Vac-U-Max, GEMCO, Vorti-Siv Unveil AM Metal Powder Recovery & Reconditioning System
The new system reclaims, reclassifies, reconditions, and reduces time and unsafe operating conditions.
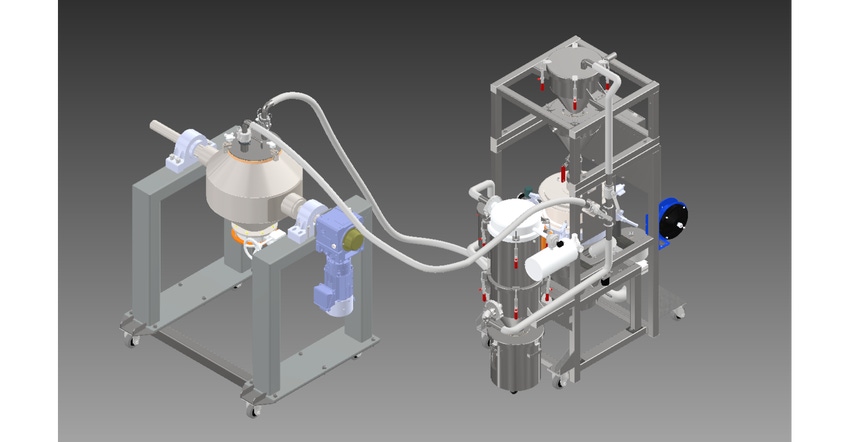
Vac-U-Max, GEMCO, and Vorti-Siv announce the collaborative development of the AM-MPRR, a new system designed for effective 3D printing of metal powders. This system manages the entire lifecycle of metal powders for powder bed laser fusion and binder jet printing, including unloading, handling, reclamation, and reconditioning.
Advanced Vacuum Technology
The new system utilizes advanced vacuum technology to fully extract metal powders from the printing bed, while removing unused metal powder and reconditioning it for future use, revolutionizing metal powder reuse. It reclaims unused powders from the printing bed in 85% less time than traditional methods, reconditioning them for reuse. AM-MPRR seamlessly integrates with GEMCO’s mixing and drying technology. This allows users to efficiently reclaim and recondition unused metal powders from the printing process and extend their useful life. Overall, this system leads to waste reduction, material usage optimization, and cost savings – all while maintaining the high-performance standards required for critical AM applications.
“Experience is not an experiment,” said Doan Pendleton, president of Vac-U-Max. “There is no need to reinvent the proverbial wheel for metal powder handling needs. The MPRR family of products comes with experience as a standard feature, from a team of companies including GEMCO and Vorti-Siv that have supported additive manufacturing and 3D printing since its early days.”
The commitment to innovation extends beyond the AM-MPRR project for all three companies. Highlighting the collaborative nature of the AM-MPRR, Casey Bickhardt, president/CEO/owner of GEMCO, said, "We are firmly committed to advancing the entire additive manufacturing industry. This new, joint AM-MPRR effort perfectly embodies that spirit."
This commitment is further exemplified by GEMCO's recent membership of the National Institute of Standards and Technology's (NIST) Metal Additive Manufacturing Powder Consortium.
Listening to customers’ needs and drawing on their extensive powder handling experiences has resulted in an equipment package that addresses key requirements of laser powder bed fusion and binder jet printing operations.
Reclaim: Removing unused metal powder safely and productively from the build box with a proven vacuum conveyor. The vacuum conveyor module also direct-charge loads the tumble blender in a safe and productive way. A sustainable and safe benefit.
Reclassify: Depositing the collected metal powders onto a vibratory sieve to remove oversized particles or foreign debris. A high-quality benefit. The sieve incorporates an ultrasonic screen anti-blinding device for non-stop operation.
Recondition: Residual identical powder from multiple printers can be delivered to the tumble blender module to be homogenized into a consistent masterbatch for reuse. Another version of the MPRR not only blends the powder effectively but dries it to a single-digit moisture content to improve the powder flowability. Longer time before returning the powder for remelting and re-atomizing. A bottom-line benefit.
Reduce Time: Traditional 3D printing workflows can be hampered by the time-consuming powder handling required for each build. The MPRR system addresses this challenge by offering a combined solution for productive vacuum removal and simultaneous sieving of powders. This translates to a significant 85% reduction in downtime, leading to substantial gains in overall printing efficiency.
Reduce Unsafe Conditions: All MPRR products are designed to process reactive and non-reactive metal powders in accordance with NFPA and UL standards in a plug-and-play design. The MPRR products deliver reconditioned metal powders that are ready for use in demanding high-spec printing operations. Other benefits include improved ergonomics for operators, safe material handling, and reduced spillage from manual handling of small powder containers or manual sieving. The portable design is easy to maneuver around print rooms.
AM-MPRR products are easily serviced with their uncluttered design and the ability to have screens pretensioned and re-meshed by the manufacturer at a lower cost than new.
Vac-U-Max, Belleville, NJ 973-388-2423 www.vac-u-max.com
About the Author(s)
You May Also Like