Why Dry or Wet Milling?
While the need for size reduction is a common goal, the approach and selection of the method and equipment is driven by many other requirements.
March 15, 2024
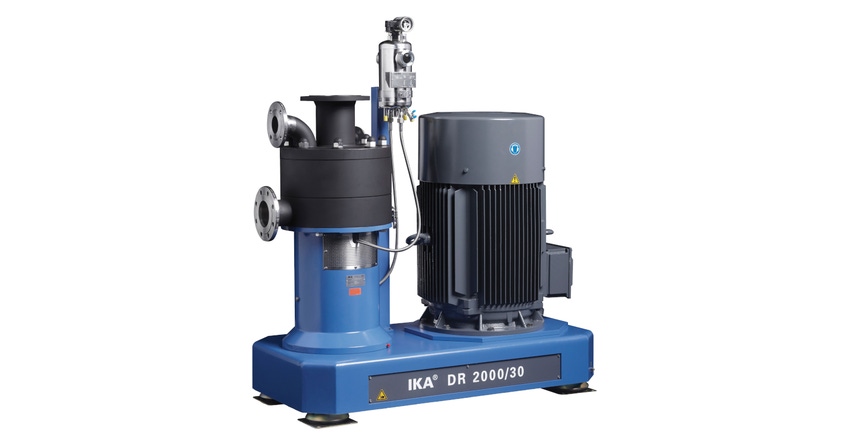
Accommodating material size reduction is a common necessity across most industries. Whether it be food, pharmaceutical, cosmetic, or chemical, the need for targeted particle size achievement arises for many different reasons. This can be related to anything ranging from pursuing a specific product mouth feel, pigment sizing and deagglomeration for coloring, creation of drug particles for time-released delivery, to increased surface area for driving reactions. While the need for size reduction is a common goal the approach and selection of the method and equipment is driven by many other requirements.
Two primary size reductions processes endure: dry and wet milling. Each approach contributes to methods of size reduction and creation relative to a form of energy, impact, shear, attrition, and compression. The basic principal of milling involves energy transfer through mechanical forces to create size reduction of a material by breaking it down progressively in to smaller and smaller pieces. Application of the appropriate milling technique varies relative to the conditions and/or environment.
Regardless of it being de-agglomeration or physical particle size reduction, targeted size reduction is not the only factor or requirement when milling. Even, narrow distribution of a focused size is of additional consideration. This means that size reduction of particles should fall uniformly withing a particular size range with minimal particles above or below that range (i.e. < 5µm @ d90) (see figure 1). In addition to narrow distribution, some applications also require specific shapes. For these and other reasons different methods of milling not only exist but are required.
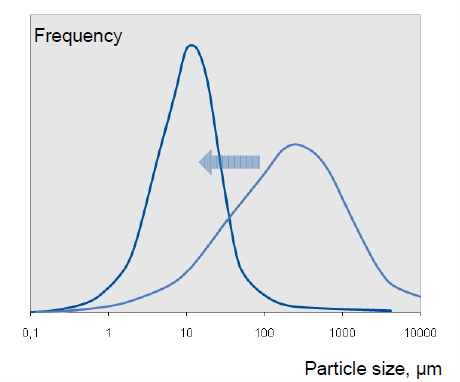
Figure 1: Particle size, µm (image courtesy of IKA Works)
Dry milling involves size reduction of material in a dry state. Function of a dry mill can produce high velocity collisions with other particles, against machine tooling, or create cutting, crushing, or grinding between tight tolerance mechanical surfaces.
Dry Milling Type Examples:
Hammer mills: Milling created by multiple repeated impact blows of small hammers within a chamber
Jet mills: Size reduction occurs relative to particle impact and collision with one another within a chamber as a result of high velocity produced with compressed air or inert gas.
Sieve mills: Uses a conical rotor to force material through a sieve of fine mesh in close tolerance for size reduction
Wet milling involves pumping a slurry through a grinding chamber in order to collide particles against one another or a solid surface. Hardness of the particle plays a key factor. The impact material surface must be harder than the particle itself to allow particle fracturing. Resulting force can be related to impact, griding, or crushing (to name a few).
Wet Milling Types:
Dissolver batch dispersers: High-speed toothed disc batch machine which pulverized solid agglomerates and particles with mechanical energy in a slurry under controlled conditions, creating size reduction.
