Understanding Process Weighing Technology
July 5, 2012
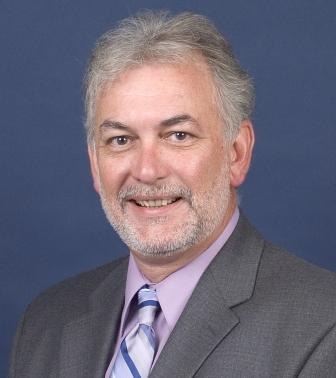
Weighing solutions in the process control industry have greatly evolved over time with the ever-expanding advancement in electronics and digital controls.
For many years, scales and weighing components were reliant upon mechanical levers and counterweights to achieve accurate product weights. Then, in the 70s and 80s came the introduction of the microprocessor and PC. Applying these technologies to the weighing industry greatly revolutionized the ability to weigh products, digitally control the entire process, and activate filling equipment and related components. All of these advancements in turn greatly increased productivity and time management in the weighing of products and manufacturing processes.
Today, there are two key components in weighing: the load cell and the weight indicator. The load cell is the integral part of sensing weight, and where the original point of weight is derived in a digital weighing environment. The weight indicator receives the signal from the load cell and converts it into a displayed weight that is visible to the eye and may additionally be stored on the indicator itself or related software and/or printed on a ticket.
The load cell is a precisely-engineered piece of metal that has micro-sized strain gauges strategically placed inside the body to sense the smallest amount of movement when force (weight) is applied to it. Depending on the vessel or container that is being weighed, it may require a single load cell or up to three or four load cells, placed in equal positions under the vessel. Some containers are suspended and, therefore, require special load cells designed to work within the suspension of the equipment. The weight indicator, in turn, receives and transmits electronic signals from the load cell. These electronic signals are ultimately translated into a readable weight measurement through a scale input circuit board inside the weight display.
The market for weight-based filling and product control is ever expanding. Whether bulk weighing the cereal we eat in the morning or the asphalt pavement on which we drive, everything from grains to aggregates have been weighed and monitored at some point during their production processes.
Weight-based display indicators have become very versatile in meeting almost any application. It's important to evaluate your weighing process completely when making a choice in the product you need to purchase. From a basic analog signal output going to only one device all the way up to reading multiple scales simultaneously, your choices are wide ranging and require research and understanding to make an informed selection. Flexibility in the ever-changing weighing process for industrial operations has become more user-friendly over time and with technological advancements. Many of the weight controllers on the market today are configurable and programmable to meet the exact process required for dispensing material and controlling relays for the purpose of activating conveyors or opening gate dumps. Depending on the complexity of your application, a scale distributor can work with the manufacturer of the scale to customize and design a product weighing application specifically just for you. In the world of weighing, one single device can now read multiple scales and manipulate several external devices to perform a complete production process.
In many cases, weight is required within your company's computer network for tracking products or applying dispensed weights to invoices. Many of the new digital weight indicators on the market include communication ports required for process control. Whether you require a basic serial connection to a PC or more advanced data transfer such as Ethernet EIP to your network, all of these connectivity options are available for getting weight to specific targeted locations. For example, you may require printing a weight ticket on site while also simultaneously sending this data to other networked locations within your company. This is all possible now through advances in weighing technology.
Choosing the correct scale and related weighing peripherals for your application can greatly enhance your productivity and economize your operations. It's important to review your complete weight based equipment and document what will be most important to you. Then, contact a local scale systems distributor to begin designing an application that is best suited for your process.
Having an accurate scale displaying reliable weight is important, but how you utilize that weight within your production process is most important in time and financial gains.
Fred Cox is vice president of sales, Cardinal Scale Manufacturing Co., Webb City, MO.
You May Also Like