Drum or Fluid Bed Dryers?
February 9, 2012
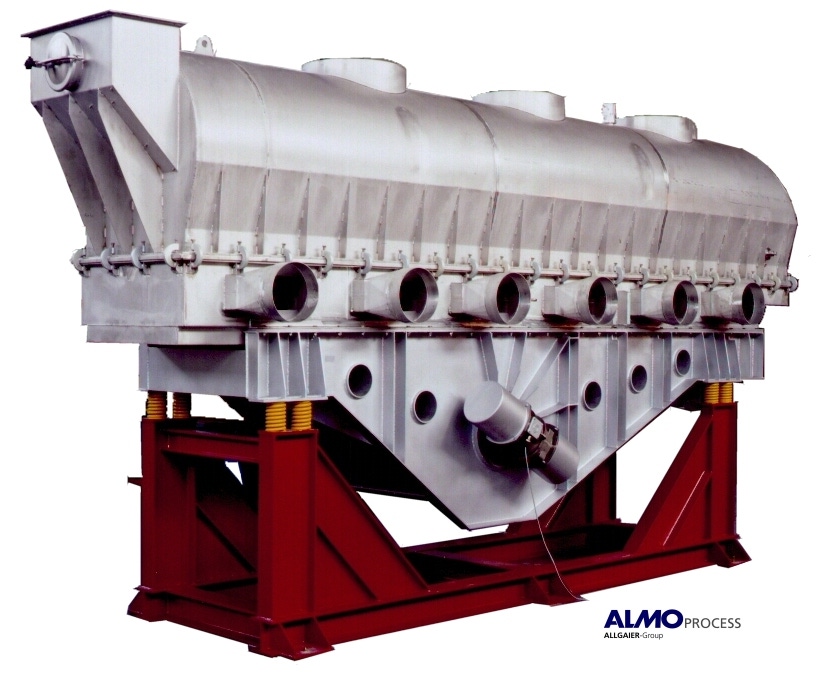
Dryer suppliers often promote their particular technology. This has led to uncertainty among users selecting an optimal drying system. One common dilemma is the decision between drum dryers (rotary kiln dryers) or fluidized bed dryers (vibration fluidized bed dryers). In some cases the two systems overlap with regard to their suitability. However, there is benefit from technical considerations during dryer selection. The product, the process, and external factors should be considered for the application. Product-specific criteria include particle size, size distribution, product temperature sensitivity, and abrasion. Process relevant criteria include the fluctuations in throughput rate, quality, moisture content, energy requirement (electrical/heating), and qualification skills of operatives. Additionally, external factors include the country of installation and associated infrastructure should be considered.
Drum Dryers
Modern drum dryers are almost all installed horizontally. Lifting blades pick up the moist solid from the bottom of the drum letting it fall again, allowing contact between the hot drying air and the moist solid. The combustion gases are mixed with part of the ambient air to obtain average drying air temperatures between 600 and 900°C. For thermally insensitive materials, (e.g. silica sand) the flame can burn directly into the rotating drum. For the drying of temperature-sensitive materials (limestone, clay, bentonite, plastic recyclate, or organic waste) firing chambers are used. In most drying applications, the solid material is conveyed in a co-current flow (i.e. in the direction of the gas flow).
Countercurrent applications are found mainly in the asphalt industry as well as in high-temperature applications and calcination. Drum dryers are built for solids with throughput rates between 5 and 150 tn/hr. One particular advantage of drum dryers is that they are largely insensitive to fluctuations in the starting moisture content of the material to be dried and to fluctuations in the feed rate, size of the particles or the inclusion of unwanted clumps or coarse particles. Drum dryers are suitable for fine sands, but especially for coarse and very coarse bulk solids. It is not absolutely necessary to adjust the air volume on product during changeover. With appropriate design of the internal fittings, even very abrasive materials can be processed in drum dryers.
Technical requirements for heating drum dryers are low. Modern burners have only relatively small combustion air fans. The moisture-laden dryer exhaust air is extracted from the dryer by means of an extractor fan, fed through a bag filter to remove any entrained dust and emitted into the environment through a chimney flue. The system of pipes for the exhaust air from the drum dryer is a comparatively simple arrangement as the air only has to be extracted from one point on the dryer casing. Drum dryers are especially tolerant to operating errors and therefore optimally suitable for installation in areas with underdeveloped infrastructure. The cost for automation of the dryer control system is comparatively low. In the event of a power outage, it is usually possible to resume operation when power supply is restored. In the event the supply of drying air cuts out, the solid in the drum dryer is reliably conveyed by the rotation of the drum.
Due to the comparatively simple setup of a drum dryer, end-users can perform dryer assembly on the construction site. This is advantageous in global markets where locally available exhaust air filters are used or air pipelines are installed by local companies. Additionally, drum dryers can usually be commissioned in a relatively short time. A key feature is their extremely energy-efficient operation. An essential factor for the efficient utilization of the heating energy is the optimal design of the dryer’s internal fittings as these have to guarantee optimal and intensive contact between solids and drying gas.
