Using Indicator Technology to Improve Process Efficiency, Profitability
July 6, 2012
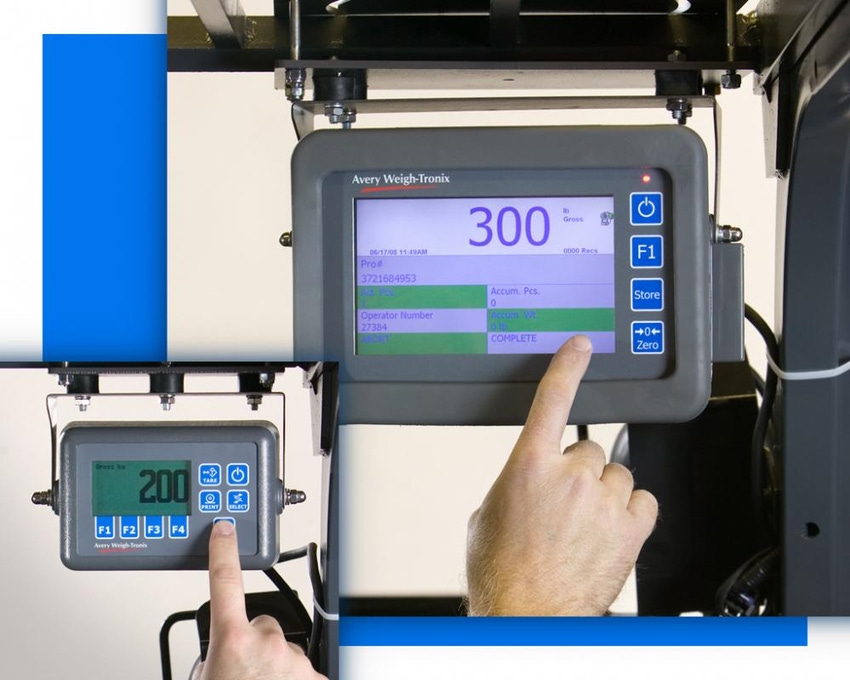
Precise weight measurements are critical in material handling operations as they directly impact many aspects of production, from inventory accuracy to customer satisfaction and overall profitability. To achieve the necessary weighment precision, indicators are an essential component of scale systems. Today’s highly-intelligent, digital weight and scale indicators are designed for virtually any weighing application, significantly improving weighing operations, increasing the visibility of data and enhancing production efficiency.
Indicators range from simplistic, entry-level models to sophisticated options with connectivity capabilities that support a wide variety of industry-standard interfaces like Ethernet and DeviceNet. With advanced features and performance options, indicators can easily integrate into existing networks, saving valuable time and the expense on costly system upgrades to support future production modifications and adaptations as they arise.
Controlling activities from data management to process control and quality assurance, indicators are much more than just a device that displays weight measurements. By understanding recent advancements and current performance capabilities associated with indicator technology, as well as the impact these innovations can have on overall production, operators can select the ideal indicator solution that will adapt and evolve with process needs to increase productivity and profitability.
Indicator Technology
A simple definition for a scale indicator describes it as a device that allows the operator to read the weight and control the scale. Today’s indicators have expanded beyond these basic principles and can now function as a “behind-the-scenes” process management tool. Indicators still obtain weighments that can be stored and recalled when necessary, but they also provide connectivity capabilities that allow the indicator to communicate with plant devices and computers to further automate production.
As an intuitive weighing solution, indicators feature simplistic programming functions, allowing users to customize performance to meet specific needs. They also deliver consistent, reliable readings with highly visible displays that allow indicators to be viewed in a variety of lighting situations, such as dim lighting conditions, direct sunlight, or reflected light.
Presenting rapid response times, flexible input/output options, and multiple units of measurement, indicators can adapt to fast-paced environments, providing the accuracy and versatility necessary for a wide variety of material handling applications. Further, indicators ensure loads meet strict legal-for-trade weights, as well as demonstrate that each load contains the exact amount of materials it is purported to have, eliminating under or overvalued packages. Indicators with networking capabilities can effortlessly integrate with plant devices to easy collect and convey critical data. Plus, for additional flexibility, indicators offer internal battery power for mobile applications and provide a serial interface for printer or PC connectivity.
Engineered for durability and versatility, indicators are available in multiple housing options, such as aluminum and stainless steel, with mounting flexibility that enables them to adapt to diverse situations. For instance, panel mount enclosures provide protection against dusty or wet environments. Additionally, indicators featuring IP ratings, such as IP69K, can withstand harsh environmental conditions. IP69K-rated indicators are for applications where high-pressure and high-temperature washdown is used for equipment sanitation to provide superior protection against the ingress of water and particles that can contaminate the device.
