Combustion Optimization in Direct Combustion Biomass Energy Production
May 23, 2016
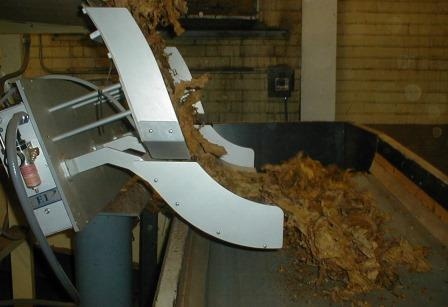
Amidst ongoing concerns regarding energy independence, the volatile costs of fossil fuels and concerns over the environmental impact of our current state of energy production and consumption, the interest in and reliance on bio-energy as a renewable energy source has exponentially increased over the past few decades. As this burgeoning industry blossoms, the concepts and techniques that were initially implemented only in pilot plants and test facilities, are now being broadened to encompass full-scale generation facilities. As this transition occurs, the desire for efficiency and cost-effective methods of energy production grows, especially as fossil fuel costs have dipped over the last few years.
A common method of producing bio-energy is the direct combustion technique, whereby a variety of feed stocks are burned to produce heat for steam, which in turn, drives turbines, thus creating energy. One of the simplest and most cost-effective ways of optimizing a direct combustion system – that is increasing efficiency and cost effectiveness - is to optimize the combustion cycle itself. That means accurately measuring both components of the combustion phase, which includes the feed stock as well as the air itself. What then, are the requirements for an accurate feedstock measurement and an accurate air flow measurement?
Requirements for Measuring the Feedstock
Many feedstocks in direct combustion bio-energy production are by-products, residues, or even waste generated by another production process. These feedstocks can be extremely diverse, ranging from wood chips or pellets to crop waste and even construction debris. Due to the fact that many of these feedstocks are by-products of other processes, the cost of obtaining them is relatively small. Sometimes, they can even be free. The cost of these feedstocks, then, or rather their lack of cost, can make it difficult to justify the addition of a measurement device to measure them. The true cost of these feedstocks, however, cannot be calculated by how much it costs to obtain the raw feedstock. Rather, the true cost of the feedstock should reflect how proficiently they can be processed, how effectively and completely they are combusted, and how efficiently they are turned into useable power. An accurate flow measurement is part of this equation and can assist in harnessing the true “power” within the feedstock by optimizing the combustion process and ensuring a consistent ratio of the feedstock to the combustion air. Furthermore, boilers, just like most other pieces of equipment, work best when a particular rate of feedstock is introduced into the combustion cycle. A proper flow measurement can help to maintain that rate. The result will be less waste (less unburned or partially burned material), which means less disposal of unused materials. It also means optimized heat production which streamlines the energy production and reduces the cost of producing each kWatt of power.
Ironically, the very thing that makes many of these feedstocks inexpensive to obtain is the same thing that makes them difficult to accurately measure. Their status as by-products means that little time or attention has been paid to their physical properties and thus, they are often irregularly shaped and may vary quite significantly in terms of particle size, shape, and even density. Another key attribute of many of these types of products is their relatively light bulk density. Many of these products can have bulk densities well under 10 lb/cu ft. This irregularity in particle makeup, as well as the relatively light bulk density, makes these products difficult to accurately measure, especially for any flow measurement that would assume as constants, parameters such as particle size, shape, or density.
One extremely accurate way of measuring these materials without assuming particle size, shape, or density is to utilize a gravimetric measurement. Static or load cell-based measurement devices such as static weigh scales or bins/silos on load cells can be very accurate. However, load cell-based measurement requires that the process be stopped in order to take a discrete weighment of the feedstock. While they can be quite accurate, the optimization that comes from a continuous process is simply impossible with a static, load cell-based measurement. The ideal meter for measuring the feedstock in any biomass combustion operation would retain the high accuracy of a static or load cell-based measurement system that measures gravimetrically and thus, independently of particle size, shape, and especially density. Such a meter would ensure that its accuracy would not degrade as the feedstock’s moisture content varied over time or if its density was extremely low. Moreover, the ideal flow meter should be able to measure feedstock in process, as product flows through it continuously, so that the combustion cycle never needs to wait on additional feedstock.
Requirements for Measuring Air Flow
As important as it is to accurately measure the feedstock that is being combusted, it is equally important to measure combustion air since a proper air flow measurement is integral to the airflow control loop, which aids in controlling the efficiency of the combustion process. “Combustion efficiency” it is said, “depends primarily on good contact between the oxygen in the air and the biomass fuel.”2 It is important then, to not only ensure that the mass of air is stochiometrically ratioed with the mass of the feedstock, but also, that the air stream needs to be properly presented to the fuel to ensure that proper contact is made and maintained during ignition.
