Drying End Point Measurement Options
January 30, 2012
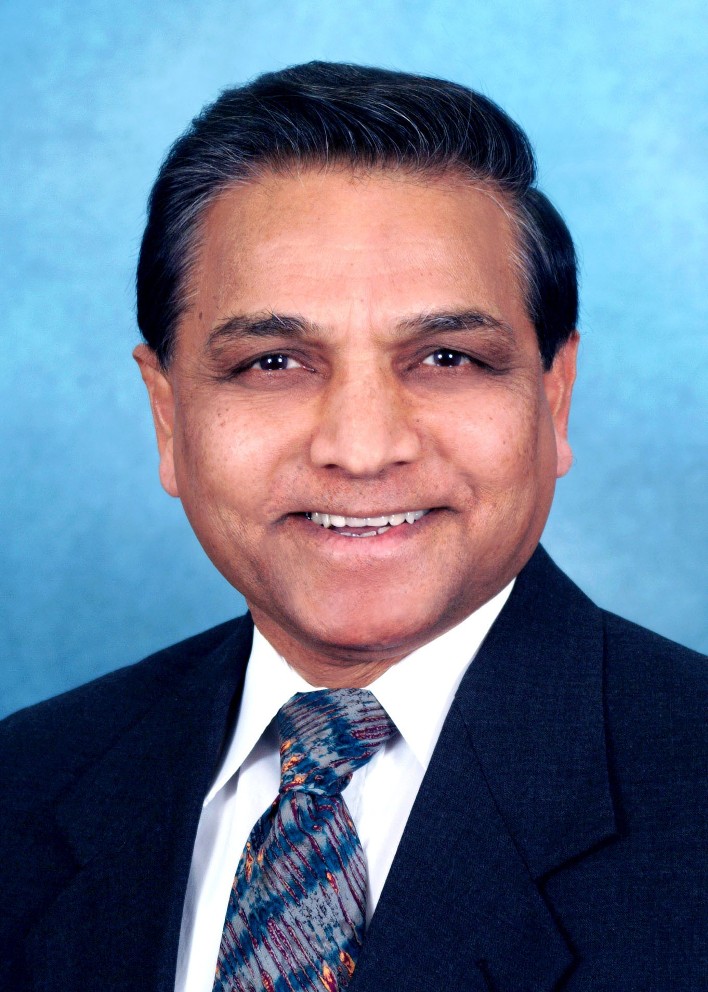
Drying is a vital unit operation in various process industries. The end point of drying is one of the critical process parameter that normally dictates final product quality attributes. Industries use moisture/solids analysis for a variety of process and quality tests. The speed and precision of the test, as well as the reproducibility of results, are vital for determination of whether or not product meets manufacturing specifications at key points of the process. A classical way of determining the end point of drying is to establish the drying curve by plotting the level of residual moisture in the product over a period of time and determine the point at which the desired level of moisture is reached. This measurement is done off-line by measuring loss on drying. Seasonally changing inlet air humidity affects the moisture content of the finished granules, as long as the drying process remains unchanged. The temperature of the granules increases linearly as the humidity of the inlet air is increased. This effect causes variation in moisture contents of the final granules of different batches when the fixed temperature of the mass is used as an end point criterion. Fluidization activity affects the drying end point.
Researchers expanded on the concept that the larger granules contain more water than smaller granules and developed a model to determine the water content of granule based on Near Infra red (NIR) to monitor the drying process in fluid bed. This model provided median water content of granules and hence the drying end point. NIR to measure moisture in a batch process is now becoming a common occurrence. NIR provides the product moisture profile throughout the drying process. The challenges in applying NIR for continuous processes are somewhat different. These include among others, sampling issues, calibration, and stability. To obtain relatively fast measurement, multi-point measurement system is used to provide the moisture content and the homogeneity of the product. Near Infra Red (NIR) can be used as a single point probe or a system that monitors up to eight sampling points for real-time moisture and solvent content. In-line measurements are done with diffuse reflectance insertion probes and using a software data which monitors and analyzes.
In the food industry, a method was developed for the automatic determination of near-ambient barley drying in static beds, based on a correlation to infer grain moisture content of the top layer, using a continuous on-line measurement of relative humidity and temperature of outlet air.
In a freeze dryer, drying occurs by sublimation. The partial pressure of water vapor in the drying chamber is high, but when the rapid evolution of water vapor ceases with the conclusion of sublimation drying, the partial pressure of water sharply decreases. The electronic sensor is employed to monitor the partial pressure of water, which provides the convenient and reliable method for determination of the end point of sublimation drying for the batch as a whole.
On-line mass spectrometry (MS) has been used as a tool to continuously monitor the headspace for solvent concentration. It has also been investigated in microwave vacuum drying operation. The microwave drying rates for polar solvents were shown to have a linear correlation with solvent heat of vaporization. MS profiles were shown to correlate with other drying end point parameters, including rate of recovered solvent, product temperature, and microwave reflected power.
In the pharmaceutical industry, batch fluid drying is the desired option for drying wet granules or active pharmaceutical ingredient (API). In response to the FDA’s Process Analytical Technology (PAT) initiatives, a number of process instrumentation companies offer solution that monitor processes and the drying end points. These are generally non-invasive and non-destructive methods. PAT-based applications such as multi-point NIR, Focused Beam Reflectance Measurement (FBRM), acoustic emission, and thermal effusivity, provide end of drying indication. These tools can be used to monitor the entire process as well as to produce desired product attributes.
Dilip M, Parikh is president of DPharma Group Inc., Ellicott City, MD, a pharmaceutical technology consulting firm. He is an industrial pharmacist with more than 35 years of industrial experience in R&D, manufacturing, cGMP complaint facility planning, and operational management at various pharmaceutical companies in Canada and the U.S. The editor of the “Handbook of Pharmaceutical Granulation Technology”, 3rd Edition, Parikh has authored three other book chapters and a number of scientific publications, and has spoken worldwide at scientific conferences on solid dosage technology development and manufacturing.
About the Author(s)
You May Also Like