Indicator Capabilities that Improve Process Performance
In order to increase automation and efficiency in diverse material handling processes, indicators have become faster, smarter, and more versatile—dramatically impacting productivity. Indicators possess the power, flexibility and speed to achieve the most advanced performance capabilities in weight measurement, process control and effective communication.
Communication networks are critical components of modern manufacturing and processing facilities, therefore, implementing indicator solutions that fully integrate with existing plant systems provide a scale system that is accessible from any computer for remote analysis of real-time data, system configuration, and diagnostics. Additionally, employing multiple information systems, indicators can deliver maximum flexibility by monitoring operations and performing data acquisition via a web browser. This provides users with immediate operational updates via e-mail as well as unaltered data transmission via FTP.
Additional indicator features include simultaneous display of multiple scales, user-configured displays, direct process control, network communications and programmable softkeys. They are designed to function in fully-integrated environments, with options to communicate over the widest range of network protocols. Equipped with a variety of standard and optional connectivity interfaces, indicators offer seamless compatibility and communication with previous and new peripheral technologies. With this sophisticated connectivity, indicators can be programmed to measure, monitor and control virtually any weight-based operation.
Along with monitoring all connected scales, sensors, and control devices, indicators can also perform maintenance on their own internal systems. Any faults or errors initiate “Operational Warnings” that are clearly spelled out on the indicator display, and if the indicator is connected to a fieldbus, detailed descriptions of functional issues can be viewed at any access point along the network. E-mail messages can also be sent directly to designated personnel both on and off-site—minimizing downtime. Further, error reporting and programmed response are system specific, which means that problems occurring within one system will not interrupt the operation of other scales or processes controlled by the indicator. To ensure continued operation as soon as possible and to prevent the loss of valuable data, indicators maintain downloadable system logs containing a detailed record of overloads, underloads and traffic counts.
For operations that require users to manage multiple scale systems, indicators can store multiple TAREs and IDs in their internal memory, providing easy retrieval for future use.
Featuring clearly-displayed buttons for common weighing requirements, such as counting, checkweighing and process control, the same indicator can be used for multiple applications. Plus, to easily monitor multiple scales and operations, multi-segmented graphs provide detailed information regarding product inventory, production status and cumulative weight data at a glance.
Indicators In Action
Chemical processing and food manufacturing plants often require precision mixing and batching of multiple components to achieve the desired end product. This requires exact measurements, as incorrect mixtures can lead to poor customer satisfaction, or in the case of pharmaceuticals, improper ingredient quotients can be dangerous to users. Therefore, utilizing an indicator that can automatically recall recipes and ensure exact product distribution enhances productivity and product quality.
Indicators can easily receive weight data from load cells attached to vessels (tanks), floor scales, bench scales, or conveyors, allowing them to command PLCs to control and manage ingredient flow. This increases process efficiency and accuracy. Batch mode configurations include manual, automatic, filling, reverse filling, and continuous. Some indicators even have features that allow them to improve automatic batching applications by compensating for weight of product in free fall and compare the amount of deviation to piece or ingredient weights stored in memory to pinpoint any missing elements, improving the accuracy of the next batch
Additionally, for applications that require users to monitor and manage the movement of large quantities of materials on a daily basis, such as with recycling facilities, indicators can track and store data about each load, improving inventory management and increasing revenue. By interfacing these indicators with forklift trucks and floor scales, recycling centers have a fully-programmable scale system, with indicators that can record ID numbers, load and accumulated weights, as well as customized data for management information and control. Further, these indicators can be linked to printers, bar code scanners, computers, and other peripherals for integration into existing networks, allowing effortless data transfer and management from anywhere in the facility.
The Future of Weighing Technology
With today’s fierce market competition, ensuring customer satisfaction without impacting productivity is crucial. Now, operators can implement indicator solutions with customizable features and functions in order to tailor their performance to exact application specifications. This not only improves production with data acquisition and inventory management capabilities, but also improves a company’s bottom line and product quality.
Don Halbert is global product manager at Avery Weigh-Tronix (Fairmont, MN). He has more than 33 years of expertise in the provision of weighing equipment and solutions. Halbert focuses on the need for weight-based data collection in a variety of industries (warehousing, recycling, transportation, waste, food and beverage) providing product management for market solutions while staying abreast of emerging technologies and industry trends. For more information, call 877-888-1646 or visit www.wtxweb.com.
You May Also Like