As measurement devices for measuring air flow, pitot tubes are a time-tested and economical method that are as simple to install as placing them within the air stream. Most pitots work by measuring the differential pressure or velocity pressure of the air that passes across the profile of the pitot. The differential pressure created across the profile of the pitot is proportional to the mass flow as long as absolute pressure and temperature are also being measured and included within the mass flow calculation. This is typically accomplished by utilizing a multivariable transmitter along with your pitot array.
Pitot technology is extremely accurate as long as the air is smooth and there is little turbulence within the air stream. Unfortunately, the air within the ducts of power plants is often extremely turbulent. This turbulence can include both swirl and poor profile. Swirl occurs -especially in round ducts - as air travels around the circumference of the duct, swirling as it travels through the duct work. A poor profile occurs after some sort of disturbance (bends, tees, duct obstruction, etc.) where the air may be hugging one of the duct walls and is not evenly distributed across the duct. Typically, air flow elements such as insertion pitots require at least five diameters of straight duct run after a bend and 10 or more diameters after a fan in order for the flow to become smooth enough that swirl and a poor profile will have a limited effect on the accuracy of the flow measurement1. In many power plants, these types of straight duct runs simply do not exist.
In order to minimize the straight runs required for accurate measurement, different types of flow conditioners are used in order to eliminate the turbulence prior to measurement. Flow straighteners, for example, are typically used to straighten the flow and eliminate the effects of cyclonic flow. Flow straighteners like honeycombs work well to eliminate cyclonic flow or swirl, but they are not able to properly profile the air, meaning that the air will not be evenly distributed across the entire duct. If only part of the duct is seeing flow, any measurement within this turbulent air may misinterpret the flow or may miss the flow entirely. Furthermore, flow straighteners may utilize a collection of small openings or cells in order to straighten the air. These small cells also serve to reduce the amount of air that can pass through the duct, meaning that the fan used to push the air through the ducts may have to work even harder to maintain a consistent amount of air. While flow straighteners are good at straightening flow and eliminating swirl, flow profilers are good at profiling flow. Quite often venturis are used for profiling air flow. Venturis work by nozzling the flow to a smaller diameter which profiles the flow quite well. With nothing to eliminate swirl, however, flow profilers are unable to eliminate the swirling effect of air and the negative effects that swirl has on the accuracy of flow measurement devices.
The answer then is a flow measurement device that consists of an array of insertion pitots that is combined with a flow conditioning device, one that eliminates swirl like a flow striaghtener and is able to profile the air like a flow profiler. These flow conditioners properly condition the flow prior to measurement so that the air is smooth and near-turbulence free at the point of measurement. In some instances, flow conditioners can be installed directly after fans and can still maintain an extremely accurate measurement because they are able to condition the flow properly prior to measurement. Many of these devices offer reduced pressure loss that is never more than 30% of the generated differential pressure. Moreover, the benefit of measurement devices that condition the flow, especially in combustion applications, is precisely that the air is conditioned as it exits the flow conditioning element. Properly profiled air takes the guesswork out of presenting the air to the fuel, ensuring that proper contact between the air and the feed stock is maintained. Because the air is presented consistently, the presentation of the feedstock can easily be controlled and optimized.
Summary
When utilized in concert, accurate air flow and accurate solids flow measurement combine to offer greater control over the combustion process. This control maximizes the efficiency of the boilers, which will in turn maximize the combustion potential of your feedstock, allowing you to extract the maximum energy from it. Optimizing the combustion process will also aid in reducing buildup and residue on the boiler tubes because the combustion will itself be cleaner and more efficient, thus reducing the need for costly cleaning and maintenance. Cleaner combustion will also result in fewer emissions, due to a cleaner and more efficient combustion, so that scrubbers and other injection systems often used to counteract harmful emissions can be reduced or even eliminated. The net result of optimized combustion is increased efficiency which translates into a less costly and more profitable process.
Christopher Lewis has been with Eastern Instruments, Wilmington, NC, since 2008. For more information, visit www.easterninstruments.com.
References
1. ASTM D3154 Standard Test Method for Averaging Velocity in a Duct (Pitot Tube Method), ASTM Standard Section 8.5, 8.6, 8.7. 2014.
2. Zafar, Salman. Summary of Biomass Combustion Technologies. BioEnergy Consult www.bioenergyconsult.com, January, 2016.
You May Also Like