News
Nowicki Food Machinery Now Called NOMA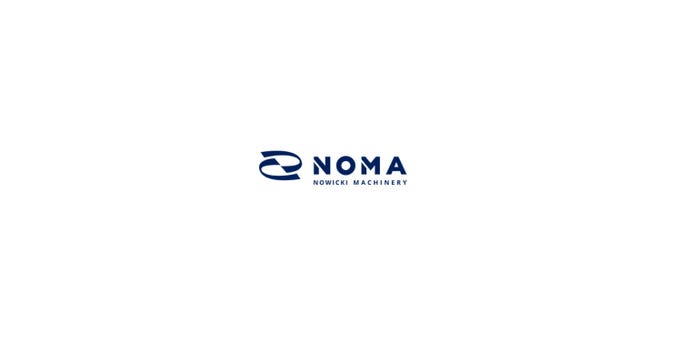
Mixers & Blenders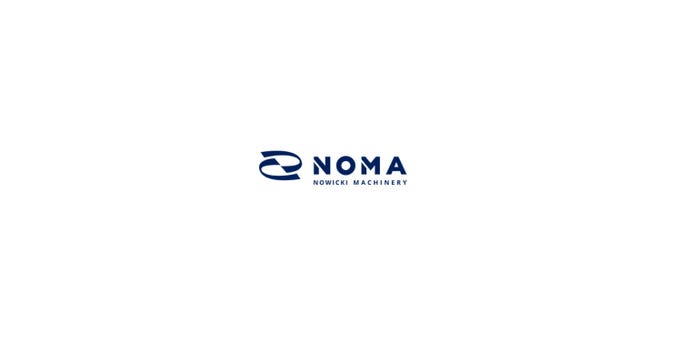
Nowicki Food Machinery Renames to NOMANowicki Food Machinery Renames to NOMA
The name is a combination of "Nowicki" and "Machinery."
Sign up for the Powder & Bulk Solids Weekly newsletter.