Articulated Loader Reduces Barge-Loading Times and Costs
September 27, 2012
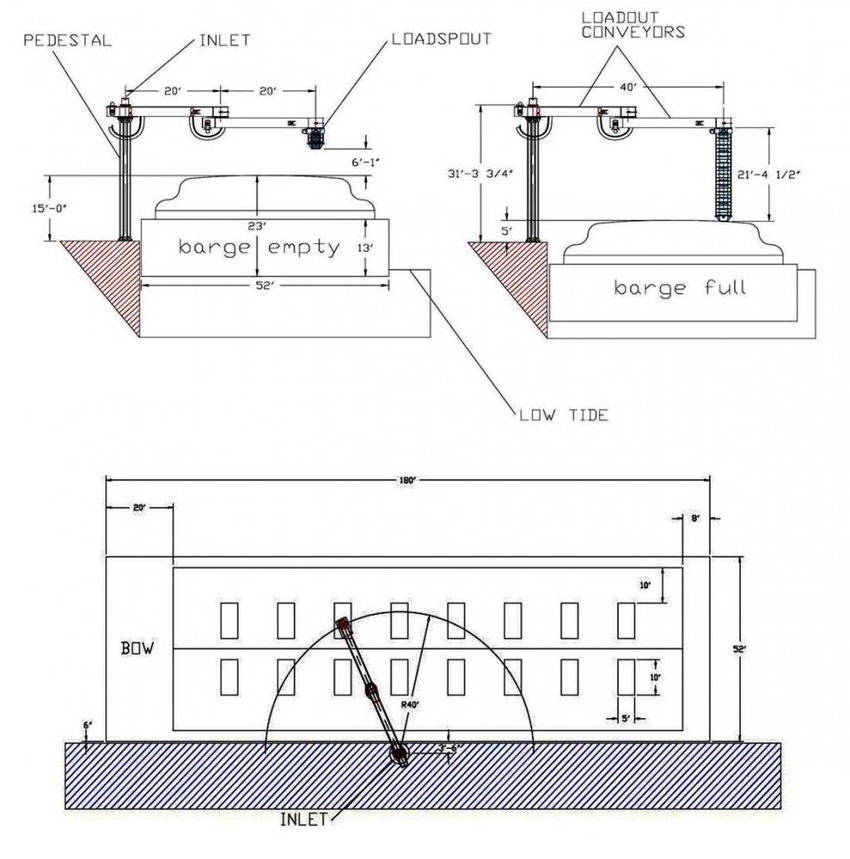
DYNATEK has released a new articulated loader design that can improve the efficiency with which 180 X 52-ft, 16-hatch hopper barges can be loaded with dry solids. Using a traditional barge-loading system, it is common for the loading process to require as many as nine barge position changes and a tug-based, 180-degree barge rotation to access all infeed hatches and fully load the barge. All of the position changes and time that can be spent waiting for a tug to arrive and rotate the barge can easily reduce loading rates to less than one barge per day.
DYNATEK’s solution was to design an articulated dual–arm, loading system that featured a 40-ft reach radius and a rotational range of up to 330 degrees. Using drag or belt conveyor technology and this loading system design, a 180 X 52-ft, 16-hatch hopper barge can be fully loaded without the use of a tug at all, and with only two winch-based position changes. At a loading rate of 25,000 cu ft/hr, a barge can be loaded in seven hours versus a day or more. Fewer barge position changes and shorter loading times reduces loading costs and enhances loading process safety overall.
DYNATEK Articulated Loading Systems, a division of D&D Products, designs and builds articulated truck-, railcar-, and barge-loading systems based on auger, belt, drag, and air slide conveyor technologies.
DYNATEK Articulated Loading Systems, North Prairie, WI 888-853-5444 www.dynatekloadingsystems.com
You May Also Like