. The thermal energy of the hot gas is consumed in evaporation so there is no heat damage to the product being treated. It is, therefore, very popular where the product may be sensitive to temperature changes and is widely used in the pharmaceutical and food industries.
Freeze drying, or lyophilization, is a typical technology choice to meet high-yield percentages, particularly of smaller particles in high-value areas such as pharmaceutical or biotechnology. However, this technology comes at a much higher cost and is a time consuming process, whereas a single spray dryer could replace six lyophilizers and maintain the same production capacity. A spray dryer installation is estimated to take 25% of the square footage of a lyophilizer, which requires significant additional machinery such as vacuum systems to support what is a quite complex process. The installed cost of a freeze-drying process compared to spray drying for the same production scale, is significantly higher. Therefore, a spray drying processor with a high yield at scale would offer numerous benefits with reduced costs and improved process efficiency.
Clearly the installed cost of a freeze-drying process compared to spray drying for the same production scale is significantly higher. So if a spray drying processor could bring a high enough yield at scale it would offer numerous benefits with reduced costs and improved process efficiency.
Instead of a cyclone for collecting powder, systems that use bag filters would, of course, also bring a high enough yield of product. Bag filters are not, however, suitable for use with all compounds. There can be issues with particles being retained within the bag for an undetermined amount of time and contamination of the product can occur with delamination of the filter media.
Spray dryers that use a cyclone to collect powder are a well-established technology and have predictable results as a process is scaled up in size. They offer precise control of all critical process parameters. This predictability and the simplicity of their operation also provides a high degree of user confidence and product consistency – perfect for applications in areas such as pharmaceutical that require validation. Historically, however, the yields have not been high for larger production capacities with particles in the range of less than 10 microns. The issue here is that the size of cyclone needed to gain the throughput is not ideal for the small particle sizes.
So, for an application where particle size is small, a bag filter is not suitable and high product value demands high product yields, freeze drying would seem to be the best option. If, however, the efficiencies of a spray dryer with a cyclone collection system to handle a higher production capacity could be vastly improved, it would remove a great deal of cost from the initial installation (capital cost) and significantly reduce ongoing operational overheads.
The solution is a relatively simple one: Instead of one larger cyclone, where there is potential for small particles to be carried through with the gas used to dry them, two smaller cyclones can be installed in parallel within the machine. Smooth, pharmaceutical-grade materials within the cyclones help with the execution of the process and the results are truly dramatic. The dual system provides a larger production capacity but with the collection performance levels of a much smaller system. Predictable performance and product consistency are maintained at the high levels expected from a spray dryer. Tests with a drying air rate of 150 kg/hr have shown a yield percentage in the high nineties for a particle size of about six microns.
High yield spray dryers bring an exciting alternative to expensive lyophilization techniques for many applications within the pharmaceutical and biotech industries. There are no requirements for vacuum systems and the installed and operational costs are greatly reduced. A single spray dryer could typically replace multiple freeze dryers to gain the same production capacity.
There are clear advantages to this dual cyclone spray dryer in the pharmaceutical industry where the operation also lends itself to straightforward validation of the system in line with FDA requirements. Its higher efficiencies, however, would be equally applicable to other application areas with higher cost products, for example flavors and fragrances, catalyst processing or high precision ceramics.
Robert Turok is technology manager, SPX Flow Technology Systems Inc. For more information, visit www.spxft.com.
You May Also Like