Solids Level Detection Using High-Power Technology
October 25, 2012
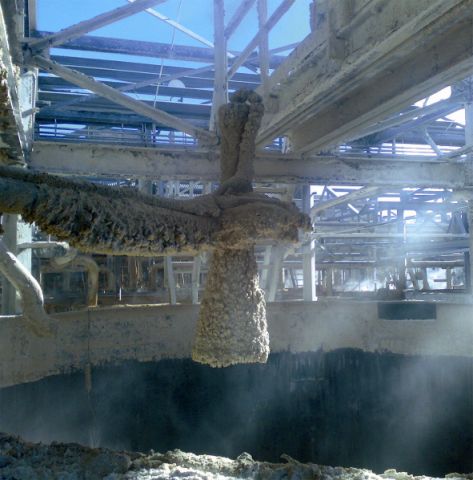
How many more technologies will emerge in the world market for measuring continuous level for solids? With all of the level technologies available, it is becoming difficult to make a wise selection of which one will provide the best results. Many factors are involved in deciding which technology is best suited for a level application, not to mention the cost, installation time, and the learning curve involved for the technology chosen.
Comparison between Acoustic Wave and Microwave Technology
Microwave Technology
If there isn't a universal technology for measuring level in liquids or solids, why is microwave radar being sold into a large majority of level applications? It is being falsely promoted as the solution to almost every application, and has claims that it can perform under all conditions of duress. These conditions are heavy dust in the airspace, heavy build-up on the antenna emitter, wet and moist conditions, the ability to read through foam, high temperatures. One can visit a plant site and see microwave radar designs installed in applications where they should not have been used. With microwave radar technology, like any other technology in the marketplace, there are advantages and limitations for its applicability and performance success. Microwave radar is not the ultimate solution for all level applications.
Acoustic Wave Technology
Not to be mistaken with ultrasonic wave, acoustic wave technology uses low-frequency design harnessed within a short cylindrical, but narrow diameter transducer package. Different than any other technology on the market today, this unique design drives the low-frequency resonating mass to produce a pressure wave at the face of the transducer. With this pulsing to the face of the sensor, there is a self-cleaning effect that eliminates any type of build-up. So, low-frequency (5 to 30 KHz) combined with high power provides measurement capability in the toughest of applications. There are technologies and there are application conditions, and the two items have to be considered together. Many companies make the mistake of trying to fit one technology into numerous applications that do not work well. Understand the applications parameters, as well as the customer’s requirements, and then discuss the technology for the measurement.
When the application involves the measurement of solids materials, like powders, grains, metal ores like copper, iron, coal, and cement materials, then applying the right technology takes additional thought. From a microwave wave radar perspective, the technology was introduced into the solids level market in the 2003 timeframe, and was promoted as being the new technology for measurement in all solids applications. However, this technology was not accepted universally.
The technology warrants merit as it is a solution-oriented design, but when it comes to solids and the addition of moisture into any application, there are no self-cleaning properties like acoustic wave. With the measurement of solids, it must be emphasized that there are industries that have dry solids, and then applications that have moisture. When one speaks about the mining industry (coal, non-ferrous, and ferrous minerals), reducing the heavy dust in the environment through the use of water sprayers is an absolute necessity for the work force. There is so much excessive dust throughout a mining site because raw rock and ore material is transported to machinery that performs crushing, movement via conveyor belts, dropping from one transfer chute or another, and is a dust nightmare. So most mining operations today will make use of water in a spray form that is located at filter screens, ROM bins, rock crushers, conveyor transport, and many more. With powder and water mist combined, the parts of any containment, conveyor belts, transfer chutes, and such, will be coated with heavy scaling or build-up. So for level measurement and the notion to keep things clean so that performance can continue, either there has to be lots of periodic maintenance to keep the sensing elements clear of coating or the technology must have that feature built in. Acoustic wave technology has the built in capability to keep the propagating sensor surface free of coating or build-up regardless of the material being wet or dry.
The magic behind acoustic wave technology is not just the frequency, as it is a combination of low frequency, like 20 to 5 KHz, along with high power to a narrow diameter balanced resonating mass, and adaptive modulating gain control. Actually, the secret is in the formula for all three of these variables, which is mechanical transducer design, power & energy distribution, and adaptive software control. In the solids industry and level measurement, it isn't just software that will yield the successful results for these harsh application conditions.
When applying acoustic wave technology, the choice of the transducer frequency is not based upon the range of the measurement, but it is a function of what's in the containment. With low-frequency, high-power acoustic wave, it's more about the environment inside the containment. If there is moisture, then the frequency will need to be lowered, and accordingly, the power to move that larger resonating mass is taken into account. With lower frequency, the energy to the transducer is not increased, but distributed differently so that there is focus out into the airspace and not elsewhere. The acoustic technology is not affected by moisture content from an operational standpoint compared to microwave radar. Remember that microwave radar is a function of the dielectric value of the material.
Features of Acoustic Wave Technology
In addition to the self-cleaning properties for clean signal propagation on acoustic wave in wet, moist dusty environments, it is important to discuss the other noted features that allow this technology to stand out, including:
• The low frequency combined with the high energy allows this design to be used in solids applications without the typical aiming assembly for dealing with angles of repose. Enough focused energy is produced from the transducer face, and then a focalizer is used to harness the energy so that signal reflection back from the material surface is collected.
• Inherent false echoes and excessive ringing will occur with traditional ultrasonic technology as most of the transducers are mounted onto flanges that contact metal containment structures. A simple acoustical coupling abatement flange is designed now to completely isolate the transducer and eliminate the ringing issues.
•Acoustic wave design is impervious to any crosstalk directly related to electrical noise (variable frequency drives, pumps, etc.) because the signal coming out of the transducers are digital RS485 in their output and not some small millivolt output. Additionally, with the balanced transducer design at the crystal array, any noise is also not a problem.
•Acoustic wave technology deals extremely well with low bulk density materials. The issue with low bulk density materials (lightweight powders that have a soft surface) is that energy from microwave devices will allow the energy to pass through the material, and provide a small amount of reflection back, but mostly propagate through the material and reflect off of the metal containment bottom. Obviously, this is not an accurate measurement. The acoustic wave technology will allow much of the signal to reflect back due to some design features, which makes it ideal for these applications.
Choosing the Right Technology for Your Application
Every technology for level measurement has its place in applications. The selection of the technology for solids must be reviewed carefully and all application conditions of dust, condensation, wet material, turbulence, mounting, surface conditions, temperature & pressure, and many more, have to be considered. One technology like microwave radar should not be considered the universal solution to all level measurement applications. As pointed out, there are other technology solutions that will fit more appropriately in an application, and one that has been lying quietly in the background like acoustic wave, especially for nasty solids materials, fits the conditions to provide optimum performance.
Applying the right level technology is an engineered process and should not be a commodity sale. A careful review of the application conditions as well as the customer’s requirements should be examined before just offering something that has been promoted as the ultimate solution. The right level solution will provide many years of good successful performance with a low cost of ownership.
Jerry Boisvert is a Level Measurement Expert with Hawk Measurement Systems (Middleton, MA). He can be reached at [email protected] or www.hawkmeasure.com.
You May Also Like