Screw Conveyor with Metal Detection Transfers Plastic Chips
March 27, 2012
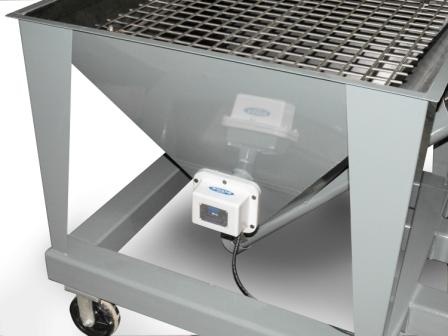
A major Michigan plastics recycling company required a conveyor to automatically transport plastic chips from a grinder feeding a cyclone to a Gaylord box without operator intervention. In addition to conveying the plastic chips the company needed to detect and remove stainless steel, brass, mild steel, aluminum, copper, and other metal contaminates from the stream of material exiting the conveyor discharge before filling the Gaylord container.
Another challenge was to make the entire unit portable, quick, and safe to setup so that the conveyor and metal detector combination could be used at different locations within the plant to minimize the initial capital investment and provide a quick return on investment for economic justification.
The solution required extensive testing in the laboratory to determine the proper conveyor parameters including size, auger type, rotational speed, and the ideal auger to casing clearance to provide a conveyor with minimal maintenance requirements. One of the initial challenges to overcome was that the plastic chips were irregularly shaped, with sizes ranging from 1/8 to ¾ inch, a bulk density of 30 lb/cu ft, and a 45 degree angle of repose. The overall capacity varied from 1000 to 1600 lb/hr or volumetrically from 33.3 to 45.7 cu ft/hr. Based upon empirical testing, a 3.5-in .OD x 3-in. ID UHMW-PE (ultra-high molecular weight polyethylene plastic) outer casing with a ¼-in.-thick wall was determined to be an ideal size. Due to the large size and irregular shape of the plastic chips, a round wire auger profile with 2 ¼-in. outer diameter was selected and provided a total auger to casing clearance of ¾ in., which eliminated any binding especially at the inlet boot assembly. Another critical factor in obtaining a smooth flow in the conveyor is the auger speed. Therefore by utilizing a variable speed controller a maximum rotational speed of 350 RPM provided for a vibration-free and quiet running conveyor yet was able to obtain the required throughput.
As seen in the photograph, the conveying system was designed with a 3-in. heavy wall portable frame, removable drive motor mast assembly, painted carbon steel construction in conjunction with industrial quality 6-in.-diam polyurethane wheels (two fixed and two swivel with locking brakes) to make maneuvering within the plant from one grinder location to another a one person job. In addition, the conveyor includes a NEMA 4 control panel that operates all functions of the system including the conveyor drive motor (220-volt, single-phase, 60 Hertz input), inlet low level sensor, metal detector on/off switch, and hinged safety grate with drive motor interlock. The electrical control panel has an on pilot light, main disconnect, fusing, on/off push buttons, and E-stop. To setup the conveyor, the operator moves the portable frame so that the inlet hopper is positioned under the grinder cyclone discharge, moves a Gaylord container under the metal detector discharge, and plugs a 220-volt, single-phase, 60-hertz plug into a nearby electrical outlet.
To make this operation automatic, a cycle timer was used to control the inlet low level sensor. When the conveyor is initially turned on there is no material in the inlet hopper and, therefore, the low level sensor doesn’t allow the conveyor to start. This protects the conveyor from running dry without material. As soon as the grinder cyclone starts to discharge material, the level sensor detects material based upon a programmable cycle timer and the conveyor will start running and will continue to run until the inlet low level sensor doesn’t detect material in the hopper. This cycle continues without operator intervention until a new Gaylord container is required. The current Gaylord is removed, a new Gaylord is inserted, and the process continues without interruption allowing the operator to be more productive.
The plastic chips are discharged from the conveyor through a metal detector that incorporates a pneumatically actuated diverter valve. Therefore, when metal is detected the diverter valve discharges the metal along with a small amount of the plastic chips into a reject container. Only a clean stream of material goes directly into the Gaylord for further processing.
In addition to metal detectors, magnets can also be incorporated into the conveyor design to easily remove tramp metal from the product stream. However, this doesn’t remove non-magnetic materials, such as stainless steel, copper, aluminum, brass, etc. A metal detector is required for the latter.
Tech3 Manufacturing Co. (Kalamazoo, MI) builds standard and custom-designed flexible screw conveyors to customer requirements, from 2.5 to 8 in. in diameter and up to 40 ft long. It also manufactures a range of replacement augers and casings for all flexible screw conveyor makes and models. For more information, call 269-375-4469 or visit www.tech3mfg.com.
You May Also Like