Drum Dryer Advantages
• Suitable both for coarse and fine solids
• Largely insensitive even to very coarse or heavy solids
• Minimal cost and effort for the supplied air equipment with direct installation of the burner at the dryer casing
• Insensitive to changes in the particle size
• Insensitive to variations in the moisture content and the throughput
• Insensitive to cut-out of the drying air
• Low specific electrical energy requirement
• High drying air temperatures combined with low heat losses
• Low heating energy requirement even when drying only partial loads by adjustment of the exhaust air volume
• Simple installation and fast commissioning
• Tolerance to operating faults
• Very rugged and thick-walled equipment with a long life-time
• Low wear and low replacement part requirement
Drum Dryer Disadvantages
• A requirement of heavy equipment (thick-walled design of the drum)
• Cooling in double-shell drying/cooling drums is limited to solid material temperatures of 55 to 60°C at the dryer exit
• Internal fitting design in drum dryers requires many years of experience
• Solid materials are only partially de-dusted in drum dryer
• Counter-flow applications are limited to coarse-grained materials
Fluid Bed Dryers
In an efficiently fluidized bed, the entire solid material is rendered into a quasi-fluid state by the air currents. At the end of the dryer, the same volume of solid runs over an overflow weir as wet solid material is added at the entry of the dryer. The solid material flows in a countercurrent to the upward current of air. The overflow weir is height-adjustable and, by the influencing of the height of the fluidized bed, enables adjustment of the solid material residence time. Due to constant flowing of air around every solid particle, sensitive wet granulate from granulating plates or combined mixer-granulators can be dried very gently in fluidized beds. Vibration of the fluid bed dryer ensures even coarse particles, which cannot be alone fluidized by the current of air, are transported. Depending on particle size distribution and bulk density of the solid material, the use of fluidized bed dryers is only recommended for particles approaching 6 mm. Otherwise, there is the possibility for coarse material to accumulate in the dryer as it cannot flow over the retaining weir at the end of the dryer. If no weir is installed at the dryer discharge, the solid material residence time can no longer be varied by adjusting the bed height. Poorly fluidized solid material would no longer be sufficiently aerated. Fluidized bed dryers should be fed with the predominantly fine-grained solid materials for which they have been designed. If, for example, on account of a product changeover, much coarser solids are fed to the dryer, fluidization can collapse. Efficient dryer operation can become impossible under certain circumstances.
With fluid bed dryers, the air director plates have to be designed with a sufficiently high pressure loss. This is in order to ensure an even distribution of the total drying air over the entire air flow of the dryer. The fans for drying air have to exhibit high compression. Otherwise, the air seeks the path of the least resistance through the bed of solid material in the dryer. As a result, fluidized bed dryers have higher electrical energy consumption relative to the solid material throughput rate (approximately 150% of a drum dryer). The electrical energy consumption of fluidized bed dryers remains constant even with partial loads and leads to increased specific electrical energy consumptions. Fluidized bed dryers should therefore be always operated in constant conditions and close to their design full load. As in the minerals industry, frequently fluctuating moisture contents of the solids to be dried must be expected in the course of a year, it is particularly important in the planning phase, to find a good compromise between the required maximum solids rate and the expected average starting moisture content of the feed materials. Plant design with reserves for solid throughput rate, as well as starting moisture content, will impact efficiency. This is particularly notable for overseas investments especially where it is not always possible to operate the plants in constant conditions.
Fluidized bed dryers are usually controlled by a constant holding of the temperature of the dryer exhaust air. Depending on exhaust air temperature, a control circuit influences the heating of the air and reacts to varying volumes or water content of wet material feed. A constant residual moisture content of the solid to be dried can be guaranteed. However, the specific fuel requirement per ton of dried material increases when the dryer is not operated at the optimum operating point of its original design. As the volume of air in a fluidized dryer must be kept constant on account of the necessary solids fluidization, the same absolute quantity of heat is lost with the exhaust air (despite the lower plant throughput rate).
Fluid Bed Advantages
• Intensive material and heat transfer based on the fluidized bed principle
• Countercurrent between the solid material and the drying air
• Controlled de-dusting of the solid material during drying and cooling is possible
• Low weight thanks to the thin-walled design
• Consequently, low-price stainless steel models possible
• Dryer-cooler variants enable a low fuel requirement thanks to heat recovery based on recirculation of the cooler exhaust air
• Low solid material temperatures are possible (approx. 10 K above the cooling air temperature)
• Special applications for coating, agglomeration and granulation, calcination, roasting, etc.
Fluid Bed Disadvantages
Possible disadvantages of fluidized bed dryers are:
• Optimally suited only for fine-grained materials to around 4 mm
• Limited drying air temperatures
• Sensitivity to abrupt changes in the solid material particle sizes, moisture content and throughput rate or to cut-out of the drying air
• Relatively high electrical energy requirement
• Expensive supplied air system consisting of fans, pipelines and separate hot gas generator necessary
• Significant effort and expense involved in commissioning and parameter optimization
High hot gas temperatures result in low volumes of drying air and, therefore, low heat losses emitted with the still warm exhaust air. For this reason, drum dryers operate very efficiently with the hot gas temperatures up to 900°C common in the minerals industry, although the exhaust air temperatures of drum dryers are slightly higher than, for example, the temperature of the exhaust air from fluidized bed dryers.
Dr. Mathias Trojosky is the Head of the Drying Department at Allgaier GmbH. For more information, call 513-402-2566 or visit www.almoprocess.com.
You May Also Like