Practical Uses of Metal Detectors for In-Flight Applications
October 11, 2012
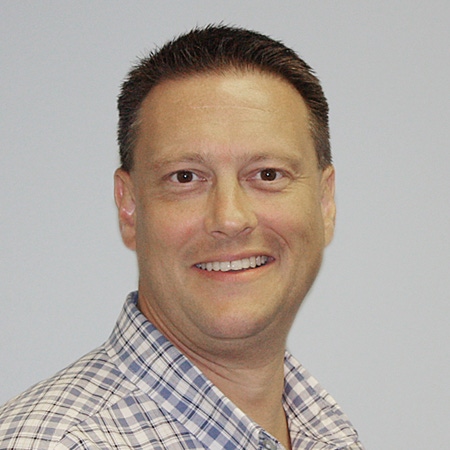
Most of us are familiar with common uses of magnets and metal detectors for gravity free fall of loose product, or inspection of finished bags and boxes. As the needs of industry have changed over time, so has the application of metal detection equipment in a processing environment. The use of pressure or vacuum to transport materials, whether bringing materials into a building, or loading them out, has now given us other locations to utilize modern separation techniques.
With improvements to metal detection in the last few years, reliable detection and rejection of contaminated product flow is easily achieved. However, the location and use of metal detection inside the processing plant requires special attention.
First, let’s start with a little information about the basic construction of the metal detector coil (sometimes referred to as the search head). Modern, electronic detectors utilize triple coil technology. Wrapped around the aperture opening are three coils. The center winding is the transmitter. There are two other coils, one at each end of the head. An electromagnetic (EMF) field is created inside the opening of the head. Items passing through the search head that are either magnetic permeable, or conductive, disrupt the field and create a signal with each receiver. Modern electronics and software are able to capture these readings in milliseconds of time and compare the readings at each receiver point. The computer processor decides if the signal is metal, or not. A reject mechanism further downstream is activated to divert the product flow into a contamination bin or some other catch point.
The distinct advantages to triple coil technology is that the unit is able to determine the velocity of the contamination by measuring the amount of time between signals, and knowing the space between the two receivers. The downstream reject device is then able to actuate at a more precise time the contamination will be approaching the diverter. This allows for the end user to not reject as much good material in the product stream along with the metal contamination.
As you apply this equipment in your process, it is important that you understand how fast the material is traveling in the line. The location of the reject device needs to be far enough away from the search head, that the flap has time to open before the metal arrives. Most flap rejects activate close-open-close within a second. For larger line sizes where a flap is not practical, you can use a slide gate. These typically actuate much slower, and need to be placed further downstream. If the material velocity is too quick, and the gate is too slow, it is possible that you run out of room to install a reject. Again, it is important to know the velocity of the process flow.
Another critical installation aspect is whether you are inspecting and rejecting in a horizontal plane, or doing this with a vertical installation. Whether you are conveying in a constant or intermittent process, a vertical system has a higher level of successful rejection in the event of contamination.
If you are conveying on a horizontal plane, there exists the possibility that the metal is correctly detected in the search head, but then does not reach the reject device while the flap is open. A potential cause of this would be if the system loses pressure or shuts down for some reason. If the unit is oriented in a vertical installation, and the system shuts down, the particles will fall. When the system resumes, the particles have to pass through the search head a second time, thereby ensuring successful reject.
A final consideration when looking to install in-flight detection is to know if the area is considered a hazardous zone. In recent years the efforts of regulatory agencies has been to classify most of these environments as a dust hazard. It is the end users responsibility to evaluate their circumstances and determine the appropriate level of hazard. The detector can then be built to meet that standard, whether it is NEC or ATEX rated.
Rod Henricks is product manager – metal detection, Bunting Magnetics Co., a world leader in the manufacture of permanent magnetic separation equipment for the processing industry.
You May Also Like