Innovative Waste Processing with Integrated Air Filtration System
The fusion of advanced waste processing technologies with the FS filtration system has improved operational efficiency and environmental performance for Huthmann.
February 21, 2024
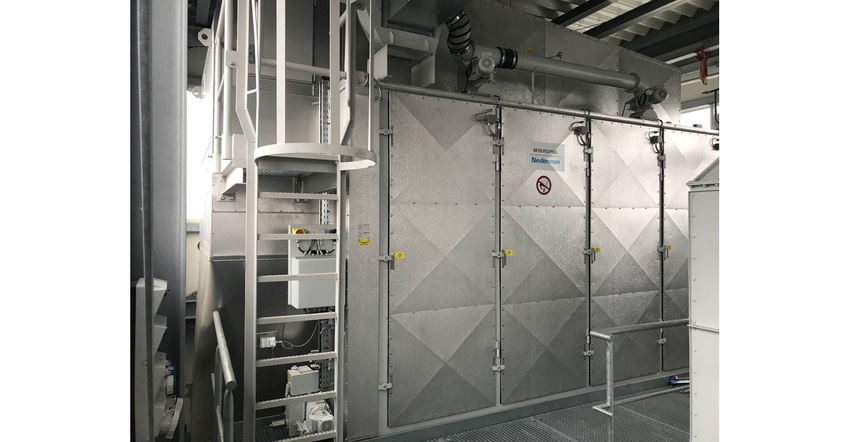
Albert Huthmann GmbH & Co. KG, a pioneer in waste recycling and underground landfill, launched a comprehensive plant expansion initiative by building a new intake and treatment sluice supplementing the capacities of the four existing processing plants. These facilities, which are equipped with state-of-the-art machines for screening, shredding, scrapping, sorting, moistening, and mixing, can process different types of waste.
The company primarily deals with residues originating from waste incineration plants, biomass, or other solid fuels, as well as from foundries (foundry sands, cupola furnace dust). These residues are predominantly in the form of dust or small particles, constituting dry bulk materials. The residual materials are often contaminated with metallic scraps and other substances, some of which can be separated through processing procedures. Filter ashes may contain toxic or carcinogenic substances, posing added challenges for safe handling. Huthmann’s commitment to environmental and occupational health and safety is demonstrated by advanced processing techniques that ensure compliance with strict regulations.
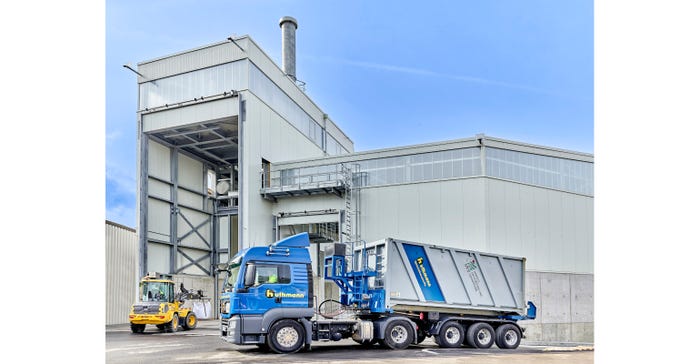
FS baghouse system seamlessly integrated into Huthmann’s waste processing facilities (image courtesy of Nederman MikroPul)
Processing and Recycling
Huthmann’s processing facilities have highly efficient machinery that converts various types of waste into valuable secondary raw materials. Carbon-containing residual materials in particular are processed on site into quality building materials that meet recognized standards and are subject to strict controls. The company's commitment to environmental protection and resource recovery is underlined by the integration of a reverse-air cleaning filtration system from Nederman MikroPul.
Integration of Small-Footprint FS Filtration System with Reverse Air Cleaning
As part of its commitment to sustainability and environmental responsibility, Huthmann selected and seamlessly integrated the FS filtration baghouse system into its waste processing facilities. The baghouse is compact with a small footprint and is located inside a dedicated unloading hall. The baghouse system ensures the efficient capture and filtration of dust generated during the unloading and treatment processes. As a boost to the company’s sustainability profile, the FS baghouse uses a low-pressure automated cleaning system that does not use compressed air.
The use of plant-wide compressed air can waste energy due to leaks and overuse for the application. Huthmann has avoided the use of compressed air in its FS filter implementation while maintaining filter efficiency. This has a positive effect on its carbon footprint. An added benefit of the FS cleaning system has been the filter bag life. The original bag set is now over four years old. The lower impact on the baghouse components has also reduced the demand for spare parts to ensure uptime. The FS baghouse is a robust preventive measure against environmental pollution in the surrounding community.
The Result
The fusion of advanced waste processing technologies with the FS filtration system has improved overall operational efficiency and environmental performance for Huthmann. The company successfully manages diverse waste streams, produces valuable secondary raw materials, and adheres to strict environmental standards. The integration of the FS filtration system into the unloading hall not only optimized waste processing, but also created a controlled environment that prevents dust contamination, while reducing energy use in a circular economy setting standards in responsible waste management.
For more information, contact Nederman MikroPul (Charlotte, NC) at 704-736-3593 or visit www.nedermanmikropul.com/en-us.
You May Also Like