Rotor/stator mills: Uses a liquid carrier to convey a slurry trough tooling--one stationery and one rotating at high speed--with progressive tooth slot openings for impact size reduction relative to velocity (see figure 2).
Media mill: Uses small media (beads) of different material or shapes under agitation, creating high velocity, reducing size of a solid slurry through impact and collision
Aspects of selecting a size reduction method are partly related to the proprieties of the material. Harder particles require impact, crushing, or grinding for size reduction. Materials of a fibrous nature are not susceptible to all of the same methods. They can resist some of these forces due to the elasticity and flexibility of the material. Therefore, the ability to cut, slice, or dice is required to create and produce smaller particles.
Process environments play an additional major part in either dry or wet milling selection and should also be considered. Processing temperature, dust accumulation, humidity, or even operator safety are all examples that can play a role. As an example, in the pharmaceutical industry wet milling is more desirable because dry milling can create surface defects related to the method. Wet milling provides the advantages of belter temperature control, filtration trough decantation, and lower yield losses (see figure 4). However, dry milling can be advantageous and effective for deagglomeration of dried crystallin active pharmaceutical ingredients (API).
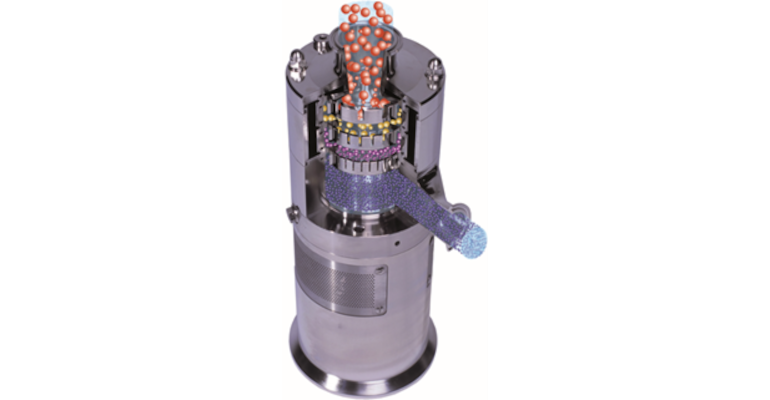
Figure 4: IKA Dispax Reactor DR interior cutaway (image courtesy of IKA Works)
Wet or dry milling have distinct advantages associated to a defined application and material condition. For instance, size reduction of hard particles on a rotor/stator wet milling process is related to impact. As the rotor/stator slots align material is conveyed through the openings via the liquid carrier and lift produced by centrifugal motion of the mill’s rotational speed. This motion creates velocity. Said velocity is abruptly disrupted when the partial impacts the stator tooth, creating fracturing (see figure 5). These same rotor/stator mills can provide the addition benefit of forming specific solid sizes from solution resulting from high energy impartation, derived from chemistry precipitation.
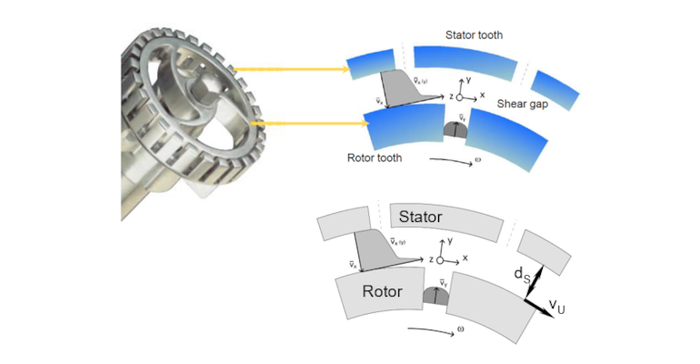
Figure 5: Rotor and stator shear effect (image courtesy of IKA Works)
Summary
Appropriate consideration of the milling conditions, goal, and environment is critical in specifying the correct method or approach for size reduction. With so many processing options to choose from the correct selection can a bit intimidating. Partnering with an experienced equipment manufacturer that specializes in a given technology can be immensely beneficial to expedite the selection process and insuring the correct method and equipment selection.
Lee Holliday is director of process, IKA Works (Wilmington, NC). For more information, call 910-452-7059 or visit www.ika.com/en.
About the Author(s)
You May Also Like